The realities of BIM
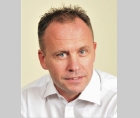
Realising the benefits of building information modelling (BIM) requires not just BIM itself but also a spirit of collaboration and co-operation — as well as suitably detailed BIM libraries of products. Stuart Turner of Hamworthy Heating shares his views and experiences.
The use of building information modelling (BIM) for the different elements of a building project will vary greatly. For mechanical and electrical equipment such as boilers and water heaters, identifying the space available and the embedded output/performance data will be vital. However, the aesthetics of a boiler are not as important as how the interior or exterior of a building will look.
A key theme that emerges when exploring BIM is the idea of ‘collaborative working to improve information flow and performance during the design and operation of a building’. But are there too many commercial influences and pressures in the supply chain to make this altruistic view a reality?
At a recent Hamworthy event on BIM with industry professionals from all sectors (architects, building-services engineers, consultants, contractors and building operators) the point was raised that it isn’t about collaboration but co-operation of organisations at different stages of a project using BIM. The Government, which has become a key driver behind BIM, wants to ensure value is achieved in the operational lifecycle of an asset, as well as during the design and construction phase, through the use of the Soft Landings framework and BIM.
However, BIM is not the only way to achieve value on a project, and to gain the 20% cost reduction outlined in the UK Construction Strategy we need to get things right a stage before BIM, address the upfront process issues and avoid re-work at a later stage. At Hamworthy we commit a significant amount of time at the start of a project to ensure the customer understands all the heating and hot-water options and can make the best choice through being well informed. It is also important to define a customer’s objectives, what outcome they are seeking and identify the building usage from the outset of a project.
It has been reported in the press that firms are making multi-million pound investments in the technology to deploy BIM. Add to this the investment needed in people and processes to support the technology, and the industry needs to be sure a return on investment can be achieved.
The competitive nature of the market place cannot be ignored. Although the ideology of all parts of the building supply chain, from architecture to building operator, working together sounds great, I’m not sure we’ll ever be able to get there in practice. There are issues surrounding compatibility of software, ownership of building models and liability on site. Finally, is there even the willingness to collaborate?
Some BIM components are already available from manufacturers or generic BIM libraries, but the products need to be designed into systems — hydraulic, electrical, flue and fuel. The components for joining systems are not so readily available.
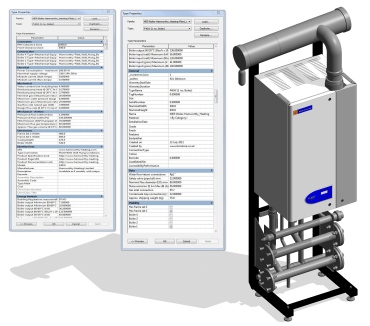
Flue systems are an important aspect of a heating or hot-water system, and the flue design and installation companies will be wondering how they protect the intellectual property of their design. They have developed bespoke flue-system calculation capability and may be nervous about sharing their knowledge and experience. And yet one of the key benefits of modelling is to identify areas of conflict in the design (clash detection) and solve the problem whilst still ‘on paper’. So avoiding the flue run having to go through a structural beam is something everyone can associate with as a real benefit.
Whilst BIM is a complex subject, it can be viewed as a more straightforward proposition for new buildings. However, it is important not to forget that most boiler work is associated with refurbishment projects for existing buildings.
Technology is available to scan buildings and create a model retrospectively, but this will be very costly and may not be a worthwhile investment for the thousands of buildings that will need refurbishment in the coming years. The Government has said BIM will only be mandatory on capital projects over £5 million, so is the industry adopting a similar approach and only using BIM on major new projects, if at all.
There is no doubt that BIM has its place for certain projects. The benefits of good planning, defining what is required of a building prior to starting work, improved workflow, avoiding costly rework, saving time on site and improving value over the lifetime of an asset are vast. However, BIM is not the solution; it is only an enabler, and to really make a change needs a shift in culture and ways of working for the true benefits of BIM to be realised.
Hamworthy’s parametric BIM components, for example, have a large amount of embedded data, and each range of boilers is encompassed in one configurable model to make it easier to select options and change the output of a boiler without having to load a new component into the model. Designed to the strictest standards, they are loaded with extensive metadata to the COBie UK 2012 requirements. We are continually expanding our BIM library and will shortly be adding BIM components for the Purewell VariHeat range of condensing boilers. Visit the link below to download the components.
Stuart Turner is southern regional sales manager with Hamworthy Heating.