Why early engagement with Net Zero pays off
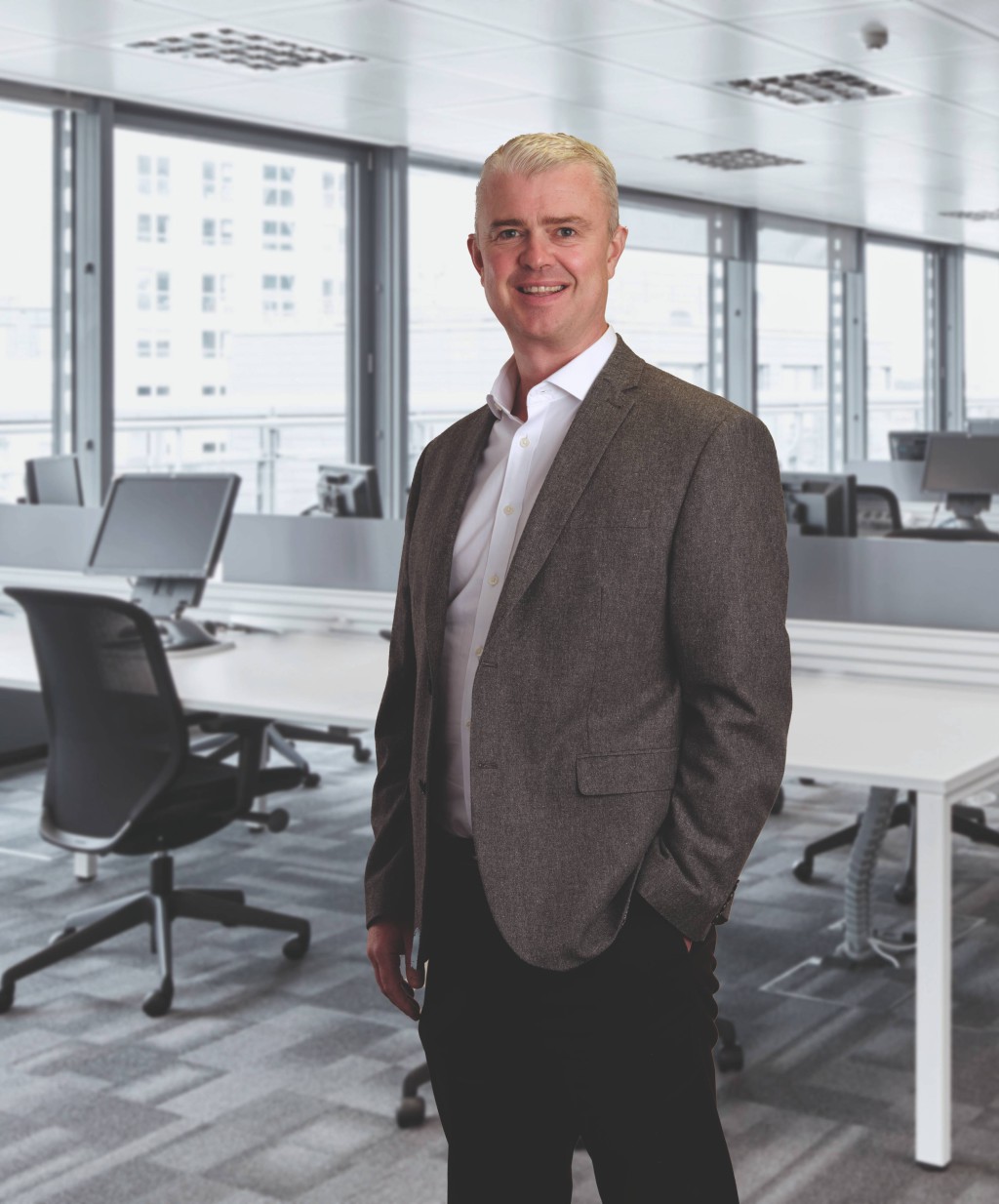
Rob Erwood, Commercial Sales and Specification Director at Baxi, looks at some of the ways manufacturers can help support the drive for net zero buildings.
With rigorous government energy efficiency and carbon targets to meet in new and existing buildings, early collaboration across the heating industry is increasingly important to achieve optimal outcomes.
