Employees are back in the office, and HVAC equipment must be prepared for them
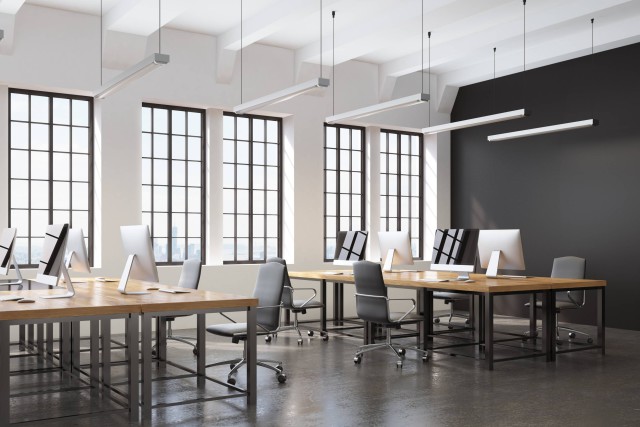
With occupancy levels at their highest than at any other point during the pandemic, now is the time to make sure building systems can start working at full capacity again. Brian Beetson of Mitsubishi Electric looks at how.
From national lockdowns to more recent hybrid working models, the majority of office and building managers have been forced to adapt their office spaces a number of times in line with changing Covid-19 restrictions in recent months. However, with all restrictions ending in England, workers are now back into the office in varying capacities. In fact, 50% of companies are reportedly expecting employees to return to the office five days a week in the coming year. With occupancy levels at their highest than at any other point during the pandemic, now is the time to make sure building systems can start working at full capacity again.
The majority of buildings have been closed for long periods of time, or have only welcomed back office-workers two to three days a week at most. With office occupancy likely to fluctuate more than pre-Covid, there may be concerns about the performance, maintenance and function of heating, ventilating and air conditioning (HVAC) equipment over the next few months.
The questions we need to ask are: -
- Will equipment be able to perform to pre-lockdown standards?
- What if certain components need replacing after having been switched off for so long, or begin malfunctioning once they begin working at full capacity again?
Luckily, there are ways of ensuring building equipment gets back up to speed effectively and efficiently to cope with the new demands of office spaces. By assessing and evaluating the performance and integrity of HVAC systems early on, building owners and facilities managers can ensure equipment is prepared in time for the office return.
Requirements have changed
Over the last two years, each industry has been affected by Covid-19 restrictions differently, and each building and HVAC system will have been working at varying capacity depending on the sector.
For example, medical facilities like hospitals or doctors’ surgeries will likely have had equipment such as chillers working overtime, meaning the facilities team looking after that equipment is well aware of the importance of establishing a good service and maintenance regime.
However, in buildings like offices a lot of equipment will have been working at 10-20% of capacity or may have even stopped operating completely. As such, facilities managers employed in these sectors are more likely to need to prepare their systems for a gradual reopening in the coming weeks and months.
Areas to consider
While it’s important that building equipment is back up and running to its optimal efficiency for when people head back to the office, it’s not as straightforward as simply switching them back on once buildings re-open.
For example, while equipment like chiller systems is an important part of creating a comfortable environment for occupants, today's modern chillers are highly advanced machines, and require more preparation than simply restarting when office workers return.
So, as buildings re-open, it’s important to think about the key considerations to bear in mind, and to also consider what steps can be taken to ensure that systems don’t fail or malfunction just as people return.
Practical solutions
Re-starting redundant systems will use up energy and could exacerbate any existing issues with older equipment, leading to a potential power surge or even overall system failure. Therefore, it’s important to take a practical approach when preparing HVAC equipment for the office return.
Firstly, it's not a good idea to restart systems on the same day of the building reopening, or the final few days before. In reality, equipment like chillers should be turned on well in advance, giving them time to run from 0% back up to full capacity.
It’s also important to run a system check on your equipment, especially in buildings that have either been unoccupied for some time, or experienced fluctuating periods of occupancy. When evaluating the performance of a chiller, for example, it’s essential to not only check refrigerant levels, but to also assess everything from the calibration of temperature and pressure sensors, to heat transfer from exchangers. This will help avoid potential power surges when buildings begin operating at full capacity, it’s also an opportunity to focus on the system’s efficiency and either initiate any repairs required to increase performance, or plan for a complete replacement if needed.
If after running a system check a component turns out to be non-functioning, it’s worth bearing in mind that replacing old equipment doesn’t have to take a long time. Lots of equipment is now easy to order at short notice, with modern, inverter-driven modular chillers available to order up to 48 hours in advance. This means you can get your systems up and running in no time at all, and don’t have to worry about any unexpected delays to the office return.
Once systems are back up and running to working at full capacity, it’s also worth getting in touch with the maintenance team and running a final evaluation of all working equipment, to make sure everything is working as expected.
Planning for the long-term
While it has been important to ensure equipment was ready for offices reopening, it is also crucial to make sure that systems are checked and serviced at regular intervals for the long term. This can ensure that equipment continues to function effectively and efficiently long after the office reopens, and minimises any later disruption to office occupants.
For example, establishing a clear framework like a planned preventative maintenance (PPM) programme can help identify and prevent faults as they arise, and help to optimise the operation and performance of HVAC equipment by extending the overall product lifecycle.
Remote monitoring technology, for example, can also allow for regular checks of how equipment is performing equipment from afar, by attaching sensors to the equipment and feeding back relevant data. This alerts engineers to any minor faults before more serious issues occur, and they can be addressed quickly as they arise. This is far more cost effective than remedying problems once they have already started to impact building occupants, and also reduces the overall risk of equipment failure in the long-term.
So, while it’s important to make sure equipment is back up and running for when occupants return, it’s also vital to regularly service and maintain this equipment in the weeks and months ahead once systems start running at full capacity again.
Ensuring a safe and healthy return
With occupancy levels expected to increase in the coming weeks or months, it’s important to run checks on existing systems in advance, and restart equipment in a steady, controlled manner.
While there’s certainly no fool-proof guide to navigating the office return, there are a series of steps that facilities managers can take in order to prepare their buildings for increased occupation again-while also improving efficiency, tackling rising energy costs and reducing carbon footprint.
By preparing HVAC equipment now, building owners and facilities managers can help ensure a safe and practical return to the office environment later, and navigate this ‘new normal’ in the weeks and months ahead.
Brian Beetson is National Sales Manager for Service and Maintenance at Mitsubishi Electric