Delivering cost-effective improvement to chiller design
Fig. 2. A coil utilising micro-channel tubes has better heat transfer than standard coil construction.
ANDREW KEOGH discusses the benefits of different heat-exchanger technology on chiller design.The air-conditioning industry faces a constant challenge to provide higher efficiency and greater equipment reliability. This challenge is even more difficult to meet when the goal is simultaneously to restrict equipment size and limit any potential cost impact. Previous efforts to improve the performance of chillers have concentrated on improving individual components (e.g. higher-efficiency compressors) or increasing the overall heat transfer surface area (e.g. a larger coil) to lower condensing pressure and hence improve performance. However, each of these enhancements tends to increase equipment size, cost — or both. Another solution that is delivering results in air-conditioning applications, both residential and commercial, is micro-channel heat exchanger (MCHX) technology for designing condenser coils. Carrier has incorporated it in the design of its latest large chiller, the Aquaforce. This heat-exchanger technology has been widely used in the automotive industry for many years on millions of vehicles, with substantial success. Compared to traditional coil technology, micro-channel heat exchangers offer considerable benefits, including the following. • Improved heat transfer and thermal performance.
• Increased efficiency of the coil and the overall unit.
• Substantial reduction in refrigerant charge.
• Reduced coil size.
• Minimal impact on equipment cost.
• Enhanced structural robustness.
• Increased reliability as a result of better corrosion resistance.
For years, condenser coils on air-cooled plant have used round copper tubes mechanically bonded to aluminium fins (round tube plate fin or RTPF). Fig. 1 shows a cross-section of a copper tube and several aluminium fins. High thermal efficiency is achieved through direct metallic contact between the tube and fin and the use of fin enhancements to improve heat transfer on the air side of the fins. Standard RTPF condenser coil construction utilises copper tubes in contact with aluminium fins. The use of these two dissimilar materials in harsh environments can result in premature corrosion due to the galvanic couple inherent in this design. In this instance, the aluminium fin is less resistant to corrosion than the copper tube, resulting in galvanic corrosion when the materials are exposed to an electrolyte (created by many environments). The result is attack to the aluminium fin starting at the interface between the aluminium fin and the copper tube. This process creates an unsightly deposit on the surface of the coil and can ultimately lead to the collapse of the fins and failure of the coil. In contrast to standard condenser coils, micro-channel condenser coils are constructed utilising an all-aluminium brazed-fin construction. A micro-channel coil is composed of three key components (Fig. 2). • The flat micro-channel tube. • The fins located between alternating layers of micro-channel tubes, and two refrigerant manifolds. The manifolds, micro-channel tubes, and fins are all aluminium and are joined into a single coil using a nitrogen-charged brazing furnace. Overall product quality and integrity are maximised since only one uniform braze in the furnace is required, compared to the 200 to 300 manually brazed connections on traditional copper/aluminium coils.
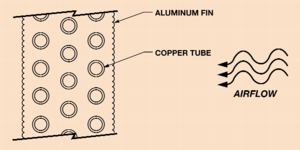
Fig. 1. Standard coil construction comprises copper tubes mechanically bonded to aluminium fins.
The coil is divided into two passes. The first pass is used to achieve de-superheat and condense the discharge gas. The second pass is used to complete condensation and provide liquid sub-cooling. The micro-channel tubes in the heat exchanger have excellent heat-transfer characteristics on the refrigerant side. On the air side, heat transfer is improved by the enhanced surface-area contact and fins designed to optimise heat transfer. The metallurgical fin-to-tube bond reduces thermal resistance between the fin and tube, resulting in better heat conduction. The benefits of the micro-channel heat exchanger may be summarised as follows.
Thermal performance. The performance is significantly better than a standard 3-row coil comprising copper tubes with aluminium fins. The micro-channel concept allows coils to be up to 25% smaller than previously and/or significant efficiency improvements.
Environmentally sound operation. The single-row coil design and the extremely small size of the micro-channels contribute to reducing refrigerant volume by about 30%.
Structural robustness. The construction of the coil inherently leads to a more durable coil that is less likely to be damaged. In addition, the single-row coil design provides a significant weight-reduction opportunity.
Serviceability. Because the fins are supported along both edges, the coil may be cleaned using a high pressure jet washer without risk of damage. Micro-channel heat exchangers can be repaired on site.
Corrosion protection. A micro-channel heat exchanger has superior corrosion resistance when applied in environments suitable for the standard RTPF coil. Most importantly, all these benefits are realised with no overall increase in cost — truly value-for-money engineering.
Andrew Keogh is UK engineering with Carrier Air Conditioning, United Technologies House,Guildford Road, Leatherhead Surrey KT22 9UT.
Related links: