The heat is on for boiler control
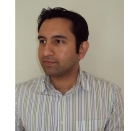
Lowering utility bills and being more sustainable are high on the agenda for most organisations, yet boilers across the nation continue to be inefficiently operated. Yasar Butt of Trend Control Systems, explains how anti dry-cycling measures can achieve significant energy savings when introduced into a Building energy management system (BEMS).
It is the time of the year when spring cleaning a BEMS and checking that it is working to its optimum levels should be carried out in order to make instant savings. As well as adjusting operating times and setpoints, one item that should not be forgotten is to put measures in place to avoid boiler dry cycling.
If at this point you are scratching your head, let me explain. Dry-cycling is the term used to describe a situation where a boiler or heating system operates when a building it serves does not require it. This happens because the system is being switched on by something other than a true heating demand — usually time clocks or optimisers — which operate with minimal influence from the temperature conditions inside or outside of a building.
The problem is that, particularly in spring and autumn when outside air temperatures can vary considerably, a boiler system could be unnecessarily operated for most of the occupied time, irrespective of the demand from the occupied space or the need for additional heat.
This could result in heat flowing to parts of a building that are already up to temperature, thermal losses resulting from the hot water being needlessly circulated around pipework systems, as well as boiler efficiency losses associated with being switched on and off unnecessarily to maintain a flow temperature without a true demand for heating. Ultimately, it all adds up to higher bills as a result of wasted energy and carbon emissions.
The good news is that anti dry-cycling is cost effective and easy to implement. Where an existing Trend BEMS is in situ, simply adjusting the control strategy can achieve significant savings by closely monitoring boiler flow and return temperatures, and then using this data to assess real demand, then increasing time delays between firing cycles if possible. Contrary to the claims made in some sections of the controls industry, there is no need for expensive ‘optimising’ hardware to achieve this objective. This simply is not needed, as a basic software optimisation process will achieve the same result.
By modifying an existing control strategy and monitoring flow and return temperatures, a system can be configured so that the boilers only fire up when there is an actual demand. Adjustments are available for setting temperatures for the maximum time that activation can be held off when a call for heating still exists.
Usefully, daily energy usage profiles can be created to compare actual and expected consumption. If actual energy consumption exceeds expected energy consumption by a preset amount, an e-mail report can be automatically generated and dispatched. This permits rapid diagnosis and rectification of any problems, thereby limiting energy waste and unnecessary expense.
To further maximise energy savings, boiler anti-dry-cycling strategies can be combined with a demand-led system that looks at the loads on the building giving rise to a heating requirement and, in turn, allows the BEMS to make intelligent decisions about whether the heating system is required at all.
This approach enables additional savings from shutting down pumps and, indeed, the whole boiler system if there is no appreciable requirement for heat — a situation not uncommon in today’s commercial buildings, which are well insulated and contain large inherent heat sources from lighting, electrical and IT systems.
In some larger buildings the way that a traditional boiler firing sequence is controlled means that it is given a period of time in which to get to a desired temperature. This often involves firing up multiple boilers, which isn’t always necessary, especially when reaching a specific temperature might not take very long. An anti-dry-cycling system can be configured to recognise situations where this could be avoided and prevent boilers operating inefficiently for short periods of time, reducing gas consumption and limiting wear and tear on the plant.
Dry cycling does not enhance comfort — it just wastes energy. A carefully specified, implemented and optimised BEMS can avoid this often overlooked and potentially expensive problem and help make instant savings. With growing regulatory and legislative pressure to reduce carbon emissions and lower energy usage, this is an opportunity that the owners and managers of buildings can no longer afford to ignore.
Yasar Butt is energy solutions specialist with Trend Control Systems.