Simple water quality test will unlock the ‘dirty secrets’ of a failing heating system
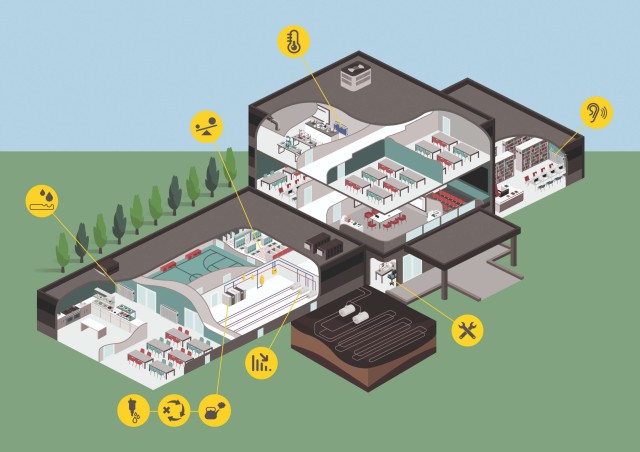
Water is a heating system’s cheapest component. Keep it in prime condition and the installation could run smoothly for years. Neglect it, and the consequences will be costly. Here, Steve Simmonds, from Spirotech, discusses some typical water woes, and explains how water quality testing can reveal a system’s dirty secrets.
Water might be the cheapest component in a heating system, but it is also the most important, and maintaining it in prime condition should be of paramount concern for anyone involved in facilities management or system design.
Too often dosing it with chemicals is seen as the answer but this is usually just a temporary fix, and not really a fix at all.
Many of the issues impacting on a heating system’s performance can be traced to its ‘lifeblood’, the system fluid.
A proper examination can reveal whether the problem lies in the water itself, such as dissolved gasses or magnetite, or that the cause lies elsewhere, such as poor hydronic balancing.
Of course, the best solution is not to let it happen in the first place. Thankfully, the industry is increasingly recognising the benefits of installing deaeration, dirt separation, degassing (including the powerful vacuum degassing), and pressurisation equipment.
When correctly specified, properly set up and regularly maintained, this will avoid the difficulties associated with air and dirt particles that lead to problems such as corrosion, erosion and bacterial contamination, to name but a few.
It should be remembered that the quality of the water is determined during the design of the system.
Unfortunately, when an installation is being designed a lot of attention is given to expensive components, but often it’s forgotten that the water quality is a determining factor for the final output and lifetime of the installation.
To ensure good water quality, a total solution needs to be designed according to the specific system.
Heritage issues
Of course, not all systems are new. There are thousands with what we will call ‘heritage issues’, where the technology has become outdated or the equipment is ageing and it’s beginning to show.
Typical indicators include problems such as boiler kettling, noisy pipework, cavitation resulting in poor circulation, pump inefficiency, cold spots in radiators and leaking AAVs.
In seeking a solution any course of action to rectify the situation should include a water quality test. In fact, this would be a good place to start.
Testing can range from a basic sampling and laboratory analysis with initial feedback, to a full interrogation and in-depth 30-section report with specific recommendations.
The test can be done at any time but should be part of a regular service agreement. If the site does not have an agreement in place the chances are the water will not have been tested.
And, what is it testing, you ask? The test is a benchmark against the recommended levels of pH, conductivity, water hardness, and if there is any protector present.
The results from these will help in putting a plan together to tackle the two main issues of corrosion and scaling.
Corrosion and scaling
The first indicator is the pH value, which is a very basic water parameter. It indicates whether the water is acidic, neutral, or alkaline. A pH of 7 means the water is neutral, below 7 it is acidic, above 7 means it is alkaline.
The effects of a certain pH value essentially depend on the material used. For example; ferrous (indicates a compound that contains iron) materials, such as in pipework and radiators, tend to corrode at pH values below 8. In contrast, these materials feel much more comfortable at values of 9, 10, or even above, and the risk of corrosion decreases.
Aluminium materials do not like pH values above 9. However, many manufacturers now use alloys that can tolerate 9.5, but from then on there is a real risk of corrosion.
For copper, it slowly becomes uncomfortable at pH values above 10.
Conductivity can be used as an indication of the rate of corrosion. The more ions present in the system water, the faster the rate of corrosion. These conductive ions come from dissolved salts and inorganic materials such as alkalis, chlorides and sulphides.
