Challenging the status quo
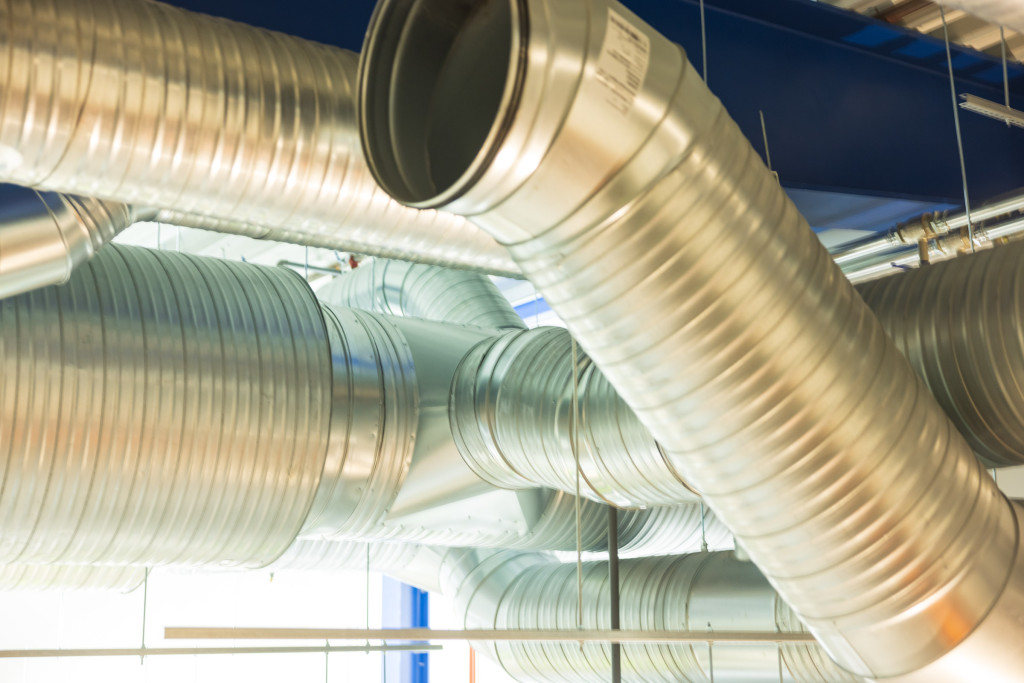
Tony Anderson, Chief Technical Officer at the Commissioning Specialists Association, addresses some important issues surrounding ductwork leakage testing.
One of the tasks that commissioning managers and commissioning engineers are responsible for on construction projects is to provide evidence that air handling units (AHUs) and fans are operating at the designated setpoint and delivering the correct airflow to the required locations in a building.
One of the most significant factors that affect their ability to provide that evidence is the standard of the ductwork installation. A poor installation will almost certainly have a much larger ductwork leakage factor, i.e. the supply AHU/fan will have to pump much more air into the distribution system to achieve the correct airflows at the outlets.
A similar outcome will result in extract systems, i.e. drawing excess air through the plant to achieve the right flows at the inlet grilles.
This creates more than one problem. The most obvious is that more time and effort is necessary to commission and prove the system. If the leakage really is excessive, there is also the cost of remedial works. Once the building is operational, energy is wasted in pumping that additional volume through the system. On supply systems, even more energy can be wasted in conditioning that extra volume. But there are also effects on element such as air quality and drafts that are rather more intangible, but nonetheless can seriously affect the operation of the building.
Part L2A of the Building Regulations in England and Wales currently states that ductwork leakage testing should be carried out in accordance with the procedures set out in BESA DW/143 and DW/144 for systems served by fans with a design flow rate greater than 1m3/s. Similar regulations exist in Scotland and Northern Ireland.
DW/144 has four classes of ductwork system, low and medium pressure (Classes A and B) and high pressure (Classes C and D) and it currently says:
“With the availability of four pressure classifications in DW/144 it is hoped that the system designer, having control over performance standards, will find air leakage testing an unnecessary contract expense with regard to low and medium pressure ductwork. The standards imposed by DW/1 44, the improved quality of sealants, modern fabrication machinery and well-defined methods of assembly on-site, all make for a higher quality of low leakage ductwork and, in the majority of cases, visual inspection of low and medium pressure ductwork will usually suffice to verify a well-engineered installation. It should be recognised that the testing of duct systems adds a significant cost to the installation and incurs a great deal of extra time which needs to be pre-planned into the contract programme.”
Up until now that has been accepted as a solid, common-sense argument for restricting leakage testing to high pressure ductwork systems to minimise the time and cost involved in the pressure testing. Is that still the case?
If we challenge that norm, what could happen? Consider reclassifying all class A systems, except the smallest and simplest as class B. Then consider specifying ductwork pressure testing of all class B, C and D system ductwork.
There is no doubt that the initial outcome would be that the ductwork installation would take longer and cost more. Both of those would have a headline detrimental effect on the overall construction program and build cost.
