How to simplify the maintenance plan
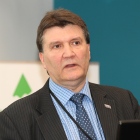
How much maintenance is really needed to achieve a building that operates satisfactorily? That is the focus of recently published guides, Andy Green discusses the success being achieved by a planned and structured maintenance scheme on the cost of maintenance and the life-cycle costs of buildings.
The planning and delivery of optimum maintenance solutions has long been a challenge for estate holders and end users, particularly in these current times when everyone is seeking ways to reduce running costs.
The UK Government’s efficiency agenda (Construction 2025) has mandated that the construction and maintenance industry must find a way of reducing total whole-life costs by up to 33%. That means public-sector projects and FM procurement must now get to grips with whole life cycle costing.
![]() |
This analysis of a maintenance strategy for HM Prisons highlights the percentage of total cost for the various priorities. Note the opportunity to save 22% by not over-maintaining (green tasks). |
In November 2012, the Building & Engineering Services Association (B&ES) updated the core SFG20 standard products for planned preventive maintenance to enable clients, contractors and consultants to customise their generic tasks schedules. SFG20 simplifies how to identify statutory/legal maintenance obligations — identified as red tasks in the guide (see diagram below). Sector or organisation mandatory compliance can also be identified, and are highlighted as pink tasks.
The new SFG20 now also includes a service modeller product. It provides an approach to customising maintenance service regimes using a simple way of prioritising function-critical maintenance and non-critical maintenance within controlled parameters that use industry-accepted methodologies and rules (defined in BS 8544; 2013).
The methods used in SFG20 also make it possible to assess the impact of maintenance on whole life cycle costing
Since 1922 the UK construction industry has used the RICS standard method of measurement (SMM) for cost management of capital building projects. However, until last year the industry has not had a standard method for managing the maintenance and renewal costs. Aligning SFG20 maintainable assets to the Royal Institution of Chartered Surveyors’ (RIC new rules of measurement for construction (NRM1) provided the basis for the RICS to produce new rules of measurement for building maintenance (NRM3 launched January 2015).
![]() |
Al of which means the RICS and its Building Cost Information Service (BCIS) have agreed the alignment of the construction cost data structure with the maintenance and lifecycle renewal works cost and asset structures to provide a standard method for lifecycle cost management that can overcome the divide between capital and revenue.
Having a common data structure linking buildings to maintenance costs will have a massive impact on how projects are handed over to be operated and maintained (Government soft landings). This should also have huge benefits for the UK maintenance industry as it will enable clients and other stakeholders to compare costs on a like-for-like basis during tendering and efficiency reviews. Adopting a common standard will inevitably change future asset registers and surveying, creating robust maintenance databases that will form the foundations for building information modelling (BIM) in FM and projects.
Table 2: Transforming way the maintenance impacts on life cycle costs. Contractors/ customers/end users/operators • Assurance of legal and mandatory compliance — red/pink tasks + compliant links • Not under- or over-maintaining the assets — based on function criticality risk rating • Ability to model level to suit business use of space — e.g. fit-for-function standards Financial • Baseline to set/defend budgets (set minimum legal and fit for function service model) • Efficiency savings v old PPM regime (criticality based use of the resource and costs) • Fairer procurement (comparable basis for tendering) and demonstration of value for money Environmental • Less downtime on key plant and equipment — business focused on critical asset types • New specification produced for renewable assets (e.g. biomass boilers and solar panels) • Energy focused maintenance — (future update) embed into standard task specifications |
This objective was achieved after extensive cross-industry collaboration and consultation with the professions/institutions and trade associations (RICS/BCIS, CIBSE/ BSRIA/ B&ES), large estate client organisations, practitioners and service providers from across the building and maintenance industry.
Many client organisations have now adopted the new maintenance standards and customised the SFG20 service regimes to ensure they are fully compliant and not under- or over-maintaining their assets. For example, the Ministry of Justice has developed a sector maintenance standard for HM Prison Service in conjunction with B&ES (Table 1). The standard has customised all applicable SFG20 tasks schedules and also added new sector-specific task schedules for specialist security and the maintenance of the building fabric.
As a result of customising SFG20 to its requirements HM Prison Service has now applied a national sector standard across 131 establishments and over 7000 buildings, the benefits of which are summarised in Table 2.
Andy Green is vice chairman of the SFG20 technical standards committee. This article is based on his presentation at the Building Services Summit 10 80 10.