Keeping heat networks on the critical path

Heat networks are one of the vital components of the UK’s Net Zero roadmap, with the government targeting 20% of heat from heat networks by 2050. One way of achieving this ambitious target and successfully accelerating heat network deployment is through use of prefabrication, says Ian Robinson, Technical Manager for Heat Network Solutions at Baxi.
With no single solution to decarbonising heat, heat networks are recognised as a critical part of the UK’s plan to reach Net Zero emissions by 2050. Currently, heat networks supply less than 3% of the UK’s heat, but the government is targeting 20% of heat from residential, commercial and industrial sectors by 2050.
To grow the heat network sector efficiently and in a controlled manner, the government is regulating it and using ‘zoning’ to drive up scale. For customer protection, new regulatory technical requirements are being introduced for new and legacy heat networks. The Heat Network Technical Assurance Scheme (HNTAS) will help heat network operators demonstrate compliance with these requirements.
Where networks do not meet the requirements, mandatory improvement plans will be enforced to bring them up to the expected efficiency and carbon performance levels. The new standard will be overseen by the Office of Gas and Electricity Markets (OFGEM), appointed the UK’s heat network regulator under the Energy Act of 2023.
At the time of writing, we are awaiting the response to the recent government consultation, but the rollout of heat network zoning is expected to begin from 2025. The scale of deployment required to achieve the government’s ambitious target in 25 years is huge and the number of connections to the heat network even more daunting. Fortunately, prefabrication offers a solution to the task at hand. This article will look at how employing prefabrication techniques will enable us to build heat networks efficiently, reducing time and costs while simultaneously improving quality and keeping them on the critical path.
Benefits of prefabrication for heat networks
Prefabrication, also known as off-site fabrication, is acknowledged to offer numerous benefits over traditional installation methods. These include delivering reduced on-site labour and time and improved safety. Quality assurance is enhanced as the factory-controlled conditions ensure that the quality of work is high and consistent. Prefabrication is also more sustainable, reducing waste and improving the overall efficiency of the process.
So how does this approach benefit heat networks?
First let’s define what we understand by heat networks. ‘Heat network’ is an umbrella term to describe a shared network that provides space heating and/or hot water to multiple buildings (district heating) or to multiple dwellings, often within a high-rise tower block (communal heating).
The source, or sources, of heat for these networks is a centralised energy centre that transfers the heat to the connected buildings or apartments through insulated underground pipework. Heat interface units (HIUs) are typically used to transfer heat from the central source to the individual dwellings. Substations provide hydraulic separation between one part of a heat network and another, often at the entry point to the building.
In high density urban areas, heat networks are often the lowest cost, low carbon heating option. By supplying multiple buildings, they avoid the need for individual boilers or electric heaters in every building. Heat networks are also uniquely able to use local sources of low carbon heat which would otherwise not be utilised, for example from industrial processes, data centres, or even from rivers.
Energy centre
The shift towards heat networks will drive the rise in demand for large scale plant rooms. The energy centre of a heat network typically consists of multiple components which traditionally will need to be delivered to site in separate deliveries, where they must be stored safely before being installed. The option to build these components off-site in quality-controlled factory conditions offers significant benefits in terms of safety, quality and hours saved as well as reducing risk of theft and damage.
The complete unit can be manufactured in the factory either as a prefabricated sectionalised packaged plant room or a tailor-made skid-mounted plant room. Where there is an existing plant room, it may be beneficial to prefabricate the plant room in the factory and deliver it to site in sections. This speeds up the refurbishment and leads to less disruption on site.