As a larger energy user, the heating system is a natural focus to improve the comfort, energy performance, operational efficiency and whole life carbon emissions of a building. In recent years, design has evolved rapidly to comply with tighter building regulations. Today, a focus on low carbon design has become critical for all buildings to achieve the UK’s net zero ambition.
However, there will be any number of possible design solutions for every project, with the chosen route being dependent on multiple factors, including available time, space and budget. Just as heating design has evolved, so too has the role of manufacturers, from single product to total solutions providers.
For this reason, engaging in conversation with manufacturers at the outset can bring multiple advantages.
Specialist knowledge
Let’s consider some of the many ways in which early involvement with manufacturers can prove beneficial on a project.
First, with a full understanding of the brief, good manufacturers should be able to suggest more than one way of approaching a total solution to help you arrive at the most appropriate option. As many will offer free site surveys to evaluate the site and understand the requirements and potential challenges, it’s advisable to organise this at the outset.
Manufacturers with specialist, in-depth knowledge of their products and how best to optimise their performance can be a key support during the design and installation process. Of course, for many products, an explanation might not be necessary. But on projects where the equipment can help define and shape a solution, input from the manufacturer can play a valuable part in designing for success.
For example, when combining technologies or integrating low carbon technologies, your chosen manufacturer should be able to advise on how to achieve the most from one product without sacrificing the efficiency of another.
It’s also worth asking to see exemplar designs which experienced manufacturers will often be able to provide. While each project is unique and should be designed on an individual basis, these could prove useful on more complex heating system designs. In fact, using them as an expert resource early on could save hours trawling through technical manuals, as well as associated fees.
On a practical planning level, early project discussions with manufacturers can help avoid any delays arising as a result of product availability. A good example is the recent school refurbishment programme carried out by Oakes Energy Services for The Priory Federation of Academies Trust, where nine Remeha ASHP were to be installed across three schools in Lincoln.
Director at Oakes Energy Services, Nik Smith, said: “As with all school projects, we were working to a tight, fixed deadline. However, knowing we had the Remeha heat pumps in stock was a big selling point as this gave us more time to complete the project ahead of the start of the new term.”
End-to-end solutions
A short conversation with your chosen manufacturer can also elicit useful updates on their latest advances in technologies and solutions that may be relevant to their project. For example, in addition to supplying all the components for a heating system, some manufacturers may also be able to offer prefabricated end-to-end solutions that can make the whole project simpler.
The major benefit of this approach is the time savings. From easier installation to simpler project management and logistics, it hugely reduces the potential for delay, helping to keep the project on schedule and avoiding any last-minute hitches.
It also enables just-in-time delivery, removing the need to store equipment on site and simplifying site management.
Early collaboration with all stakeholders, including manufacturers, is key.
On multi-occupancy building projects, the end-to-end solution could involve the manufacturer supplying the central plant for a communal heat network scheme along with plug-and-play utility cupboards containing a heat interface unit and hot water cylinder for the individual dwellings.
