Reaping the benefits of commissioning modules
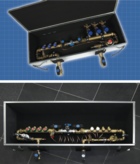
Using commissioning modules in hydronic systems delivers benefits above and beyond the commissioning process itself. Stefan Jensen of SAV Systems explains.
A recent BSRIA study on fan-coil systems using commissioning modules showed significant time-savings on installation (28%), flushing horizontal mains pipework (43%), flushing fan-coil-unit circuits (23%) and commissioning (44%) — compared to traditional systems with commissioning valves on individual terminal units. Other benefits include greater flexibility, improved cost control, fewer operatives onsite and a better solution for the end client.
Commissioning modules are also proving invaluable in the commissioning of variable-volume systems with very low flow rates (<0.015 l/s), which can be a major benefit in complying with CIBSE Code W - as explained below.
However, to achieve the maximum benefits afforded by commissioning modules it is important to ensure they are designed and deployed correctly. This article explains how specifiers can ensure they exploit the full potential of these modules.
A commissioning module essentially acts as a distribution hub for a group of terminal units (typically up to seven) and enables commissioning to be carried out at the module. Each module incorporates all the valves required for commissioning, including 2-port actuated control valves and a differential-pressure control valve to ensure that all 2-port control valves operate with excellent authority. They are suitable for fan coils, chilled beams, radiant heating, trench heating and air-handling units.
In most cases, commissioning modules are made offsite under factory conditions and pre-tested before delivery to site. The amount of onsite work is thus reduced, accelerating the installation phase of the project. This also means the time of skilled operatives can be used to maximum effect, with a consequent reduction in costs. In addition, there are fewer delays caused by various trades waiting for one another to finish working in a particular area.
Further, as the modules are assembled under factory conditions, as opposed to demanding site conditions, there is minimal risk of faulty connections. Opting for pre-fabrication also provides cost certainty because the project will be less liable to fluctuations in material costs through the course of the project.
Another benefit is that the commissioning module can be supplied in an insulated box with vapour-sealed penetrations so that commissioning does not compromise the thermal insulation of the system. In contrast, where individual valves are connected directly to a terminal unit and insulated before commissioning, the commissioning engineer has to disturb the insulation to commission the system. And there is a risk the insulation will not be replaced properly, resulting in wasted energy.
Increasingly, commissioning modules are connected to terminal units using composite plastic/aluminium pipe and pressfit connections, instead of copper pipe. Highly flexible, composite pipe reduces the number of connections — thereby saving time and reducing the risk of leaks from faulty connections. Flexible pipe also makes it easier to relocate terminal units should the design change during the shell-and-core phase, during fit-out or in later refurbishments.
Where required, the composite pipe can be pre-insulated before delivery to site, saving even more time.
Smarter commissioning
All of the control valves for a group of terminal units being in one location also brings major benefits to the commissioning process. For example, rather than taking measurements at each terminal unit, generally working at height and perhaps having to remove ceiling tiles, all the measurements for that group of terminal units can be taken at the commissioning module. Not only does this make commissioning simpler, it also saves time and can make all the difference to the project being handed over on schedule.
From the end client’s point of view, commissioning modules make it easier to re-commission the system at a future date if the building layout or usage changes.
Commissioning modules also enable use of the subtraction method of measuring flow rates, one of the methods recommended in the latest CIBSE Code W and BSRIA Commissioning Guide for dealing with ultra-low flows (<0.015 l/s). Ultra-low flows are a common problem in variable-volume hydronic heating systems, where the flow through a single terminal unit may be too low to measure accurately with standard flow-measurement devices.
The subtraction method, which can be used with all flow rates, measures the flow through all the terminal units connected to the commissioning module to obtain a combined flow rate. Then, when one terminal unit is isolated, the flow rate through the remaining terminal units is still high enough to measure, and the difference is equivalent to the flow rate of the unit that was isolated.
Planning ahead
Early planning is an important aspect of a project using commissioning modules, so that module locations are optimised for the terminal units they are serving. It also makes sense to involve the supplier of the commissioning modules at an early stage as their specialist knowledge will help to spot potential problems at design stage and nip them in the bud before work starts on site.
When all of these factors are taken into account, specifiers and installers can be assured of a successful project from which all parties benefit.
The benefits of commissioning modules
• 28% reduction in installation time
• 43% reduction in flushing horizontal mains pipework
• 23% reduction in flushing fan-coil-unit circuits
• 44% reduction in commissioning time
• More effective use of skilled operatives
• More precise measurement of ultra-low flows
• Benefits of pre-fabrication
• Uncompromised insulation
• Facilitates use of flexible pipework
• More flexible solution for
• 28% reduction in installation time
• 43% reduction in flushing horizontal mains pipework
• 23% reduction in flushing fan-coil-unit circuits
• 44% reduction in commissioning time
• More effective use of skilled operatives
• More precise measurement of ultra-low flows
• Benefits of pre-fabrication
• Uncompromised insulation
• Facilitates use of flexible pipework
• More flexible solution for end client
Stefan Jensen is product manager with SAV Systems.