Taking note of water content
Despite the popularity of low-water-content boilers, there are many instances where selecting boilers with a higher water content will significantly improve system performance. Simon Mitchell of Hoval explains the engineering reasons, which will be reflected in the next version of ‘CIBSE Guide B1: Heating’, due in March 2013.
It is a given that the performance characteristics of a boiler will have a significant impact on the efficiency of heating and domestic hot water (DHW) systems. It is also clear that building-services engineers are under constant pressure to improve energy efficiency by optimising the performance of systems. So it is very important to be aware of all of the factors that can impact on performance — in either positive or negative ways.
This principle can be illustrated by considering the influence that the water content of boilers has on the rest of the system. In recent years low-water-content boilers have become the preferred option for many specifiers, but there are instances where boilers with a higher water content will deliver significantly higher efficiency. This is because they avoid many of the constraints imposed by low-water-content boilers. Indeed, it is anticipated that this will be reflected in the next version of ‘CIBSE Guide B1: Heating’, due for publication in March 2013.
Consider a heating system comprising three identical boilers, such as might be found in a typical office block, providing hot water for space heating and DHW. For the purposes of this illustration we can assume that DHW requirements are relatively low and that the space heating is provided by a fan-coil system in office spaces and underfloor heating in an atrium.
The DHW will require a constant flow temperature of 80°C, while the other temperatures of the other two systems may vary considerably during the course of each day.
One of the constraints imposed by low-water-content boilers is that they require a minimum flow rate, often equal to the design flow rate. Also, the boiler sequencing control will be geared to maintain a constant temperature after the three flows have mixed.
However, once design space temperatures have been met the heating systems will not require a full flow. With low-water-content boilers this means a lot of flow water at high temperature will be diverted via a low-loss header back to the boilers’ return to maintain a constant flow through the boiler circuit.
The effect of this is to raise the temperature of the water returning from the fan-coil and underfloor heating circuits. Thus, there is less condensing — if any. The result is that the system fails to deliver maximum efficiency as a direct result of the constraints imposed by low-water-content boilers.
Another important consideration is that low-water-content boilers use smaller heat exchangers than those with higher water content, so the waterways are more restricted. This increases the pressure drop so that, typically, a primary circulating pump will be required to supplement the heating-system circulators. Narrower waterways are also more vulnerable to blockage.
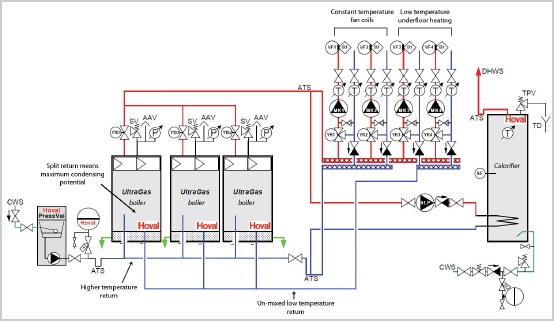
On the plus side, less condensing and lower energy efficiency does mean that less acidic condensate is produced so that a boiler made using lower quality materials may last longer. However, that’s probably not going to compensate the building operator for higher energy bills.
High-water-content boilers can accommodate a variable flow, so there is no requirement to divert flow water directly to the return circuit via a low loss header. As a result, the system is better able to take advantage of low return temperatures from the heating systems to achieve condensing. Indeed, some high-water-content boilers increase the potential for condensing by having the facility of a split return.
In the case of the system described above, the split return would work by having separate returns for the fan coil and underfloor heating systems (see diagram). This is because in such a system there will almost certainly be occasions when the return temperature from the fan-coil system is considerably higher than that from the underfloor heating system. With a single return the two flows will mix, and the temperature of the return from the underfloor heating will be raised accordingly, reducing the amount of condensing. With a split return the return water from the underfloor heating circuit can remain separate to maximise the condensing potential. In our experience using a split return can increase efficiency by as much as 9%.
The adequately sized heat exchangers used in high-water-content boilers mean that there is no need for high turbulence and pressure drops to achieve effective heat transfer. As a result the system circulators can manage the flows without an additional pump, helping to reduce both capital costs and energy consumption
These are all good reasons for giving due consideration to water content when specifying boilers. That’s not to say that boilers with higher water content will be the ideal choice for every project — but neither will low-water-content boilers. The important thing is that all of the options are considered during the design and specification process.
Simon Mitchell is specification sales manager with Hoval.