Direct electric heating: a real low-carbon alternative for construction
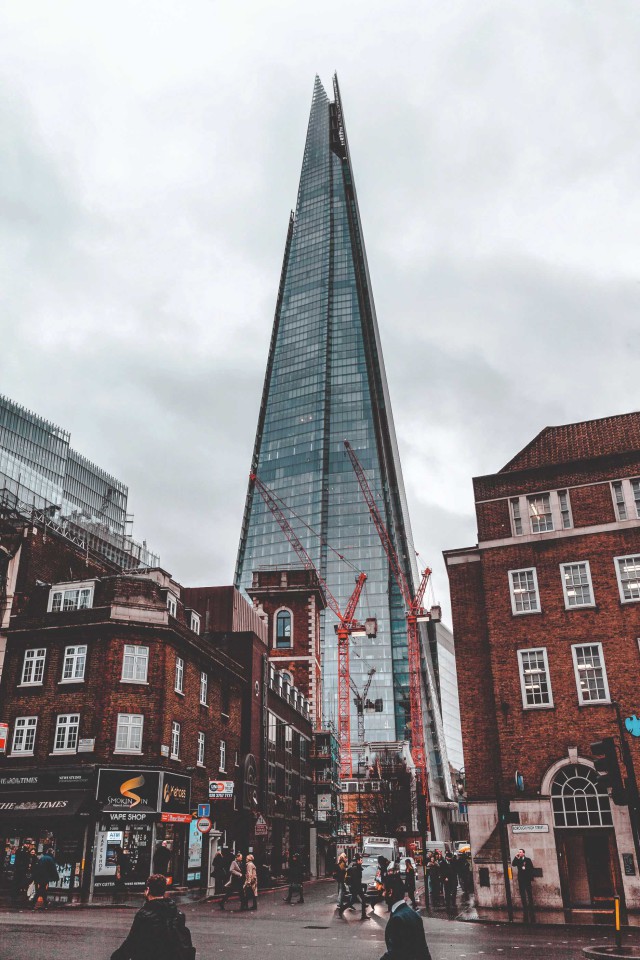
Alistair Bell, Director at ThermoSphere, discusses the mood in construction, and the industry’s opportunity for growth.
Our new report ‘Working towards Net Zero’ sheds light on the attitudes toward direct electric heating inside the construction industry, with many industry professionals preferring it as a means of retrofitting small homes and apartments.
Since the UK government set its target of Net Zero by 2050, significant efforts have been made to reduce emissions across the whole of the economy. In the construction industry that means decarbonising supply chains, replacing non-renewable energy with renewables, and using low-carbon heating methods.
The most recent Climate Change Committee (CCC) parliamentary report, published in June 2022, highlighted that for the UK to meet its target of Net Zero by 2050, at least half of the current heat demand for buildings must be supplied by low-carbon sources by 2035.
The need to change to low-carbon alternatives apply to all UK buildings, but the pressure is on residential construction to make the change. Residential homes are by far the largest contributor to UK buildings emissions. Buildings emissions make up 20% of the UK total emissions, and residential homes account for almost 80% of that. The UK construction industry has an opportunity to massively reduce the nation’s overall carbon emissions.
It is against this backdrop that the recent report has revealed important and timely attitudes towards the decarbonisation of heating and direct electric solutions within the construction industry.
The report shows that the construction sector sees the need for change. It sees insulation and low-carbon heating as essential, especially when paired with renewable tariffs. And it sees decarbonisation as both a challenge and opportunity for growth.
Priorities first
Decarbonising heat in UK buildings is not a single solution problem. There are several means of reducing emissions that can be used in tandem to reach the UK government’s goals; one size doesn’t fit all.
The report reveals that installing low-carbon heating is ranked as the most or second-most important method for reducing carbon emissions by 48% of the construction industry. Above that, efficient insulation is considered to be the top priority.
As the UK grid incorporates more renewable sources of energy, direct electric heating has become a viable low-carbon heating method for construction. Ultimately it is the electricity grid’s ‘generation mix’ that determines the carbon intensity of any form of electric heating. So, as renewables continue to replace fossil fuels, electricity is becoming a low-carbon source of energy. Eventually, the generation mix will greatly outweigh oil or gas in favour of renewables.