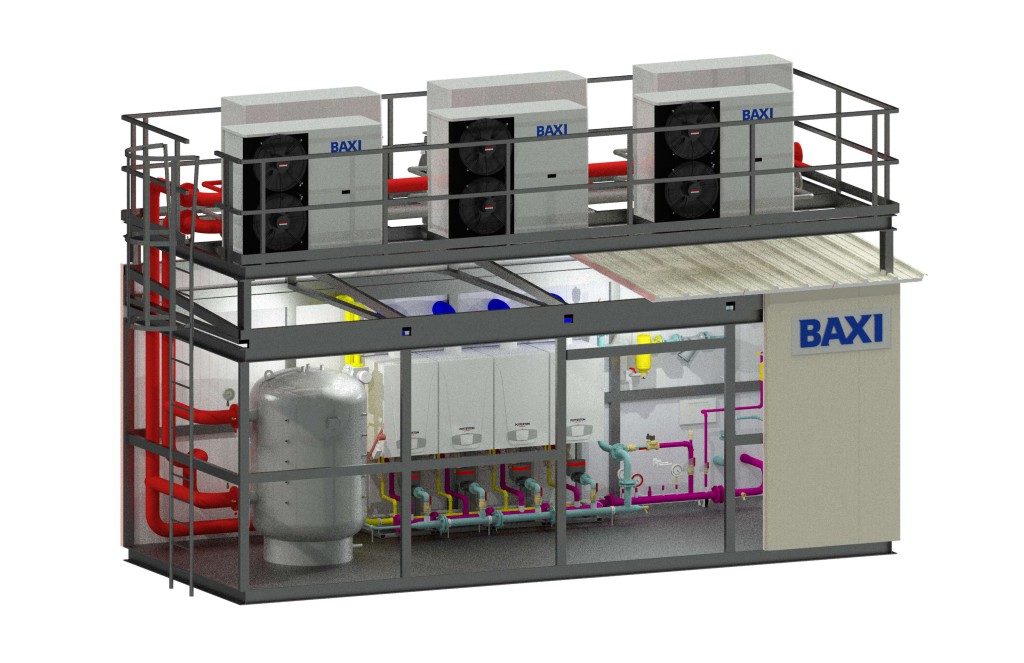
On-site assembly is rapid and, with fewer trades required on-site, planning logistics are greatly simplified. Further, as the process significantly reduces the hot works hours on-site, the installation is safer, bringing health and safety benefits. Quality assurance is also high as the unit is pre-tested before delivery.
Prefabricated utility cupboards
Where a heat network supplies energy to a residential development, installing pre-assembled or prefabricated utility cupboards (PUCs) in each individual property is also becoming commonplace. The cupboards come fitted with a full suite of HVAC and electrical components, including HIUs.
As most of the PUCs installed share many common components and design features, developing standardised designs will enable manufacturers to increase their production to meet the volumes required by the market. However, for standardisation to be achievable, early engagement with the architect is imperative.
A case in point is the PUCs produced by Baxi Packaged Solutions for the 253 residential apartments in the redeveloped Battersea Power Station. By manufacturing the full solution off-site, the risk of human error was reduced significantly and health and safety improved due to the elimination of hot works on-site. It also saved huge amounts of time on the overall project. To put it into context, it takes three hours to connect one unit via these modern methods of construction, whereas an on-site installation can take several days.
Substations
With the anticipated arrival of zoning, many buildings in a heat network zone will need to be connected to the new heat network once it is up and running using a substation.
As with PUCs, the aim should be to standardise substations as much as possible to drive down the cost of heat networks and accelerate connection. However, prefabrication experts can customise them where needed to suit the individual requirements of each project. Examples include designing larger substations to be split into smaller skids for site assembly, overcoming any space constraints, and sizing connections to suit site requirements. Where required, the units can be provided with heat network distribution pumps and headers for rapid changeovers or upgrades.
Key to success
In summary, prefabrication offers many benefits for all stakeholders involved in designing and building heat networks, delivering significant time savings, improved quality assurance and accuracy and a reduced carbon footprint. Encouraging detailed front-end planning, early collaboration and design approval is essential as is a focus on value-added benefit and clear deliverables.
This will truly unlock the potential of the prefabrication process to deliver optimal outcomes, help bring down costs and keep heat network deployment on track.