A great refurbishment for Great Northern Hotel
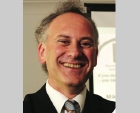
The refurbishment of the listed Great Northern Hotel at King’s Cross achieved an Energy Performance Certificated only just below a B rating. Mike Malina of Energy Solutions Associates, which carried out the assessment, describes how a BREEAM ‘Very good’ certification was achieved for this 150-year-old hotel.
Take a building project — A Grade 2 listed, 6-storey curved structure first opened in 1854 at the height of the British Empire. Neglected and mothballed in recent times and situated at the southern end of a massive 67 acre regeneration site. This was the Great Northern Hotel, London's first purpose-built railway hotel — a Victorian refurbishment challenge located between King’s Cross station and St Pancras International.
The mission was to restore the building as a fully functional hotel of 94 bedrooms fit for the 21st century, keeping the external appearance and many of the original features, so protecting the unique historical and architectural nature of the building. The additional challenge was to fit all the new mechanical and electrical services in a building of this age, with some tight spaces and with a number of unknown structural elements not obvious or recorded — lost in the mists of time. All of this to comply with the Building Regulations and the sustainability policies, as part of the conditions of planning permission granted by the London borough of Camden.
Because of the listed-building status and the need to preserve the appearance of the building, an overview energy assessment of the whole development area did not identify the Great Northern Hotel as an appropriate location for the incorporation of renewable energy technology.
However a detailed review of lower-carbon and renewable technologies had been carried out at the planning stage. This review had concluded that a gas-fired combined-heat-and-power system (CHP) would function as the most appropriate technology given the significant constant hot-water demand of the hotel.
The electricity produced by the CHP is fed into the building systems, and meets about 16% of the building's total electrical demand.
![]() |
Now restored to hotel use — London's first purpose-built railway hotel, the Grade 2 listed Great Northern Hotel at King’s Cross. |
The warm CHP exhaust is also used in conjunction with a variable-refrigerant-flow (VRF) system and air-source heat-pump technology to effectively provide the building's heating demand and assist in pre-heating of hot water.
Significant ventilation plant incorporates plate heat exchangers, and the main fresh-air supply, and extracts incorporate a run-around coil to maximise energy efficiency. This integrated CHP/VRF system, in addition to all the energy-efficiency measures, are expected to lead to an overall CO2 emissions reduction of about 9.5%.
Main contractor Mace appointed Dornan Engineering Services to carry out the design and installation of the mechanical and electrical services for the project.
The project manager for Dornan, Ronan Keohane, explains, ‘The challenge of working in a building constructed over 150 years ago was the unknown, which would only be revealed during the refurbishment work.’ The space in some areas was also very restricted.
This had an impact on the run of services throughout the building, which was largely confined to the main runs along the spine of the building via the corridors. Dornan undertook extensive 3D modelling to get an exact layout and fit for the M&E services for the entire building. It could be said that this was an enhanced design process on the lines of what will become a lot more common in the future with the delivery of BIM (building information modelling). This process enabled a very successful fit out of the M&E services, in some very tight spaces within the three basement plant rooms.
David Shaw, business manager of Baxi-SenerTec , the CHP manufacturer and supplier, commented, ‘This was one of the best jobs I’ve experienced in many years and a real credit to Dornan, who had taken the real time and effort to pre- plan and fully understand all aspects of the project. This ensured a trouble-free installation and commissioning process.’
![]() |
The refurbishing Great Northern Hotel at King’s Cross Station fell just short of achieving a B rated Energy Performance Certificate. |
In the end, after an energy assessment of the building to obtain the Energy Performance Certificate (EPC), Energy Solutions Associates, energy assessor, Brian Edwards explained, ‘The EPC missed getting a B rating by just three points. This was a well-run and well documented contract, and this ensured that extensive and accurate information had been provided, ensuring that an accurate and meaningful EPC could be produced.’
From an M&E perspective, this project was a good example of the refurbishment of an inner-city historic building. The limitation of achieving a better EPC rating was a clear case of the restrictions of the listed-building status. Limits on fitting double glazing, with secondary glazing only permitted along with other elements for enhancing the insulation of the building fabric, prevented the B rating.
Mike Malina is a director of Energy Solutions Associates and the author of ‘Delivering sustainable buildings’ published by Wiley- Blackwell. Readers of MBS can get a 20% discount using this code VBB09 at www.goo.gl/yt39F
Environmental sustainability — key points of compliance
The integration of the principles of sustainable design into the refurbishment of the Great Northern Hotel, which meant balancing sustainability measures with the Grade 2-listed status of the building and the need to preserve the building structure and fabric as far as possible in its historic form.
• A target to achieve, at least, BREEAM ‘Very good’ certification.
• Reuse and upgrade of the existing building with associated embodied energy and material savings.
• Improve the building fabric (where possible for a listed building) U-values, by insulation and fitting secondary glazing.
• To provide for the efficient use and monitoring of systems via a building energy management system.
• Use low-carbon electricity and thermal energy supply using VRF air-source heat-pump system and gas-fired combined heat and power.
• Maximise use of natural daylight and zoned, daylight controlled, low energy lighting.
• Specify water-saving devices and sanitary ware to reduce water consumption.
• Installation of grey water recycling system to further reduce water usage.
• Construction waste minimised and recycled where feasible.
• Provision of recycling facilities for construction and operational waste.