Ongoing maintenance is key for working buildings

Simon Plummer, Divisional Manager for Axials at Nuaire, says ongoing maintenance is key for working buildings to remain safe and compliant when it comes to smoke management and fire safety.
Many people are surprised to learn that in fire situations, most fatalities suffered are due to smoke, not the actual fire. In 2021 over a third1 of fire-related fatalities – where a cause was known – were down to people becoming “overcome by gas or smoke” and yet still smoke management in buildings is, unfortunately, a thing that isn’t seen and therefore misunderstood.
Smoke is a product of fire and should therefore be treated, in terms of safety, as seriously through the building management system (BMS) and fire safety alarm system - not just at the design and specification stages of a build, but right through the whole process including installation, testing, maintenance, and service.
Smoke fans, or high temperature axial fans, have been supplied to the marketplace for over 40 years. They are the main airflow driver with a smoke control system and respond to alarms but before 2005, not all fans were created equal.
Older standards set out that high temperature axials, and the motors on which they run, could be certified by the factory where they are made, not necessarily independently, meaning there was room for problems to occur. As a result, worryingly many of these fans may now not be fit for purpose.
With the new regulation in the Fire Safety Order and Building Safety Act (PAS 8670), the rules around testing and compliance have positively now changed. Nowadays all smoke fans need to meet set building legislation and be certified to EN12101 Part 3 to be specified. Performance is now independently tested by third party test houses and independent factory audits are conducted through the BSI, meaning that fans going into new builds are up to the job.
Disturbingly though, these standards are not retrospective and where a building has a pre-2005 fan installed, there is no legislation to say that it should be replaced. Emergency use fans for heat and smoke control systems, manufactured for safety-critical operations, should be replaced as a good practice every 25 years and yet we know that isn’t the case.
It is unfortunately common that when a building is finished and handed over to facilities management teams problems come...
As smoke control fans and their associated motors are a life safety product, maintenance rules differ from those applied to normal fans. Anything that operates on the alarm system must be tested periodically and maintained accordingly – in this case, prevention really is better than cure. We wouldn’t dream of running a car for five years without a service or MOT and yet we are just assuming our smoke management systems are working as they should without regular testing.
Fan maintenance and servicing are often overlooked or put off as it isn’t as straightforward as simply testing the smoke alarm works each week. These fans are often hidden away – in ceiling voids, up on roofs, or stuck up inside a riser – so are easily missed, or simply too inaccessible for a maintenance engineer to reach.
Smoke control fans often only run during testing or if called upon to perform a primary smoke control function. Dual Mode fans will also work however, to ventilate a building as well as perform this role and as a result, will see more wear and tear on the fans over time. This means, that as a critical component within the building, steps must be taken to ensure that they operate effectively during an emergency as well as day to day, known as the “smoke control duty”.
When looking at any testing of these fans, it’s important to think about how a building functions over time.
It’s rare for a building to be continually used for the same purpose as it was originally designed, and yet as these changes occur and office layouts change, the occupancy levels change, we often don’t stop to think about how these changes might affect the safety systems within the building.
Along with building changes also come personnel changes and unless thoroughly handed over by conscientious facilities teams, service histories and maintenance records for axial fans get lost and in time, the maintenance gets forgotten.
We need to offer more support and guidance to these facilities teams to ensure our fire and smoke systems are safely maintained. Building occupants take for granted that this maintenance is happening and deserve the reassurance that the smoke fans designed to keep them safe in case of a fire perform as they are meant to.
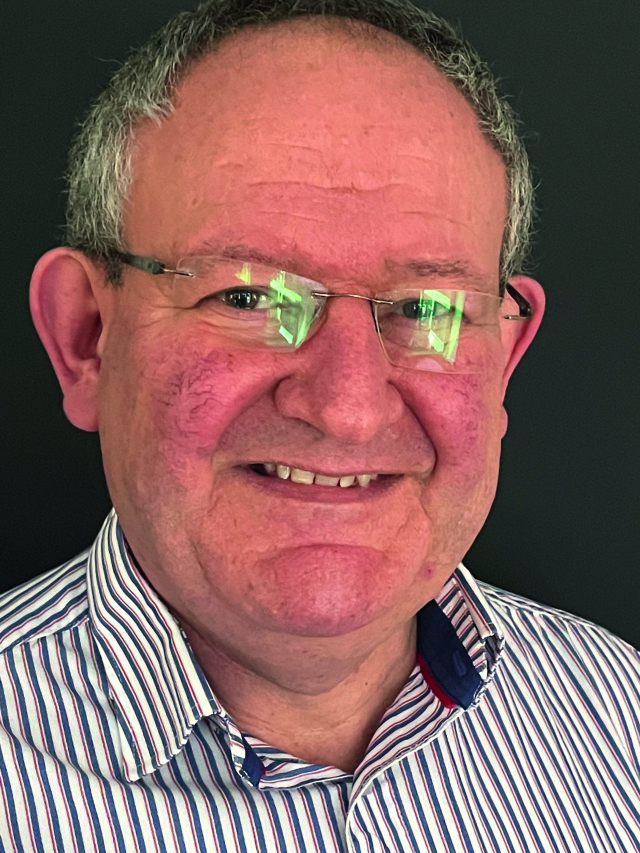
For those living with a mechanically, electrically-managed, life-saving safety system the when and how it should be tested and serviced is very much dependent on how it is used.
As a rule of thumb, if the information is available then this generally indicates that the system is being maintained but building caretakers should never be afraid to ask for clarity on when the products were made and installed, documentation for service dates, the products DoP, relevant test certificates or ask for a copy of the approved installer service scheme certificate. All these questions will identify gaps, which could save lives.
When it comes to the maintenance of smoke fans, you can’t be too thorough. I would always recommend:
1. Get set up in the right way – all building designs will have fan requirements stated within the fire strategy, make sure these match up. Determine the year of manufacture (pre- 2005 or 2005 onwards) and that the fan being used is certified to EN 12101-3. It must also have a CE or UKCA label attached. Then check you have the appropriate installation, operating, maintenance and service instructions and that a valid maintenance record exists.
2. Test weekly with the full fire safety system – the Smoke Control Association (SCA) recommendation is that smoke control systems should be tested weekly with each fan being tested at least once per week. They should be run up in accordance with the manufacturer’s operation and maintenance documentation, ideally for between 15 and 30 minutes to minimise the risk of the lubrication grease hardening and to reduce bearing corrosion. Recommended maintenance intervals are dependent on the fan function.
3. Identify weekly testing personnel - tests can be conducted by the building owner or by their nominated maintenance engineer to ensure that system will operate effectively, just like the fire alarm system.
4. Book bi-annual servicing - a regular service (every six months) of all fans by a suitably trained, competent supplier to ensure any underlying faults are dealt with. Look for a member of the SCA who specialises in fan maintenance and servicing. They will have been fully audited so you know you have a reputable engineer. Third-party certification is important.
5. Keep everything updated and accessible - Fan installation records and associated DoP documents must be held in a safe and accessible location. This will provide critical access for review by fire authorities, risk assessors, service and maintenance operatives. These records are for conducting a risk assessment of the smoke control systems. Dated and signed records are imperative.
If consultants are unsure of what fans are operating in their building or need help with regular testing, always seek the help of an expert and don’t put it off. As active members of the SCA, we have the technical knowledge and experience, held for over 60 years to provide further advice. We’re dedicated to the protection of buildings and those operating within them by producing the best standard of axial fans and post installation servicing.
The UK’s contribution to fire and smoke safety standards has been considerable and as a result of this, alongside learnings from our neighbors across Europe, we operate within a harmonised set of standards. But going forward I’d love to see the industry coming together to develop a superior set of standards, moving away from the EU Standards to offer building owners or operators a reduced level of risk and liability, while providing the highest level of smoke protection for building occupants.
To get this right, we need to identify a market-recognised qualification and training for upskilling service engineers to champion fan maintenance for smoke management in buildings. Only then will we see dramatic change and a rise in understanding of these safety-critical products.
Source
1. https://tinyurl.com/4e3ahdt5