But let us look at the flip side. The benefits are likely to be:
Proving and documenting ductwork installation
A site leakage test would be able to prove ventilation systems are sealed – with any leakage within an acceptable range – with documented results for each system. This would be far more definite and occur prior to the system being brought into operation. If the testing did identify any excess leakage this could be rectified immediately and prior to any insulation being installed. This would obviously be much quicker and cheaper than remedial works in the latter stages of commissioning. Overall, this cost/ time saving would counteract the cost/time of the testing.
Improving system operational efficiency set points
By reducing ductwork leakage – this would improve the efficiency of airflow being transported throughout the buildings, allowing AHU or fan setpoint to be reduced.
Improving air quality and reducing drafts
Delivering controlled airflow by minimising any outside air loss being delivered to each area and the extracted air being fully removed from all individual spaces would both allow systems to be efficient and minimise any chances of cross contamination. The carefully directed and accurate airflow will also minimise the possibility of drafts. This will aid the handover process.
The above benefits will all be accrued during the construction process, but the benefits for the client/end-user also need to be considered:
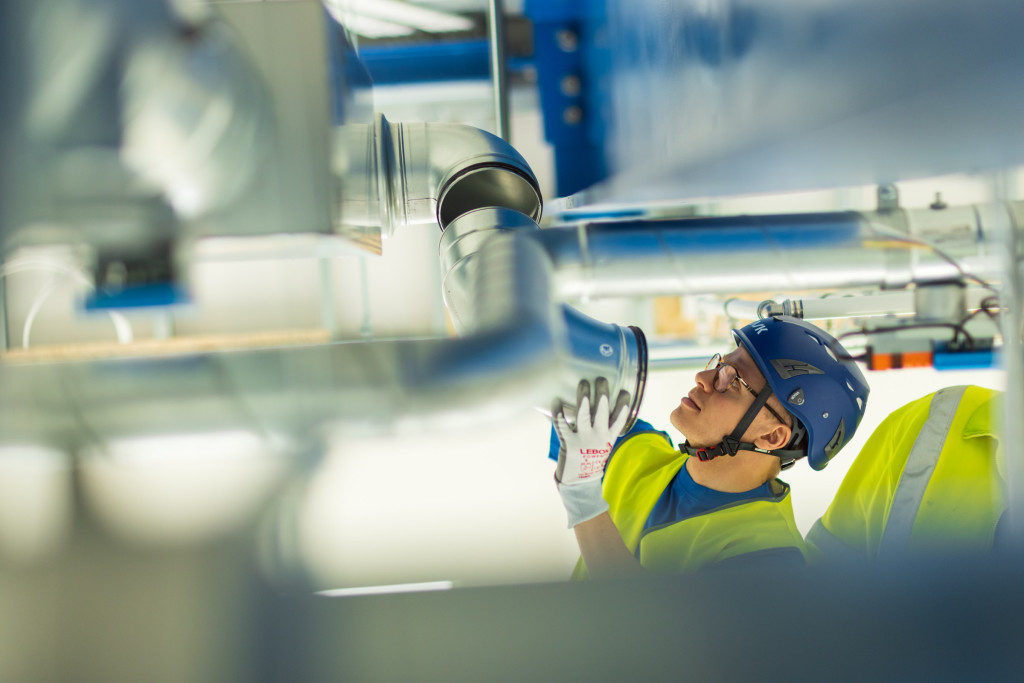
• With improved system efficiency, individual operating setpoints would be at their optimum levels.
• The whole-life cost of ventilation systems will be significantly impacted by maintenance and operational inefficiencies. Higher classifications for ductwork will inherently promote systems that are better constructed and more dependable.
• With a higher ductwork classification – Medium pressure class B – this could allow AHUs and fans to operate at a slightly lower setpoint – potentially for the life of the project.
There are benefits for the wider environment as well:
• Reduced carbon footprint – Tighter ductwork standards would directly contribute to reductions in carbon emissions by ensuring that ventilation systems operate efficiently. According to CIBSE Guide
B2, airtight duct systems are essential for meeting energy efficiency targets under the Energy Performance of Buildings Directive.
• Support for Net Zero goals – Introducing legislation for increasing the minimum ductwork classification supports the broader aim of achieving Net Zero carbon buildings by 2050.
Although it seems obvious that the testing would be an overall benefit, the practicalities of the change do need to be considered:
• Changing all classification of ductwork on-site would not be an easy task.
• The current methodologies used at site along with visual inspections are considered sufficient to prove a minimum standard of installation – even if they are not in practice.
• Although designers can insist on all ductwork being tested, any change would be difficult to implement unless DW/144 itself is changed.
The construction industry has always pressure tested all pipework systems, including open-ended drainage pipework and in recent years has introduced the pressure testing of whole buildings, so why not the ductwork?
We at the CSA suggest that now is the time for a serious conversation between developers, builders and designers and the relevant technical bodies to redefine the level of excellence required for all types of ductwork installations in buildings and lay out how to achieve it.