In pursuit of airtightness
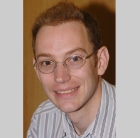
Reducing air leakage from buildings improves energy efficiency — in theory and in practice. David Bleicher of BSRIA looks at how construction professionals can pass their airtightness test first time.
Building Regulations, planning requirements and environmental assessments such as BREEAM are pushing buildings towards ever-lower energy use. One of the steps that can be taken to improve energy efficiency, both in prediction models and in real life, is reducing air leakage. Although the worst allowable air permeability stated in Building Regulations guidance has remained unchanged for some years at 10 m3/h.m2 at 50 Pa, many designers are finding that much lower levels are achievable.
The good-practice benchmark for new air-conditioned office buildings is 2 m3/h.m2 at 50Pa. If sufficient attention isn’t paid during the design and construction stages of a project, there is a risk that the building will fail its airtightness test. Carrying out remediation work and retests when this happens can be a major headache, leading to delays and cost over-runs.
Airtightness is not rocket science. While many things contribute to a building achieving its airtightness target, by far the biggest factor is the quality of site workmanship. As such, an airtightness test is in some way a measure of how well the building has been designed and built from a technical point of view.
The key principles of achieving airtightness are the following.
• Having a simple strategy defined at design stage.
• Clearly indicating the location of the air line on the drawings from an early stage (the air line is defined as the series of elements providing an airtight envelope around the building).
• Using components that are specified as airtight, such as windows, doors, rooflights and smoke vents.
• Generating common, easily repeatable details.
• Ensuring the building is prepared correctly.
• Assigning a single individual or team with overall responsibility for airtightness.
• Communicating the importance or airtightness throughout the entire project team.
• Involving all parties in the process, including trades that interface with one another.
• Making it clear who is responsible for sealing in each instance.
Air leakage commonly occurs at interfaces between construction elements, such as wall-to-roof junctions and service penetrations. Also, air leakage paths may be circuitous, meaning air may travel some distance through the building fabric between the points of entry and exit.
There is a wealth of advice in a new guide from BSRIA (about which more below). Common construction types for walls, roofs and penetrations are covered in the guide, including the following.
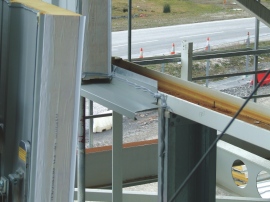
• Traditional brick & block cavity walls.
• Composite cladding panels.
• Curtain walling.
• Structural insulated panels (SIPs).
• Single-ply membrane roofs.
• Mansard roofs.
• Upstands.
For each type of construction, best practice is stated alongside common pitfalls.
One of the pitfalls common to many construction types is including parapets, balconies and the like in the air line. This over-complicates details and increases the number of joints between elements. Penetrations, such as ductwork through a concrete riser wall, can be locations of air leakage. The best seal is achieved when the build sequence allows the penetration to be sealed to the air line element. All too often, access is restricted by later work. Avoiding such situations requires advance planning of all penetrations. The publication covers methods of sealing penetrations on site, in addition to pre-fabricated components such as rubber seals and pipe grommets.
The photograph shows the installation of composite wall panels in a new building. A line of mastic is already in place, and there is an effective overlap between air line elements, leading to an effective seal.
‘Designing and constructing for airtightness’, the new BSRIA guide, provides architects, main contractors and subcontractors with knowledge of best practice which will help them achieve their airtightness targets. Aimed primarily at commercial buildings, it gives examples of good and bad practice gathered by BSRIA’s airtightness consultants over many years of testing.
The guide is packed with images that show good practice and also common pitfalls that lead to air leakage. Sample clauses for airtightness testing are provided for insertion into contracts. The publication also gives guidance on methods of carrying out the test, including zone and sample testing. The various test standards are outlined, together with means of identifying air-leakage locations, such as thermography and smoke testing. There is also a summary of the Building Regulations requirements and supporting guidance for testing across the UK and Republic of Ireland.
The guide is now available for purchase from BSRIA.
David Bleicher is publications and training manager at BSRIA.