Heat rejection put to good use
The heat rejected from an air-conditioning system has the potential to be put to good use. Mike Nankivell of Space Airconditioning describes how just that was achieved when a chiller serving a London hotel was replaced.
In building HVAC system terms, heat recovery is a process of capturing, and putting to good use, heat that would, in the normal course of events be ‘thrown away’. One example is heat energy that is absorbed and rejected by an air-conditioning system during its cooling cycle. This, to all intents and purposes, is free heat that can be successfully redirected for space heating, domestic water heating or any other process that requires heat.
Heat recovery is being successfully applied in all types of buildings, including hotels, schools, manufacturing plants and office buildings. It typically provides a very attractive return on investment for building owner/operators.
The use of heat recovery should be considered in any building with simultaneous heating and cooling requirements, or where the heat can be stored for future use.
Buildings such as hotels with high year-round internal cooling loads combined with high hot-water demand are excellent opportunities for heat-pump, heat-recovery chiller technology. Importantly, heat-pump heat-recovery systems can allow for substantially downsizing or even elimination of fossil fuel, combustion-based heating equipment such as gas boilers. This was the case in a recent project undertaken by the Daikin distributor Space Airconditioning.
This recently completed refurbishment project in the heart of London, includes a 320 kW Daikin chiller with a heat-recovery option. In addition to satisfying the hotel’s cooling demand, this chiller also provides warmed water to four 500 l indirect DHW cylinders.
The hotel’s hot-water supply is pre-heated by the heat-recovery process, which dramatically reduces the output required of new high-efficiency gas-fired water boilers. The result is significant energy savings and huge reductions in gas consumption.
The hotel group had committed to refurbish the Covent Garden Hotel, including all guest bedrooms as well as function rooms, reception areas and restaurants.
A survey was carried out by Space Air technicians and the hotel’s maintenance company. It was determined that whilst the existing AHU plant serving the common areas and restaurants etc. was in good condition and could be re used, an existing air-cooled chiller needed replacing; it was designed to operate with R22 and was in a state of disrepair, with only one working compressor circuit.
The thought that a replacement Daikin chiller could also provide cost-effective heat recovery created interest because the existing gas boilers were due to be replaced. In addition two 1000 l calorifiers needed removing.
Space Air presented the features and specification of the Daikin heat-recovery system to the client and was able to illustrate cost savings the heat-recovery option would provide. In addition the new boilers would be smaller, further reducing costs. The hotel group decided it made good financial sense to proceed with the heat-recovery option.
The Daikin heat-recovery chiller operates 24/7, and an existing back-up cooling-only Daikin chiller is only used in case of unlikely failure. This means the new chiller provides virtually continuous pre-heated water for DHWS.
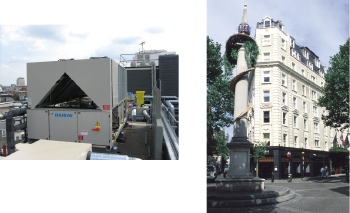
On a seasonal basis it has been calculated that the chiller will produce an average of 236.6 kW of hot water, free of charge. This takes into account the chiller operating for 24 hours, 7 days a week, 365 days a year (8760 hours).
Four 500 l indirect cylinders provide pre-heated water on a separate circuit to the secondary heat exchanger in the basement, which serves the main feed to the showers, and DHWS for the hotel guestrooms.
Allowing for losses in the cylinders and pipework etc. Assuming high demand, the system achieves an approximate ∆t of 20 K. So the mains water supply to the DHWS heat exchanger is increased by this temperature — leading to much lower boiler demand.
To put this into perspective we calculated what it would cost to heat 2000 l of water based on a ∆T of 20 K with a gas boiler and compared this with the ‘extra’ cost of providing a heat-recovery option on the chiller to perform the same function.
The average power consumption is about 46 kW for 8760 h a year. With gas at 4 p/kWh, the annual cost would be about £16 000.
The estimated installed premium cost for the optional heat-recovery circuit on the Daikin chiller plus the required tanks, pumps, pipework was in the region of £30 000 to £40 000.
These figures give a payback on the investment of less than three years.
So far the client is delighted with the cost savings achieved and is looking to apply similar heat-recovery principles in more of its property portfolio.
Mike Nankivell is a director of Space Airconditioning.