The power of demand-controlled ventilation and smart technology for more energy efficient buildings
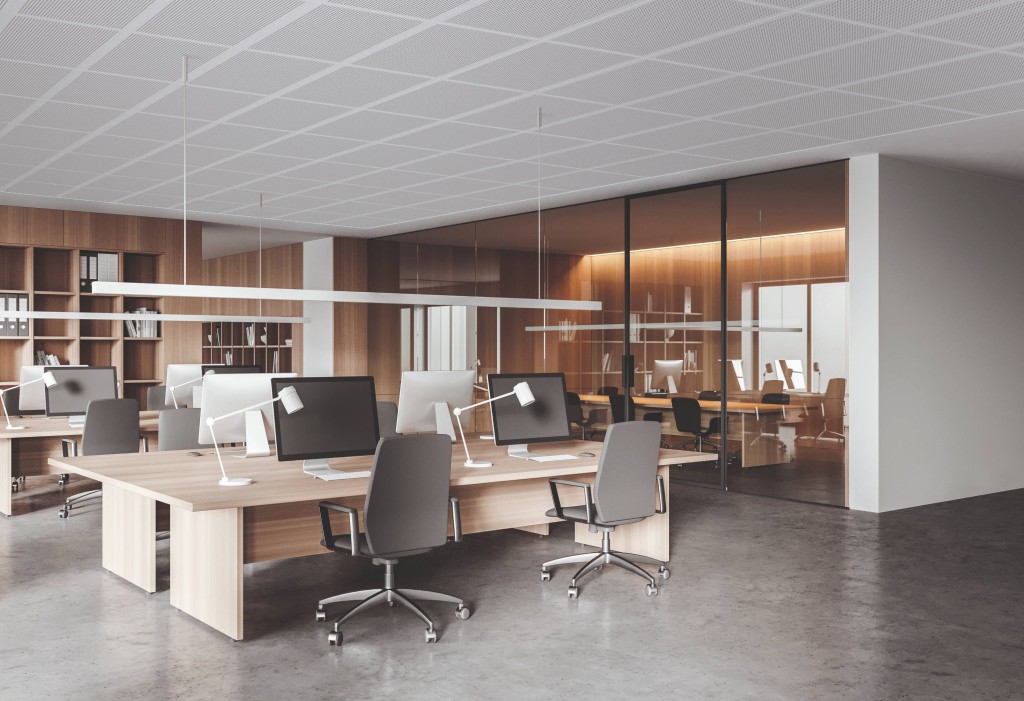
Only one-in-five buildings have an BMS system to regulate and oversee their inner workings, and so most commercial buildings operate at a Class C energy efficiency level. Stuart Smith of Zehnder looks at how to improve performance.
The UK construction industry is in the midst of a groundbreaking transformation fuelled by efficiency, sustainability and decarbonisation. This sweeping change is in perfect sync with the industry’s mission to attain net zero objectives by 2050 - igniting an intense scrutiny of every system installed within a building’s fabric, leaving no room for under-performance.
As energy costs surge higher and emissions regulations grow ever more stringent, a seismic shift is underway in building construction. These developments are creating a pressing need for substantial improvements in the calibre of our constructed spaces and, unsurprisingly, digitisation and innovative technology is leading the way.
But despite these improvements, around 80% of existing buildings adhere to outdated construction regulations. Astonishingly, only one in five buildings has adopted a Building Management System (BMS) to regulate and oversee their inner workings. Consequently, most commercial buildings right now operate at a mere Class C energy effi ciency level.
2050 targets
A critical part of achieving our 2050 targets will be renovating and retrofi tting these older structures. The incorporation of advanced controls as part of the BMS could prove pivotal in unlocking superior building performance. Building regulations, Part L (Conservation of Fuel and Power) and Part F (Means of Ventilation), have established stringent standards for buildings and infrastructure, aimed at ensuring both existing and new structures are energy- efficient and environmentally responsible. However, addressing efficiency challenges in older operational buildings is a complex challenge, with issues ranging from overheating to ventilation effectiveness and heat retention.
When it comes to the balance between energy efficiency and air quality, the majority of buildings in the UK rely on natural ventilation through high levels of air permeability. Yet the strive for more airtight properties means that building developers must carefully specify natural and background ventilation methods to provide adequate levels of air movement throughout the building.
However, if ventilation cannot be achieved to standard through these methods, a continuous mechanical extract ventilation system needs to be installed. When fitted and then controlled through the BMS of a building using current sensor technology, these systems can provide increased savings in energy and costs.