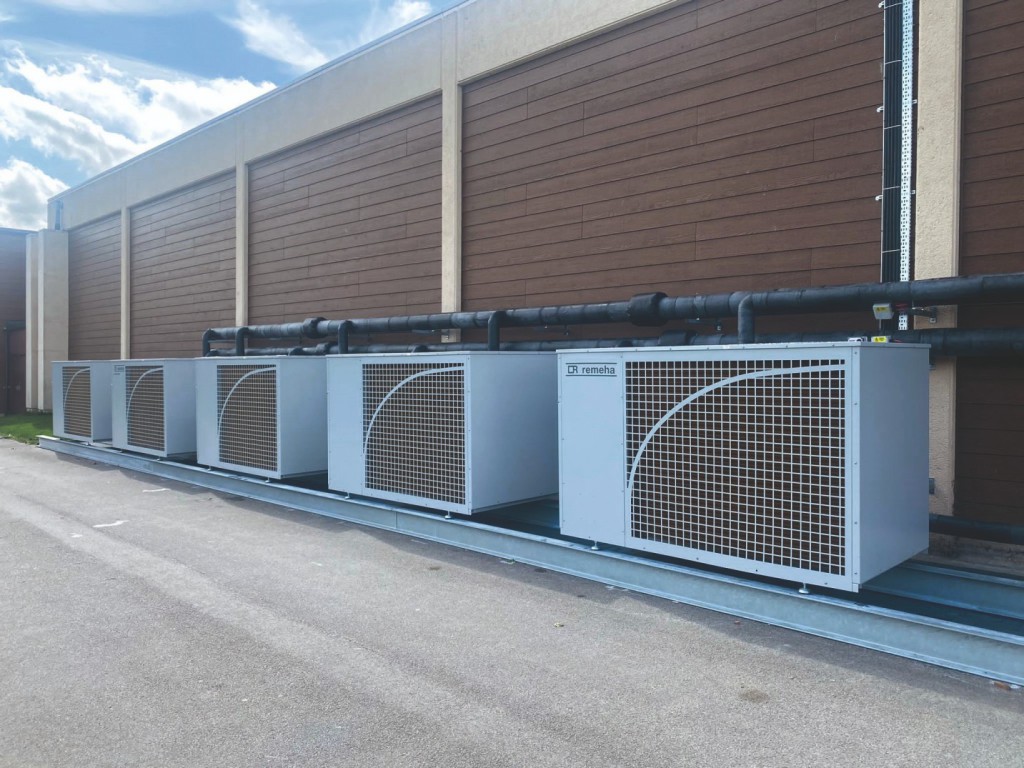
Prefabricated packaged plant rooms are another increasingly popular solution for use in both new and existing buildings. For example, early discussions about heat source revealed an area of expertise that a client hadn’t formerly been aware of during a project for Queen Elizabeth University Hospital’s Maternity Unit.
A packaged plant room was designed and built by Baxi Packaged Solutions for WGM Consulting Engineers to serve the maternity unit and during those early discussions with Baxi, its experience in providing specialist packaged plant solutions came to light.
WGM’s Project Consultant Craig Gallacher said: “The key drive behind this method was that of minimising disruption and enabling building operation at the maternity unit to keep running efficiently. The packaged plant room not only looks great, but it successfully meets the immediate and longer-term project requirements.”
Achieving embodied carbon targets
Net zero targets mean that specifiers and consultant engineers must increasingly evaluate the embodied carbon associated with the manufacture of a product. This includes the carbon embodied in its installation, transportation, maintenance, repair, replacement, and end of life. As a result of the high replacement rates and materials used in this equipment, embodied carbon can have a huge impact on a building’s whole life carbon and help accelerate progress towards net zero buildings.
This is yet another area where discussions with manufacturers at the early stages can save valuable time later. Discovering that manufacturers provide this data will simplify the carbon calculation process significantly, making it quicker and easier for specifiers to evaluate and select equipment with lower embodied carbon.
Passivhaus Certification data
The growing requirement for more detailed product data extends to buildings built to rigorous energy efficient design standards like Passivhaus buildings, which are designed in such a way that they require less energy to achieve comfortable conditions all year round.
While not all buildings built to this standard are certified, this is the best way to demonstrate that it meets the exemplary standards. Certification is a rigorous quality assurance compliance process that includes tests to ensure the targets are met. On projects like these, early conversations with manufacturers can be useful for exploring the most appropriate energy-efficient solutions and sourcing the relevant information for certification.
Passivhaus Designer and Associate Engineer at BakerHicks, David Coulter, said early discussions with Baxi on both these topics proved invaluable when gathering data for Riverside Primary School, Scotland’s first Passivhaus-certified primary school.
“It’s an exacting process,” David said. “We needed to supply detailed calculations and evidence relating to the energy values of the selected technologies.”
Those early conversations meant he had all the information required for certification and support at every stage of the project, David said.
Useful resource
From accompanying you on site surveys to offering any number of options for a selection of purposes, it pays to involve manufacturers at the early stages.
Manufacturers ‘live’ their products every day so are well placed to offer in-depth technical knowledge that can help save time and costs. They will also likely have seen a similar scenario before, along with an outcome, so can be a useful resource.
Tap into that experience. Whether you use them as a sounding board, a fresh pair of eyes, technical insight or to check product availability, it’s always worth an early discussion.