Delivering value engineering
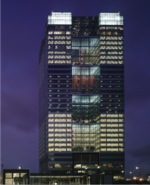
• Do components or equipment offer greater reliability — particularly in business-critical situations, where failure can be potentially disastrous and costly?
• Apart from factory acceptance testing, does the engineering team undertake factory inspection during assembly to check quality assurance and specification compliance?
• Do manufacturers provide an audit trail of all equipment and components used in the manufacture of plant? Preparation and analysis Engineers provide real benefit when a thorough value-engineering exercise is undertaken and regularly reviewed during the design phase. It must be stressed that this process is not a case of simply changing product selection for the cheapest available, or reducing the specification of the product or omitting features that would normally enable the FM provider to deliver a more effective and efficient system in operation. In setting the agenda for a value engineering audit, there are key activities that must be included. Firstly, an appropriate period during the design production phase should be allocated for a full value-engineering audit. Ideally, this should be during outline scheme design and final design, prior to tender. The value-engineering process should include a rationalisation of systems to avoid duplication. Why install expensive double regulating valves across flushing by-pass loops that may never be used again? Checklists should be produced that provide engineers, particularly young engineers, with guidance on what to look for when undertaking a value-engineering study. For example, spot checks on pipe cable and duct sizes must ascertain whether they are oversized or provide a margin for anticipated future changes. Standardisation needs to be considered, particularly when providing brackets and supports for M&E services. Prefabrication must deliver cheaper and quicker fabrication without compromising quality and requires stringent off-site quality control. Simplified arrangements for on-site commissioning and testing can be achieved through precise design details and clearly specifying arrangements for both regulation and flow control. Valuable time and expense can be saved if plant and control systems can be tested off-site and their performance validated in a controlled environment. Teamwork is also essential as part of the value-engineering process. The contractor should be engaged as early as possible and help develop a construction programme which it is happy to work to. The engineer should draw on the contractor’s expertise and experience in suggesting different options and, particularly, better buying procedures that do not necessarily entail changing equipment for that with reduced quality. Early discussions with the contractor also allows the construction standard to be set early and a commitment for zero defects on conclusion to be embraced. The use of resident engineers or M&E clerk of the works can be invaluable too. From inception to practical completion, the application of value engineering in the different phases of the scheme should result in the delivery of a project which satisfies aspirations of the various parties and does not rely on compromising quality, reliability and energy performance to achieve cost savings. Jim Harrison is a director at hurleypalmerflatt.