The switch to on-demand
Energy loss due to ventilation accounts for approximately one fifth of space-heating energy demand in an older, poorly insulated building, whilst in a new, energy-efficient building, the high insulation levels mean that the proportion of space- heating demand due to ventilation increases to around a third. However, natural air infiltration alone can result at times in too little ventilation. This can lead to poor indoor air quality and other, more readily visible impacts such as condensation and mould on indoor surfaces. Therefore, the bjective of a good ventilation strategy is to provide a balance between energy efficiency and indoor air quality.
Approved Document L
Approved Document Part L has been designed to accelerate progress toward net zero carbon buildings. It introduces higher performance benchmarks and places greater emphasis on low carbon heating systems. Additionally, the regulations stipulate that building services systems must incorporate suitable controls to achieve reasonable energy efficiency standards during usage.
Under these regulations, building systems are expected to respond to the specific energy requirements of the spaces they serve. Each space is treated as an individual control zone, equipped with independent timing and temperature control and, when applicable, ventilation and air recirculation rate control.
Wasted energy
Most traditional ventilation systems are mechanical and not connected to the Building Management System. They are either on or off, or work from timer controls to adapt the air flow into the building. This is problematic for two reasons; first, if the system is turned off, say at the weekend in an office space, air pollutants build up over time and the system must work harder when switched back on to purge and replenish the air within the building. And secondly, timed ventilation controls don’t adapt to fluctuating building occupation. For example; if staff work from home during the week and the building is only half occupied, the system is still running at full power and wasting energy and money.
Modern ventilation method
The installation of Demand Control Ventilation (DCV), mapped into the Building Management System is now being hailed as the modern ventilation method. DCV doesn’t just outperform traditional commercial ventilation systems; it completely redefines the game. DCV systems employ a sophisticated array of sensors capable of monitoring an array of environmental variables within a building - think humidity, temperature, carbon monoxide, carbon dioxide, motion detection etc. The objective is clear; ensure that the ventilation airflow rate is always in perfect sync with the building’s real-time demands.
A mind of its own
On-demand ventilation is the key here; it’s like having a ventilation system with a mind of its own. It responds automatically to any ventilation requirement, whether it is generated by the building’s occupants or arises from other sources of pollutants like furniture and appliances, which can create troublesome spikes in volatile organic compounds (VOCs) and other toxic contaminants.
A DCV system doesn’t wait for instructions. It takes the initiative by pumping in more filtered air when it senses higher pollutant
levels - for example, when more people enter a room. Then, when the foot traffic dwindles, it automatically reduces speed, optimising efficiency responsively. This is dynamic ventilation at its finest, effortlessly adapting to the ever-changing demands of the environment. Even when not occupied, overnight for example, the system will keep running at a low energy level to maintain indoor air quality levels ready for a healthy environment for occupants the following day.
The ebb and flow of output in the system levels out to get an ideal balance in energy efficiency and occupant health and wellbeing. Utilising on-demand ventilation will not only maintain the right level of fresh air and improves energy savings, but also lowers maintenance costs, serves superior indoor air quality to occupants for enhanced climate comfort and allows for flexible installation in both new build and retrofit buildings.
Up to 30% savings
According to recent studies*, up to 30% savings are possible using demand-controlled ventilation in open-plan offices when an average 40% of the people who work there are present and increased savings are possible depending on the environment the DCV system is serving. These efficiencies can result in cost savings in the thousands.
UK is still falling behind
However, despite Europe being the third largest energy consumer in the world and the world’s largest energy importer, the UK is falling behind in the installation of smart control technology. The consequences are both immediate and far reaching, with higher energy bills being faced by commercial consumers and significant emissions experienced across the globe.
Only 80% of commercial buildings are operating at class C energy efficiency with timer-based programming rather than sensor- based, demand orientated activation when it comes to ventilation and cooling. Smart controls can provide impactful energy efficiency and cost savings with networked connectivity and site-specific controls that monitor trends to adapt to meet site requirements. As an example; at Zehnder, we invest in smart control technology to ensure our customers see these benefits. Our commercial HVAC systems are built to the Bluetech® concept, a solution that ensures the optimal use of the system to reduce energy expenditure and CO2 emissions.
These plug and play solutions include a powerful, efficient, communicating control system that contributes, on one hand, to active efficiency for buildings (EN 15232) and on the other to potential savings of thermal energy without neglecting the climate, acoustic comfort and suitable air quality specific to each type of building.
Embracing cutting-edge control systems for these critical operations, and adopting them into the BMS as standard, empowers buildings to consistently elevate indoor air quality and optimise performance year-round, effortlessly transitioning between each season, from summer through to winter, with systems adapting to the need of the occupied space.
As an ever-evolving industry, it’s imperative that we future- proof our buildings by constantly scrutinising their usage patterns and anticipating potential changes over time. This forward-thinking approach is the key to maintaining and maximising efficiencies.
* www.sauter-controls.com/wp-content/uploads/Import-PDM/757327.pdf