Fan-coil units exercise self control

Enabling fan-coil units to control the flow rate of water through them opens up a host of energy saving, installation and operational benefits. Peter Lowther of Ability Projects describes how they have led to the company’s first full Matrix project outside the UK.
The debate rumbles on about which is more energy efficient — chilled beams or fan coils — and everyone probably has a view on this. However, it is a fan-coil project that has recently been awarded the highest energy rating in New Zealand for an ‘as built’ building. ‘As built’ means the ‘occupied running reality’, not just the design expectation. The project, TPK house in Wellington, was Ability’s first full Matrix installation outside the UK and has been awarded the New Zealand Five Green Star Award.
The award was not only for energy efficiency per se but also included innovation points, one of which was for local fresh control air, which was managed by the integrated fan-coil strategy written and applied by Ability.
So what is it that makes TPK and Ability fan coils generally so efficient? It’s pressure — or, rather, the lack of it!
Building systems, be they airside or hydraulic, are loaded with devices that generate the need for more system pressure. Examples that spring to mind are air-volume control dampers, double-regulating valves, measuring stations or orifice plates and now, the pressure-independent cartridges of PICC valves. These are all devices that produce no cooling or heating effect themselves but are deemed necessary simply as a means to balance or quantify the system.
However, the reality with modern fan-coil systems is that all these elements can be removed, substantially reducing the continuous ‘energy-sapping’ pressure demands on air-movement fans and water-moving pumps.
The ePIV valve is an electronic pressure-independent valve; it has no mechanical pressure-equalising cartridge and requires no more differential pressure than is necessary to achieve the design water flow through it. In an Ability fan-coil strategy, the ePIV is the modulating flow-control valve but replaces the double regulating valves, measurement devices and even removes the need for local strainers.
The ePIV continuously modulates to provide the correct water flow rate by electronically monitoring the actual water flow rate through the valve and adjusting its position accordingly. There is no mechanical pressure-independent cartridge because it does not need one. Whatever the flow required and whatever the pressure, the valve will continually adjust to deliver the correct water flow to meet the duty requirement as defined by the control strategy.
Another benefit is that commissioning is vastly simplified. Via either the BMS, the supplied software or a physical switch on the unit, all the fan coils are instructed to open their valves to their design water flow positions. Given that there is enough water being provided to the floor or the branch and given a few minutes to settle, the fan coils will reliably achieve flow and report this to be the case. These confirmed flows can easily form the backbone of a commissioning/handover report.
The two water-flow tolerance values (upper and lower) are held within the Ability strategy, and the system will only be satisfied when the measured flow is within the pre-defined flow tolerance range. Further , as the ePIV itself measures and sets design water flows for commissioning purposes, the system requires no mechanical (pressure imposing) orifice plates; also because the valve has no mechanical pressure-independent cartridge to clog, no strainers are required local to the fan coil.
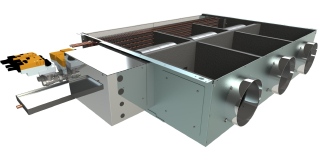
Ability’s own strategy continually polls all fan coils on a project to identify the greatest need (flow and pressure) at any time and then, through the BMS, optimises the pump speed to satisfy that maximum (index unit) demand — and no more.
The air flow on most Ability fan coils is, once again, a self-setting feature on the unit. The air volume per fan is input into the controller during the manufacturing process, and the unit automatically establishes those values once installed. These volumes are, in exactly the same way as the water flow, remotely adjustable using the software tools provided or through the BMS.
An Ability ePIV can play a large part in any 'soft landings' offering. Since the flow rates are uploaded in Ability’s factory and maintained electronically, they can just as easily be adjusted ‘electronically’. Most Ability fan coils can report to the BMS the various temperatures and values that enable occupiers or their FM team to establish whether the air conditioning is performing as per the design intent. If it is, then all is well and good, but if changes are required, be they minor or wholesale, the fan coils can be retrained, reset or completely reconfigured without the need for on site personnel to go anywhere near the actual unit. No desk surfers, no ‘high vis’ and hard hats wandering newly occupied floors looking for faults or making adjustments; remote continuous commissioning is the future.
This control strategy, which can include the new ePIV, has now been listed on the Energy Technology List, enabling a project take advantage of the Enhanced Capital Allowance tax breaks.
This new ePIV can be applied to all our fan coil ranges including EVO (standard ECs) and the Matrix ranges.
What differentiates fan coils from other product styles is their inherent flexibility in how they can be applied and how well they can adapt to changing requirements. A fan-coil installation may outlive a number of tenants, each of which will require a different usage for their spaces. With fan coils, especially remote setting types such as Matrix, the configuration of any building can change and can be changed every day if necessary.
Since fan coils are now every bit as efficient as chilled beams but undeniably more flexible, they inevitably have a prominent role to play in providing environmental comfort and energy effectiveness in building projects of the future. If further proof is needed, simply ask why would New Zealanders come all the way to the UK for a fan coil.
Peter Lowther is chairman of ability projects.