Making the most of heat recovery
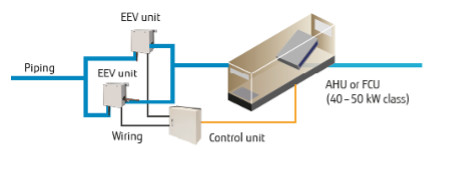
Martyn Ives, Distribution Sales & Technical Services Director at Fujitsu General Air Conditioning UK, highlights the importance of unlocking the full potential of HVAC systems.
Environmental concerns, increased awareness of the importance of indoor air quality and the current impact of soaring energy costs mean there is a greater need than ever to re-examine the way we heat, cool and ventilate our buildings.
Air conditioning is still seen by many as simply a way of cooling occupied space, even though the advent of heat pump technology as long ago as the 1970s created the opportunity to incorporate heat. The importance of making the most of a system to meet the needs of a building has now taken on even greater significance and, with a little imagination and guidance, we can realise the full potential of efficiency through heat recovery.
When we look at the functions and features of any building, we see a mixture of services; air conditioning that regulates the temperature, boilers generating the hot water and air handling units (AHUs) introducing fresh air whilst removing the stale air and keeping CO₂ levels acceptable. All require their own sources of energy, be that gas or electricity. Through understanding a VRF heat recovery system, and informed planning at the outset, energy recovery can be realised across many different types of products.
Air conditioning systems typically move energy from one space to another, for example, removing heat energy from a room and transferring it to the ambient air using refrigerant as a transfer medium. Energy is consumed by the compressor and fan operation, with the ratio of energy consumption to energy produced used to calculate the system’s efficiency. The higher this ratio, the more efficient the system and the lower the cost of operation.
Minimising costs
To minimise a building’s operating costs, we need to generate as many different uses from each piece of equipment as possible, understand the design potential and employ a control strategy that will be optimised for efficiency gains. Using the energy removed from one process and utilising in another is a core component in achieving this.
Modular VRF air conditioning offers a flexible design solution in terms of space-saving and high efficiencies. A heat recovery system can be very efficient when installed with typical fan coil units, using the energy removed from rooms operating in cooling mode and rejecting in rooms operating in heating mode, rather than outside. In principle, this increases the amount of energy provided in ratio to that of the energy consumed. This type of energy-saving is maximised in the UK during the intermediate seasons of spring and autumn, when the building uses the system in mixed mode to satisfy different requirements.
Taking AHUs as an example, these can, in most cases, include a direct expansion (DX) or hydronic coil to provide either the tempering of fresh air or extend to full air treatment. A typical AHU would generally have a cooling coil to lower the air temperature and reduce relative humidity, making it suitable for introduction into a building. The airstream would be then reheated when needed to raise its temperature, again meeting requirements for the supply. In traditional circumstances, the cooling operation would require energy consumption and the heating operation would then require further energy consumption.
Benefits of heat recovery
When we apply heat recovery to this type of design, it means we can remove energy in one heat exchanger, cooling the air and lowering relative humidity, then transfer that energy through the refrigeration circuit and reintroduce it via the subsequent heat exchanger operating in the heating. The only power requirement from a compressor point of view would be enough to provide the cooling side of the system – heating would be provided at a little or no extra cost.
The use of an air conditioning system as a method of climate control within an AHU generally outweighs other methods in terms of both efficiency and installation costs. It is also an important alternative if the site in question has a limited electrical supply. Power requirements of electric heater elements are demanding and in comparison, air conditioning has low start-up currents, inverter control, and significantly better output to input energy ratio.
Integrated heat pump systems specified within AHUs can be a worthwhile accessory, but such valuable energy-saving functions as pre-heating a building before occupancy on a cold morning, without introducing cold fresh air, are limited. This is because both condenser and evaporator are mounted within the AHU air stream, limiting the recirculation aspect. External solutions can remove or add energy to the airstream because energy can be absorbed or rejected from outside the AHU via the air conditioning system’s outdoor unit.