Pairing a direct electric heating method, such as underfloor heating or electric radiators, with a renewable electricity tariff, will prove to be one of the most effective ways of decarbonising heating in residential and non-residential settings. The construction industry doesn’t generally have control over the tariffs used in residential and non-residential settings, but they do have control over the heating solutions they install. Using direct electric will set the stage for UK housing stock to transition to low-carbon heating as electricity becomes greener.
Forward-looking retrofitting
New homes need to be built with low-carbon heating methods. But, without replacing and retrofitting older homes with low-carbon alternatives, it won’t be possible to meet the Net Zero target.
There are 29 million UK homes that need to have low-carbon heating methods retrofitted by 2050, which is one of the main priorities for the Climate Change Committee (CCC). As the Working towards Net Zero report reveals, this outlook is shared by the construction industry, as 62% of professionals report that retrofitting is the biggest challenge to decarbonisation.
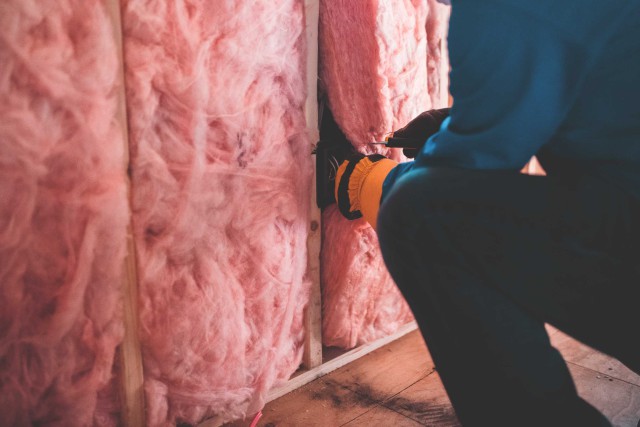
The construction industry is prepared to tackle this challenge, and direct electric heating solutions are a preferred method. Direct electric heating is seen as a better overall solution by almost half of the construction industry, second only to the use of hydrogen boilers. But, hydrogen boilers, while impactful, have a limited set of use cases, and aren’t suitable for the full range of homes in the UK housing stock.
The same is true for heat pumps. As the report reveals, 52% of construction professionals believe that direct electric heating is the right solution for modest properties and apartments, due to the fact that they’re smaller, easy to install, and do not require external equipment that would be less compatible with multi-storey buildings.
Prices are up, and so is demand
The report reveals an increase in consumer interest in low-carbon heating alternatives. But current energy prices are high and are forecast to increase in the near future. The most recent price cap increases are set to take annual average household energy bills over £3,600.
Electricity is often unfairly seen to be a more expensive form of energy than oil or gas, and this is having a detrimental effect on the uptake of direct electric heating solutions. 79% of respondents in the construction industry believe that high running costs have deterred customers from installing direct electric heating.
What’s required is a change of image. Too many people have negative associations based on old, outmoded electric heating solutions like storage heaters. 71% of the construction industry believes these older electric heating methods have a negative impact on how consumers perceive modern, low-carbon direct electric alternatives.
This need not be the case. Modern direct electric heating solutions are much more efficient than older solutions, and direct electric is 100% efficient at the point of usage, compared to gas heating where energy is lost throughout the system. They also require lower installation and maintenance costs and won’t be phased about by the UK government over the next 15 years (unlike gas).
Growth and gaps
The construction industry is keen to use low-carbon direct electric heating solutions, particularly in retrofitting older, less spacious, and multi-storey buildings. But the industry also sees the challenge of retrofitting as an opportunity for growth. 64% of those surveyed believe decarbonisation is an opportunity for the construction industry to grow.
But, as with many areas in the UK economy, there is a skills gap between the currently available talent, and the required talent. 69% of construction workers believe that while there’s an opportunity for growth, there isn’t sufficient workforce expertise to embrace that opportunity. What is needed is a concerted effort to upskill the current workforce. If the industry can do this sooner rather than later, it won’t miss the chance for growth and it will more easily meet its decarbonisation goals.
Crucially, direct electric poses a less of a challenge to upskilling as compared to other low-carbon heating methods, such as heat pumps. Direct electric involves less paperwork, and is significantly easier to install, particularly in buildings that have restricted space. The upskilling requirement, therefore, will be significantly less onerous for the industry, meaning direct electric heating offers a route to more readily embrace the opportunity for growth.
Over the coming decades, the construction industry is on track to transform. Heating solution providers that offer viable, low-carbon alternatives can help to usher in that transformation.
For more insights download the ‘Working towards Net Zero’ report: www.thermosphere.com/working-towards-net-zero-press