Is the UK obsessed with peak-load flow rate?
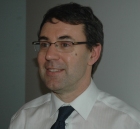
From experience with commissioning procedures, often informal, in other European countries, Chris Parsloe wonders if design return temperature is more important than flow rate.
UK commissioning procedures take a different approach from those in mainland Europe. In 1990 I spent an enjoyable time visiting design companies in France, Germany, Holland, Belgium Italy and Denmark to compare their commissioning procedures with ours. I wrote up the results in the BSRIA guide ‘European commissioning procedures’.
The upshot was that they were more relaxed about flow rates than UK engineers. There was a general acceptance that flows should be set within a tolerance of, say, ±10% but there was no proper witnessing or checking to confirm that these tolerances had been achieved. Unlike the UK, they did not employ commissioning specialists to set flow rates.
Furthermore, there was no formal responsibility for designers to witness and sign off the commissioning results. Instead there was a more pragmatic view taken that unless the system was shown not to be performing as intended, there was no reason to investigate flows. So flow rates were often set by the installer without checking by any independent authority.
This difference in culture even led to different valves being developed for the UK market.
On mainland Europe, the normal solution was to specify a variable-orifice valve. This was a valve where flow rate was determined by measuring the pressure differential across the variable opening of the regulating valve.
In the UK we preferred fixed-orifice valves where an orifice plate was close coupled to a regulating valve. The fixed orifice valve is generally more accurate and repeatable.
At the time, I took a view that our approach was probably the best out the countries that I visited and that waiting to see if there was a problem seemed a potentially risky approach that gave no reassurance to the client.
However, through the 1990s there was an ongoing debate in the UK about the relevance of flow rates to system performance. It was pointed out that for low-load sensible heating and cooling situations, close accuracy of flow rate setting was not critical to system performance. These views were expressed during re-writes of the various CIBSE and BSRIA commissioning documents — including the latest 2011 versions.
The insistence on tight flow-measurement tolerances has also given rise to problems for systems incorporating pressure-independent control valves (PICVs). These valves enable localised differential-pressure control across integral control valves. This means that the control valve will operate with better valve authority than a conventional 2-port control valve that relies on the presence of a separate differential-pressure control valve.
PICVs usually enable more accurate control of flows, which is good for thermal comfort and central plant energy efficiency. However, maintaining tight control over set flow rates is not their strong point. All differential-pressure controllers rely on the action of a spring to vary the position of the valve plug. As we know all, springs exhibit hysteresis, so how the spring behaves during its compression may not be the same as during its extension. This behaviour will be enough to cause any set flow-rate value to vary during normal system operation and by an amount sufficient to put the commissioned flow rate outside of the normally recommended tolerance band.
As a result, I am sometimes asked to give an opinion on whether set, peak-load flow rates that vary between, say, ±15%, are acceptable when the CIBSE tolerance is ±7.5%. I’d argue that in practice, most heating and cooling loads are so generously sized (and coils deliberately selected to allow for flow variations) that it would be astonishing if a ±15% variation from the design value were to be noticeable in the occupied space. Other engineers might take a different view — and hence a debate begins.
At the same time that we are pondering whether the acceptance of such a wide tolerance band is going to affect the system performance, other more important issues are ignored because they simply aren’t covered by UK commissioning guides. A good example is system return temperatures.
Part L has forced us to incorporate low-energy heat sources such as condensing boilers, CHP or biomass boilers into heating systems. But the predicted energy savings are only likely to be realised if return temperatures are maintained as low as possible (ideally 20 to 40°C). Therefore, a priority of commissioning should be to ensure that the design return temperature is achievable under both peak- and part-load conditions — yet we seldom do this check.
Designers and installers from countries with longer experience of low-carbon heat sources (and district-heating systems) do undertake this check and consider it a priority that over-rides the checking of peak-load flow rates which are seldom indicative of problems.
Overall, I have to say that I now lean more towards the European approach than the typical UK method.
Chris Parsloe is director of Parsloe Consulting Ltd.