Humidity as the key to controlling ventilation
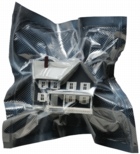
Basing ventilation rates on relative humidity is an effective way of achieving good ventilation that is energy efficient and with low maintenance requirements — explains Colin Hone.
Today’s energy efficient air-tight homes require a ventilation system that can guarantee the best possible indoor air quality (IAQ) at all times.
According to ‘Energy efficient ventilation in dwellings — a guide for specifiers’ published by the Energy Saving Trust: ‘All dwellings need a supply of fresh air, not just for the health and comfort of the occupants, but also to control condensation, remove pollutants, and to ensure the safe and efficient operation of some combustion appliances. The amount of fresh air should match the needs of the dwelling and the people living within it.’
It continues: ’Moisture is probably the most significant element because of the high rates generated by activities such as cooking and bathing, and because of the problems associated with condensation and mould growth. Research has shown that if relative humidity exceeds 70% for prolonged periods, there is a high probability that the condensation occurring on cold surfaces will lead to mould growth. A ventilation rate of between 0.5 and 1.5 air changes per hour for the whole dwelling will usually be sufficient to control condensation.’
Research has shown that occupants are most comfortable at a relative humidity of 40 to 50%. The human respiratory process produces CO2 and water vapour which, unless extracted and replaced with fresh air, will linger indoors — with detrimental effects on inhabitants’ health and on the fabric of the building itself. Demand-controlled ventilation automatically adapts to the requirements of occupancy. If there are more people in a room then its sensors will adapt to the zonal use and increase the ventilation. DCV also helps to eliminate airborne pollutants such as carbon dioxide, carbon monoxide, oxides of nitrogen, tobacco smoke, allergens and other bio-contaminants.
The recent trend in the UK has been veering in the direction of adopting mechanical heat-recovery ventilation (MHRV), despite fears that use of these systems may actually increase the risk of health and respiratory problems in tenants and householders if not installed and maintained properly.
The logical, and already proven, alternative is to adopt DCV systems that include humidity sensors on the grilles that automatically react to occupancy — so if the adults have gone to work and the kids are at school the system operates on minimum, producing a trickle of air. When the house is occupied the humidity-sensitive grilles sense that and gradually increase the levels of ventilation. There are no filters to change, they are whisper quiet in operation, and the system is virtually maintenance free.
Serious concern has been expressed that tenants and homeowners might be tempted to cut corners with MHRV systems and isolate fans to save money and to cut down on noise levels. One of the big downsides with MHRV ventilation systems is that the filters must be changed at least annually. There are fears tenants and homeowners will not invest the time and money to fit new filters. If there is no ventilation in wet rooms and no clean air circulating around these new airtight dwellings, these factors may well present problems that will need to be solved sometime in the future.
Another concern with MHRV is that tenants and homeowners worried about the fans being switched on all the time may be tempted to isolate them to save money or to cut down on noise levels. Social-housing tenants are likely to worry about energy costs, so there is more risk of this happening in this sector.
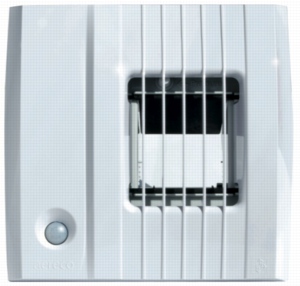
Humidity-sensitive DCV is proven to have much lower energy usage than MHRV systems, whilst providing greater levels of comfort in living areas and eliminating the problems of mould and condensation in wet rooms. A 2008 study by the Fraunhofer Institut Bauphysik in Germany shows that DCV is a far more cost effective and reliable method of providing the optimum indoor environment. The study, (reference IBP-Bericht RKB-12-2008), comes down heavily in favour of DCV.
In exhaustive tests, the Institut found that a humidity-sensitive DCV system offers an excellent method of staying below 1200 ppm CO2, which guarantees optimal indoor air quality.
In France, where DCV is major player in new build, another test bed, the Performance project, allowed testing in-situ of mechanical ventilation systems from two manufacturers, including Aereco. The Performance project monitored demand controlled MEV on two large apartment blocks. The project, supported by French ADEME, concentrated on two very airtight buildings erected in 2007 (one in Paris and one in Lyon) and the efficiency of humidity controlled MEV in general and the Aereco DCV system in particular.
A total of 30 occupied dwellings were monitored over two years from November 2007 to measure representative parameters for energy consumption and IAQ. Measurements of CO2 concentrations show indoor air quality is ensured in a low-occupied bedroom with one adult present as well as for one with high occupancy (four adults). The peak of CO2 concentration shifts from 700 ppm in the low occupancy bedroom, to 950 ppm in the latter, but even there the 1200 ppm level was not exceeded for more than just a few hours in the heating season.
Importantly, the project illustrates the high performance of DCV systems in providing high levels of indoor air quality.
Summing up, the potential for DCV is high and will become higher as the density of occupancy is lowering on a global trend for years in all countries.
Colin Hone is sales director of Aereco.