Energy-efficiency insights
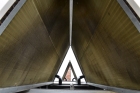
What goes into creating energy-efficient products such as chillers. George Hannah of Airedale International gives an insight.
Whilst air-conditioning and IT-cooling systems are intrinsically energy-intensive, cooling experts such as Airedale International invest significant time and resource in the development and rigorous testing of systems which minimise energy consumption. This article discusses some of the biggest wins in system design which are helping businesses to manage their energy efficiency objectives and ownership costs.
Our process for developing new products has for its primary objective, the development of cooling systems that achieve industry-leading efficiencies. It uses the latest CAD platforms and virtual-engineering techniques to maximise the use of internal space and ensure the heat-exchange area is configured to achieve the optimum cooling capacity for a given footprint. At conceptual stage, advanced design techniques such as computational fluid dynamics (CFD) are used to analyse a range of coil types and orientations to ensure the surface area for heat exchange is maximised and air flow improved.
This type of approach is typified by our latest SmartCool chilled-water precision air-conditioning unit. It has a high coil face area and V-frame coil arrangement (patent pending), enabling it to deliver significantly higher cooling capacity for footprint than equivalent models on the market whilst maintaining industry-leading efficiencies.
In addition, clever component design and the integration of advanced controls logic play a key role in system efficiency. Currently the latest technology includes the following.
• Heat exchanger. On chiller products, micro-channel coils arranged in a V-block formation increase the surface area for heat exchange — reducing airside pressure drop and allowing more airflow to pass through the coil. This increases the total heat rejection and fan efficiency to deliver better performance and control — particularly at part-load.
• Turbocor compressors. These centrifugal compressors can modulate output down to 25%, delivering tighter set-point management and significant part-load efficiencies during low-load conditions or in low seasonal ambient temperatures.
• Inverter controlled compressors. These increase part-load efficiency and deliver precise capacity match through staged DX cooling. Further benefits include low noise and reduced machine wear.
• Inverter-driven pumps. These pumps modulate water flow according to cooling load, reducing unnecessary energy and water consumption.
![]() |
CFD analysis is used by Airedale to determine optimum fan and heat exchange configuration and the best distribution and total airflow. |
• Electronic expansion valves (EEVs). These valves increase EER (energy efficiency ratio) by up to 30% compared with standard thermostatic expansion valves. EEVs deliver very precise refrigeration control whilst operating at part-load and lower ambient conditions with a reduced condensing pressure.
• Economiser circuits increase sub-cooling of the liquid entering the EEV, which improves system performance.
• Hot gas re-heat (HGRH). This technique typically uses up to 62% less power input in heating mode. Where heating is used during the cooling dehumidification process, HGRH offers an eco-friendly, re-heat capability by utilising energy that would normally be rejected outside by the condenser. HGRH is far more efficient than existing electric heat or low-pressure hot water as no further power input is required over the standard power requirement for the refrigeration circuit.
• EC (electronically commutated) centrifugal fans. With its highly efficient backward curved impeller, an EC centrifugal fan reduces power in comparison with equivalent AC fans at both full and modulated fan speeds by up to 70%. EC fans incorporate electronically commutated DC motor controls using semi-conductor modules which respond to signals from the indoor unit. The in-built EC fan control module allows for fan-speed modulation from 0 to 100%; in comparison, the modulating range of a standard AC fan is typically 40 to 100% of full fan speed.
• Carbon footprint can also be reduced by selecting systems like our TurboChill FreeCool which use refrigerants with a low global warming potential (GWP) such as R1234ze, which qualify for BREEAM points.
• HVAC controls and building energy management systems (BEMS). Intelligent controls technology plays an important role in optimising system performance and reducing power draw by using sensors to send and receive messages to and from active components such as compressors, fans and pumps so they interact with each other, balancing cooling duty, temperature, air flow and pressure to exactly match the application.
On sites with air-cooled and free-cooling chillers, the sequencer can be programmed so that the free-cooling chiller is the first to start up when the ambient temperature is low. A fully integrated BEMS will provide advanced energy-management capabilities such as live CO2 emissions and PUE power usage efficiency) calculations. The additional capability to control different zones and adapt parameters to suit peak and off-peak requirements also helps reduce energy consumption.
George Hannah is head of Airedale International’s 40-strong new-product development team . His remit is to steer the company's technology and innovation, with a focus on creating efficient solutions.