Hotels and the low carbon hot water challenge
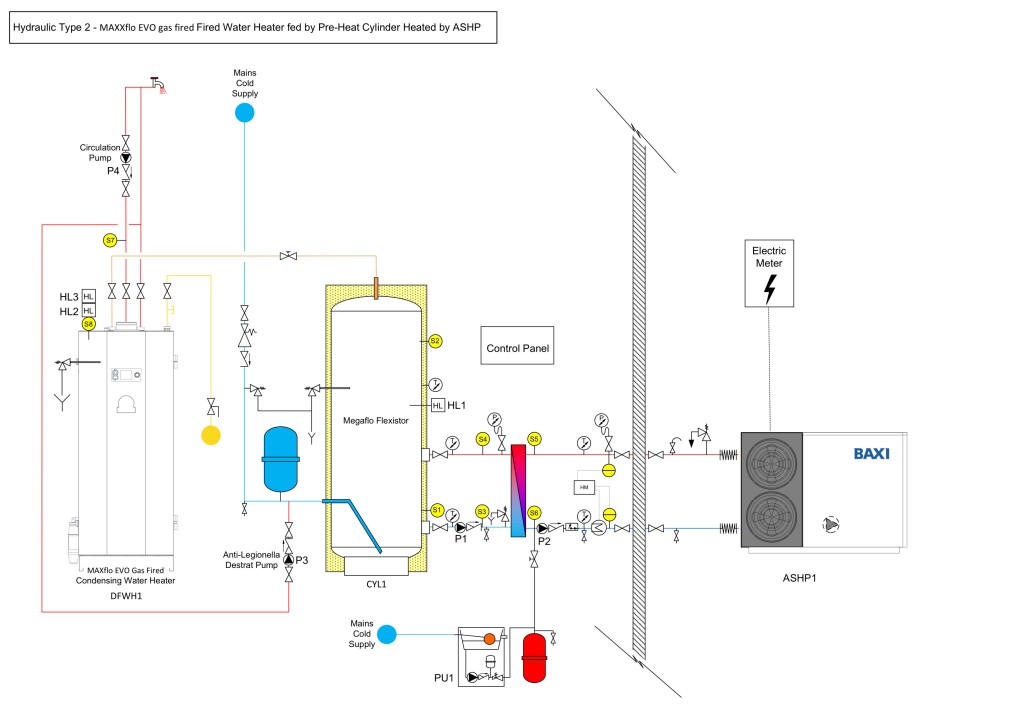
Andy Green, Head of Technical Solutions at Baxi, discusses the options for reducing the carbon intensity of domestic hot water generation in older hotel buildings and the importance of preparing for Net Zero.
As businesses and organisations face growing pressure to identify opportunities to minimise their environmental impact, hot water provision as well as heating is under scrutiny. This is particularly true in hotel building types, where the hot water system, typically associated with guest comfort, is one of the largest users of energy in the building. With 2050 Net Zero looming, the focus should be on reducing operational energy consumption and increasing renewable energy supply.
Hot water patterns
Clearly hotel buildings will have unique requirements and be at different stages of the decarbonisation journey, meaning that there can be no one-size-fits-all solution.
However, how they use hot water tends to follow a similar pattern. Traditionally, hot water usage is characterised by an extremely high peak in the morning for guests’ showers or baths, followed by a period of low demand. A second peak will typically occur in the evening when the kitchens serving the hotel restaurant will require a high demand for hot water for catering and washing down. To meet strict hygiene requirements, the solution must generate temperatures high enough to store the domestic hot water (DHW) above legionella temperatures (60oC or higher).
The challenge, particularly for older and smaller independent hotel buildings, is to achieve a system that meets the high volumes of hot water demand as sustainably as possible within available budget and time, all the while prioritising safety. With that in mind, let’s consider some of the options.
Option one: More energy efficient system
Many older hotels rely on traditional direct gas-fired water heaters for DHW generation due to their ability to meet sudden peaks in demand efficiently with reduced energy loss.
However, it should be noted that Approved Document L of Building Regulations now effectively rules out non-condensing water heater replacement in the vast majority of buildings, in favour of condensing models which are up to 20% more energy efficient. Where relevant, encouraging customers to switch from non-condensing to condensing water heaters will ensure the hot water system is more efficient and compliant, preparing it for the future addition of renewable technologies.
The hot water demand should be reassessed as part of the upgrade as this may have changed over time and could point to a smaller water heater being required, reducing capital expenditure and future running costs. There may also be the option to relocate the plant to the roof or exterior in a packaged plant room, freeing up valuable extra space.
Good solutions providers will offer free site surveys, sizing advice and technical support.
