Presenting the benefits of grooved joints

Less labour, less risk, less cost — how much more could you ask of a system for jointing pipes, asks Paul Burke of Tyco.
Combining material prices and volatile labour costs, the installation of mechanical piping components can represent a significant cost risk on complex commercial and industrial building projects. Furthermore, contractors must consider the factors that minimise future maintenance and servicing for the building operator.
Pressure to reduce the cost impact of the mechanical piping phase of the project has led engineers and contractors to identify opportunities to minimise installation times, with further benefit of a subsequent reduction in labour costs.
Added to this drive for efficiency is the increased focus on system reliability as developers and owners factor the total operational cost of the building once the initial construction and fit-out phases are complete.
One of the most beneficial alternatives to welded piping systems in today’s market is grooved piping components. A grooved mechanical joint is formed with grooved-end pipes, fittings or valves, and a coupling. The coupling comprises of three elements in order to make a complete joint — housing, gasket, and nuts and bolts.
Grooved mechanical piping uses standard pipes with a fabricated groove which is machined or cold-formed into the pipe end. The joint is sealed using a resilient rubber gasket around the two grooved pipe ends and is pressure responsive to accommodate degrees of expansion, contraction and movement within the pipeline. The coupling housing fully encloses the gasket and grips the pipe groove to create a leak-tight seal in a self-restrained pipe joint. This is held together by the external nuts and bolts that connect the upper and lower housing segments.
Grooved mechanical systems use either rigid or flexible couplings depending on the application.
Rigid couplings grip the full circumference of the pipe grooves to create a rigid joint. When using rigid couplings the piping is not subjected to axial movement or angular deflection during operation.
Flexible couplings allow controlled linear and angular movement caused by thermal changes in the pipeline. This is particularly useful at locations in the piping system where there is a change of direction, helping to minimise stress on the pipework.
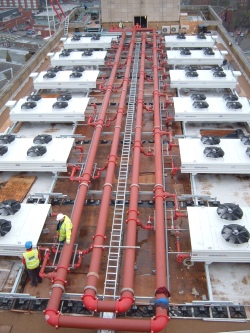
Grinnell Products has carried out an analysis of installed labour cost analysis comparing its mechanical grooved systems with conventional welded pipe jointing for a recent hotel project in the UK. The data analysed the potential material cost and labour savings of grooved products used in both heat-recovery pump sets and horizontal in-line pump sets for HVAC applications.
Based on specific installation parameters, the cost analysis used labour times for grooving and welding from the Luckins mechanical database. The results of the installed labour-cost analysis provide compelling evidence for the use of grooved products over traditional pipe jointing methods.
• In heat-recovery pump -set applications the total labour hours are reduced from 123 h to 11.75 h using grooved mechanical systems. This represents a 90% saving in labour cost.
• For horizontal in-line pump sets the savings are even greater. Switching from traditional welded pipe jointing to grooved pipe jointing reduces the total project cost in materials and labour by 92%.
The above results demonstrate that considerable labour cost savings can be made by using grooved pipe jointing techniques. When it comes to optimising cost efficiencies on the most volatile elements of a project, grooved mechanical systems represent a significant reduction in labour hours and subsequent cost.
Paul Burke is sales director for mechanical products, EMEA, with Tyco.