To refurbish or replace?
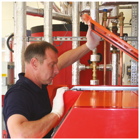
When boilers are no longer meeting performance or efficiency requirements, building owners have the choice to refurbish or replace. Kevin Stones of Hoval highlights the key considerations
Despite the variety of heat sources that are now available for providing space heating and domestic hot water, boilers continue to be the dominant heat source and look set to remain so for quite some time. In commercial and industrial applications, the boilers represent a significant investment, so it makes sense to ensure they are maintained properly to extend their life and optimise their performance.
Nevertheless, there comes a time with all boilers when something has to be done, beyond routine service and maintenance, to upgrade performance. This may be because one or more of the boilers have failed completely, or perhaps frequent breakdowns are interfering with the building’s operations, combined with rising costs for spares.
In recent years there has also been greater emphasis on energy efficiency, and energy audits may highlight ageing boilers as a source of inefficiency that needs to be remedied.
Clearly a complete failure is best avoided, and regular servicing will help to ensure that any problems are identified in time to take remedial action before total breakdown. Ideally, regular visits by maintenance technicians who are familiar with that make of boiler will also ensure the building operator is aware of the general condition of the boilers so that any future work can be budgeted in advance.
This will also be useful information when the time comes to either refurbish or replace. Understanding the current condition is the first stage in determining whether refurbishment is a viable option, what would be involved, what efficiency improvement might be achieved and how much extra life could be anticipated following refurbishment.
This would then need to be balanced against the capital cost of new boilers and the projected efficiency improvements — over what might be achieved by refurbishing the boilers and, possibly, burners. This will then help determine whether it is worth spending money on an overhaul, compared to investing in a new boiler that will inevitably be more efficient and reliable.
For boilers operating at temperatures above 105°C, which require annual inspection under the Pressure Equipment Directive, there should already be a good understanding of the boiler’s condition. However, boilers operating below this temperature may not have undergone such thorough scrutiny, and a ‘health check’ will be needed to establish their condition.
In this respect, it will be useful to ascertain the thickness of the metal, checking for corrosion and other deterioration — along with non-destructive testing to check key welds in the boiler shell. The boilers may also need descaling, so, if they haven’t already been inspected, this should be assessed. Some boilers have easy access through a suitable manhole, but this can be challenging with other designs.

If the decision is to refurbish the boiler this may also be an opportunity to upgrade the burners though, again, it will be necessary to assess the cost-effectiveness of doing this. Replacing older burners with modulating burners will give better control and a more efficient response to varying heat loads. There may also be advantages to introducing oxygen trim to ensure optimum combustion and minimum emissions under all loads.
The existing boiler controls should also be analysed to ensure they are aligned to the current requirements of the building. There are many occasions where a building’s usage changes considerably over the years, but the controls aren’t re-commissioned to reflect this. If re-commissioning isn’t possible it may be advisable to install new controls as part of the refurbishment.
Nevertheless, many such evaluation exercises will determine that replacement is the best option. The building-services engineer will then need to work with the boiler manufacturer and other parties to ensure the project goes smoothly — with minimum, if any, downtime while work progresses.
For example, close liaison with the manufacturer can help to ensure that — as far as possible — all the connections line up. This can avoid the need to drain the pipework, though it’s important to check the existing valves will hold and take appropriate action if they won’t. The flueing should also be assessed, especially if several boilers are connected to one flue but only one or some of them are being replaced — capping off as necessary.
Ultimately the ‘right’ decision will be different for each project and will be determined by a number of engineering and non-engineering factors. The building services engineer will play a key role in guiding the end client towards the best solution.
Kevin Stones is engineering and service director with Hoval Ltd.