Option two: Hybrid approach
If gas is to be kept in the building, the next stage on the decarbonisation pathway might be to consider integrating an air source heat pump (ASHP) in the system to provide pre-heated water to the direct-fired water heaters.
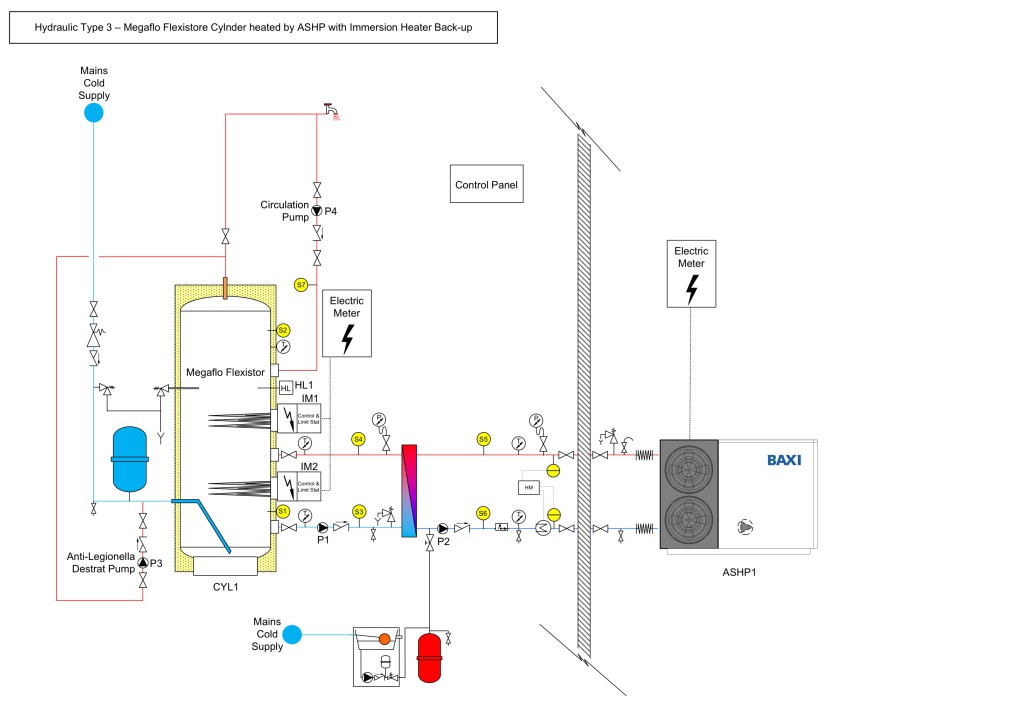
A hybrid solution is often a fast, efficient and affordable solution to low carbon hot water in legacy hotel buildings. Using the ASHP to pre-heat the cold mains water from 10oC to 50oC, with a DGFWH raising the temperature from 50oC to 60oC will deliver significant carbon savings. At the same time, using a DGFWH with built-in legionella functions like the Andrews Water Heaters MAXXflo EVO will ensure straightforward legionella control.
This design satisfies the hot water requirements safely and efficiently, greatly reduces storage requirements and ensures that the majority of demand is met through renewable energy.
Option three: All-electric approach
In new build and off-grid hotel properties, an all-electric system will be the favoured approach using a combination of electrical technologies including heat pumps and immersion heaters.
Understanding the hot water profile of the building including the demand and timings between peaks is essential to enable correct sizing. Accurate storage assessment will avoid needless energy and water waste, higher than necessary running costs, increased energy losses and space considerations. Ask your chosen solutions provider for advice on the various factors – including location, budget, electrical supply, size of cylinders – that should be considered at the outset.
One design option might be to use a medium temperature ASHP like the Baxi Auriga to bring the hot water temperature to 60oC with electric immersion back-up ensuring water safety and reliability in colder months.
In older buildings, high temperature heat pumps that use environmentally friendly natural refrigerants like R290 (propane) or CO2 provide designers with more flexible, space-saving solutions to meet the DHW supply. A major advantage of high temperature heat pumps (HTHPs) like the Baxi Auriga+ HT ASHP is their ability to deliver high flow temperatures up to 80°C to ensure adequate legionella control.
However, it should be noted that their coefficient of performance (COP) reduces at higher temperatures, affecting real-world efficiency and operating costs. As before, sizing is critical to achieve optimal performance and savings.
Optioneering
In summary, there will be many options to achieving more efficient, safe hot water provision in hotel buildings. To help designers and customers make the best choice, we at Baxi can use measured energy data to engineer a series of solutions, simulating the energy, carbon and CAPEX impact of each option. Working together we can help hotels identify the achievable opportunities for more sustainable hot water generation.