Cascading control
Cascade heating systems comprising multiple boilers are ideal for adapting to changing heat loads and also supporting a biomass boiler without adversely affecting RHI payments — but only when they are controlled effectively. Kevin Stones of Hoval explains.
When it comes to reducing energy consumption and carbon emissions for end users, specifying energy-efficient plant is only part of the solution. Controlling the inherent efficiency of that plant effectively is equally important if maximum benefits are to be achieved. This area requires considerably more attention and potentially better communication between controls companies and equipment manufacturers.
Heating is a very good example, particularly as the thermal performance of the buildings themselves continues to improve. With lower heat losses through the building fabric, set-point temperatures are achieved more quickly and then the heating plant needs to maintain those temperatures with minimum energy consumption. This requires heating systems that are able to adapt to changing heat loads more efficiently.
In what might be described as a ‘conventional’ arrangement of gas-fired condensing boilers this situation is effectively addressed by using a modular cascade of boilers, each with the ability to modulate. For instance, several boilers in a cascade each capable of a 5:1 turndown ratio creates a very adaptable and responsive system.
A further benefit of cascade boiler systems is that they can be supplied as a kit complete with wall-hung boilers, low temperature hot water (LTHW) and gas pipework header(s), inter-connecting flexible LTHW and gas pipework, pumps and valves. As well as facilitating installation this means they require less plant room space, which potentially makes it easier to incorporate other heat sources in the cascade.
However, if the cascade isn’t controlled effectively those benefits will not be fully realised. Crucially, the control strategy should ensure that the design temperature differential (ΔT) between flow and return water temperatures is maintained. All too often, the controls reduce the ΔT from, say, 11 K to just a few degrees. The result is that the boilers are switched on and off (cycled) far too frequently; wasting energy, increasing emissions and reducing the longevity of the plant.
Excessive cycling may also be caused by the boilers coming straight on at high-fire, rather than coming on gradually. To maintain the design ΔT, the boilers should come on at low-fire initially, or modulate to meet the heat load, depending on the type of burner being used.
Nor is this challenge confined to cascades of gas-fired boilers. It is becoming increasingly common to use a biomass boiler to meet base heat loads, enabling building operators to improve their return on investment (ROI) through the Renewable Heat Incentive (RHI). Higher heat loads may then be met by gas-fired boilers, so in these applications the heating cascade comprises different heat sources using the biomass boiler as the lead boiler.
In these situations it is important that the control strategy recognises that biomass boilers are not designed for rapid on/off firing; they require some time to stabilise. So the controls need to allow sufficient tolerances for the biomass boiler to meet the set-point temperature.
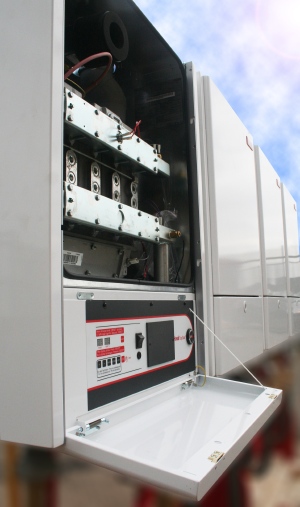
In parallel, bringing in gas-fired back-up boilers too quickly may cause the biomass boiler to switch off, so the full heat load is then met by the gas-fired boilers. As RHI payments are based on the heat supplied by the biomass boiler(s) this has a direct impact on the end client’s ROI.
The issues described above can be addressed through correct commissioning of the control systems. However, it is also important to recognise that as a building’s usage changes, the controls should be re-commissioned to reflect the changing heat loads. An obvious example is when the boilers are commissioned at the end of the shell-and-core phase of a development. As tenants move in and fit-out their own areas, the heat loads will change significantly, and the control strategy needs to be adjusted accordingly.
There are also many occasions where staffing densities change with time, or improvements are made to the fabric of a building, again resulting in a very different situation from when the heating systems were initially commissioned.
On these older systems there are significant benefits to building operators to check the boilers are configured correctly on a regular basis, perhaps as part of the routine maintenance. This is facilitated by the use of remote monitoring, which can be easily implemented for both gas-fired and biomass boilers. This would also be beneficial for those maintenance service providers that have guaranteed the energy performance of the plant they maintain.
All of which cries out for a better understanding of how heating plant should be controlled, perhaps through improved engagement between equipment suppliers and controls companies. It is also important to see the control strategy as a ‘work in progress’, rather than something that is set in stone when the building is handed over.
Kevin Stones is engineering and service director with Hoval.