Lighting control starts with power distribution
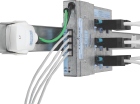
The power and control requirements of a lighting system are best considered together to achieve a flexible and cost-effective installation, argues Steve Marr of Legrand.
Future proofing is the expression on the lips of both clients and specifiers as the drive to deliver a more sustainable and less wasteful built environment continues. To this end, the ubiquitous lighting-control system has become a key element in specification strategies for reducing energy consumption and operational costs. However, many power-distribution installations are specified without sufficient consideration of the future flexibility they offer in terms of Category B fit-out lighting control compatibility.
To future proof a building’s control capabilities, specifying the most appropriate power-distribution system is essential, which is why Legrand has developed a CPD presentation specifically to develop understanding of this matter.
The various approaches that can be used include fixed cable, lighting busbar, modular wiring and a busbar system with integrated communications bus. A comparison of these options illustrates just how much the power-distribution specification affects the potential sophistication of the lighting-control system.
While any of the above types of power-distribution system could be installed in any environment, realistically they represent two tiers of specification.
• Fixed cable and lighting busbar are at the lower-specification end of the spectrum.
• Modular wiring and a busbar system with integrated communications bus are more suited for high end office or hospitality environments.
A fixed wiring installation offers low material costs and straightforward installation by a skilled electrical team, but the advantage of cheaper materials can be outweighed by the labour-intensive nature of the installation. Installation requires a relatively high number of circuits at the distribution board, with each circuit typically feeding four or six light fittings. Control is usually incorporated, with a standalone presence detector to switch each circuit, which provides no scope for intelligent, networked controls, and any additions or changes to the system would involve an expensive rewire.
A plug-and-play busbar installation, by comparison, may incur a higher material outlay, but labour time and costs are significantly reduced — making busbar a very attractive option both in terms of installed costs and simplifying an installation. A typical busbar installation requires fewer but higher-rated circuit breakers in the distribution board feeding 25 or 40 A lighting busbars with power accessed via tap-offs that can be plugged in as needed at regular tap-off outlets. These tap-offs may, for example, feed an 8-way marshalling box connected to six light fittings. The lighting output from the marshalling box is then controlled by standalone presence detectors.
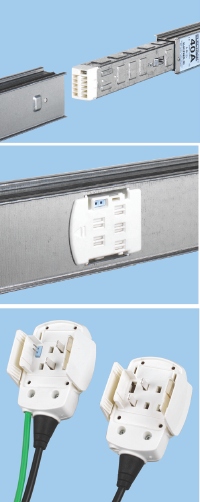
While this approach enables a fairly simple lighting-control system, there is potential for adding new lighting components thanks to busbar’s plug-and-play nature, which provides spare capacity to put in additional lighting on the busbar or at the marshalling boxes. Busbar may still not provide any potential for intelligent controls or networking of the control system, but it does offer an in-built flexibility — albeit within the same basic specification parameters.
For higher-specification buildings where lighting control is part of a wider portfolio of energy-efficiency measures, a more sophisticated control system is to be expected — possibly integrated with the BMS (building management system).
A modular wiring system can provide the infrastructure for networked lighting controls with the inclusion of communications circuits. This entails higher material costs than a traditional cabling installation, but an easy-fit system keeps labour time and costs low. A best-practice approach to a modular wiring installation is to build in spare capacity at the master distribution box (MDB) and lighting-control units (LCUs) to cater for future additions and adaptations. However, as the LCUs are fixed to the fabric of the building, subsequent changes that involve the need to move or add new control units will entail significant labour costs.
For example, Legrand’s Lightrak offers spare capacity throughout a system and provides an adaptable and future-proofed solution for an intelligent networked lighting-control system. It communicates using KNX and can control analogue, DSI or DALI lighting installations. The system requires fewer circuits on a smaller distribution board, with 25A or 40A circuit breakers feeding the Buscom system. Fused Buscom tap-offs then feed and network pre-wired, 9-output intelligent lighting control units onto the integrated communications bus. With this installed, the Lightrak LCUs themselves simply snap-fit onto the Buscom trunking with virtually no labour and pre-wired sub-cabling plugs into the LCUs to provide power and control to each luminaire.
A system like this offers quick and simple retro-fit possibilities. If at the Category A stage of an office fit-out, the lighting requirements of the final tenant are not known, developers can install a cost-effective lighting-control solution that can be upgraded to meet the additional needs of the incoming tenant.
Optimising energy efficiency with the right combination of controls is a key specification decision for any commercial building, but power distribution must also be considered carefully as a first and essential step to ensure that controls can be tailored in line with the building’s function, and sustainability goals.
Steve Marr is marketing manager for Legrand's power distribution business unit.