So how can we maximise the benefits? By using a heat (energy) recovery VRF system instead of a heat pump and recovering the energy expelled or absorbed by each type of DX coil to be used elsewhere. For example, the energy absorbed by a coil used for dehumidification, and therefore cooling the air, can be diverted and used in the coil that is providing the air re-heat, or pre-heat, rather than expelling outside.
Expanding a single system to include multiple AHUs will further increase the energy recovery potential. If we combine to include fan coil units, we extend the possibility of mixed operating modes across the system. Remember, any ratio of mixed operating mode on a heat recovery VRF (cooling and heating at the same time) results in higher system efficiencies. It is simply a case that a greater system capacity is produced with less relative energy consumed.
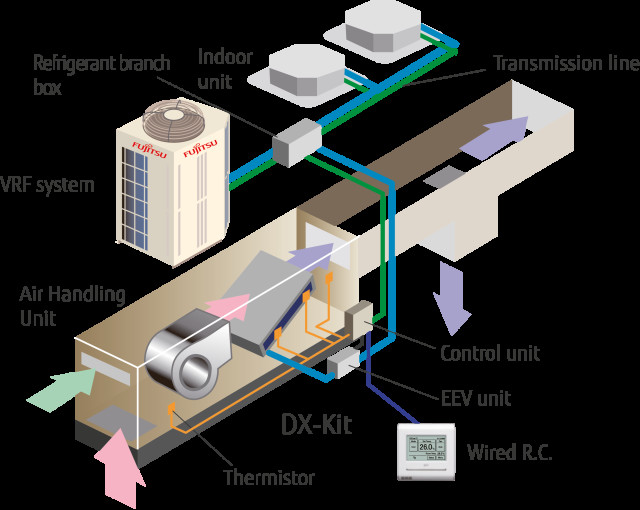
Process
Comprehensive solution
The Fujitsu DX Kit is a simple yet comprehensive solution providing heating and cooling to ventilation systems from an air conditioning product. It enables other manufacturers’ AHUs and fan coil units to be incorporated into a VRF system, or be connected to a VRF outdoor unit to control outside air ventilation or room temperature. A unique operating range allowing air on coil down to -7°C in heating allows the removal or significant reduction of pre-heat and frost protection, resulting in high-cost savings for operation and significant environmental benefit in CO₂eq emissions and the removal of fossil fuel products.
In addition, the capability to join electronic expansion valves in a parallel piping configuration allows an unprecedented 50kW heat exchanger capacity whilst maintaining precise control for capacity staging across multiple heat exchangers, multiple ventilation systems and heat recovery applications.
To put the potential benefits into context, a recent project to replace a chilled water system at a Primark store in Manchester saw an outdoor VRF unit serving multiple heat exchangers in each AHU. The heat exchangers provide staged cooling/heating capacity, with two VRF systems for each of the six AHUs, each with 2 / 3 stages of cooling or heating as required.
The system reaches operating efficiencies of up to 3.46 EER (cooling) and 3.67 COP. In comparison to the chillers that were removed, operating at an EER of 2.0, this equates to an operational saving of up to £10,757 for full load cooling operation plus a potential £2,000 per AHU in the removal of expensive pre-heat coils. This is expected to be extended further due to the inverter and load control nature of the new equipment. Using Standard Assessment Procedure 10.1, the new installation has reduced the site’s environmental impact by an equivalent 8,606 kg CO₂ per year annum in cooling operation alone.
In addition to VRF solutions, split system kits make application into smaller specifications easier and cost-effective, spanning a range of 3.5kW to 22kW with capacity demand control.
Taking control
Controllability is another key element of integrating VRF with other applications. AHU fan speed control, defrost signalling, error monitoring and airflow detection are all examples of direct integration. Modulation of evaporating or condensing temperatures not only creates more comfortable environments, reducing temperature overshooting or eliminates draughts, but also adds to the system efficiency gains. Further connectivity to a building management system allows comprehensive integration to a wider scope of other systems for complex control strategies.
Conclusion
As an industry, we may understand heat pumps, heat recovery and energy transfer, but we also need to develop our understanding of how to make the most of what we have when it comes to system design.
Martyn Ives is Distribution Sales & Technical Services Director at Fujitsu General Air Conditioning UK