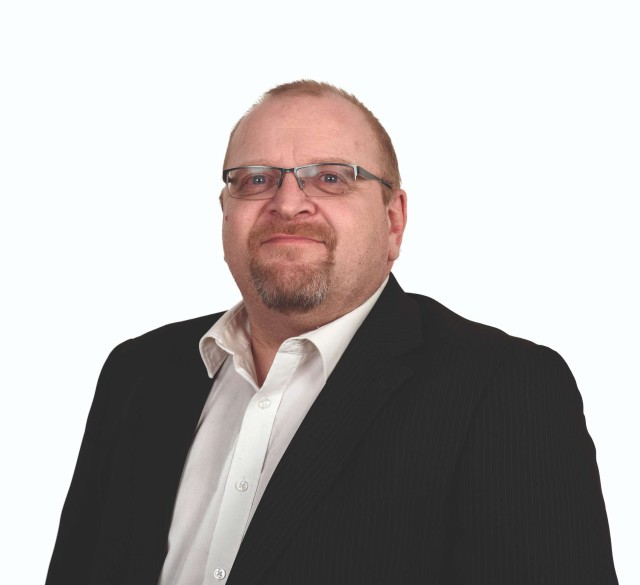
To improve water quality and reduce corrosion, you would need to reduce the conductivity.
Water hardness varies across the country, but there is always a level of scaling, which is higher in hard water areas.
Scaling is a function of the presence of hardness components such as magnesium and calcium, and these are deposited as the temperature increases, affecting the highest temperature areas such as heat exchangers the most.
This has a direct impact on boiler efficiency and, of course, the problem is proportional to the volume of the system, so larger systems are more greatly affected.
To prevent scaling on commercial systems over 600kW, the European standard VDI 2035 recommends the removal of all hardness formers to eliminate limescale deposits through demineralization.
For smaller systems, and domestic applications in general, then water softening is a viable alternative to remove primarily the calcium and magnesium via an ion exchanger.
Whichever method is used, the conductivity of the water is reduced. As demineralisation can also remove chlorides, this method also helps reduce corrosion.
Test results
Depending on the results of the water test, recommendations could range from a mechanical solution, such as the fitting or replacement of a pressurisation unit, vacuum degasser (for the elimination of microbubbles and dissolved gases) or a dirt separator, to a chemical ‘dosing’ solution or a demineralisation solution.
Another good reason for carrying out a water quality test is that many HVAC manufacturers will only offer a warranty if the system water meets certain standards.
In the UK the standard is BG 29/2020, as promoted by BSRIA (the Building Services Research and Information Association). According to the standard the system fluid should be compliant to:
- A pH value (measuring water acidity) of between 8.2 and 9.5
- Hardness 0 °dH (degree of hardness)
- Electrical conductivity (the ability of water to pass electricity) no higher than 100 µS
- Minimal microbiological activity
This requirement is in place to avoid scaling and corrosion, and which is a key issue where there is high conductivity in water. The more ions present in water the faster the rate of corrosion.
When this occurs, the plantroom equipment becomes less efficient and increases the fuel consumption of the system.
Ignoring the BG 29/2020 guidelines is likely to increase the system’s dependence on continuous dosing; but this would mean the symptom was being treated as opposed to the cause.
So, in summary, a water quality test could be the key to unlocking the ‘dirty secrets’ of an inefficient heating system and opening the door to better water quality management, the benefits of which are:
- Reduced corrosion of metals within the system
- Scale formation is inhibited
- Primary plant equipment is protected
- Lower maintenance
- The opportunity for microbiological organisms to grow is lessened
- Increased system lifespan and efficiency.
CPD and solutions guide
To further support estate managers, specifiers and M&E contractors, Spirotech has launched a new CPD ‘Understanding Water Quality & Total Solutions’.
Presented by a member of our technical team, it looks at common problems caused by poor water quality, from balancing issues and pump inefficiency to kettling and poor circulation.
Other topics include hydronic stability, the latest regulations and guidelines, how water conductivity causes corrosion, and the impact of hard and soft water. Bacterial contamination is also covered.
We have also created a 16-page ‘problem solving’ guide, ‘Best in Class Heating’, which explores the issues that can arise in heating systems, whether it is a refurbishment or a new-build.
Steve Simmonds is Specification Manager at Spirotech