Taking stock of lighting control in warehouses
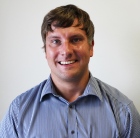
With lighting everywhere but often very few people, lighting control in warehouses can pay rich dividends — as Rob Crookes of CP Electronics explains.
While many companies tend to focus on lighting within offices, there is a strong case for energy- and cost-saving measures within spaces such as warehouses, where lighting can account for more than 50% of the total energy budget.
Advances in lighting-control technology enable end users to manage their energy consumption, and, on the strength of the financial benefits alone, there is a compelling case for immediate action.
In many respects a warehouse is not unlike an office building because there are several different types of control scenario to suit every warehouse space and the way in which it operates.
Presence detection is a very common example, allowing lights to be switched on as required, for instance when someone is picking in one of the aisles.
Another scenario would allow for the lights to be switched on when someone enters a specific area and then dim when they leave, ensuring that there is always a minimum level of illumination for safety purposes.
A further notable example is the use of daylight harvesting, which allows lights to be switched on when someone enters an area but then automatically adjusts to the level of natural light within a specific area.
What these examples share is that they all harness control technology to deliver significant energy savings.
Whichever scenario best suits the needs, the success of the lighting controls depends on the types of controllers which are installed. PIR (passive infrared) detectors are a common choice and work by detecting moving heat, whether this is generated by people or machinery.
What is crucial, however, is that the correct type of detector is used. For example, when mounting at height, high-sensitivity long-range detectors (such as the CP Electronics EBDHS range) are essential.
If a longer detection range is required, microwave or HF detectors are ideal and work by using low-power radar to detect moving objects. However this type of detector can be triggered with any movement such as loose packaging so the likelihood of lighting being switched on as a result of ‘false triggers’ is fairly high.
In addition, lux sensors are often incorporated into the PIR or microwave detector so that the area is only illuminated if the natural light levels are not sufficient. This is an excellent way of making use of natural light and provides additional energy savings.
One of the main considerations when implementing a lighting-controls solution is the correct selection of the control device. Close consultation with the luminaire manufacturer is advisable as this ensures compatibility with the selected product; this process may involve testing the proposed luminaire type with the control device.
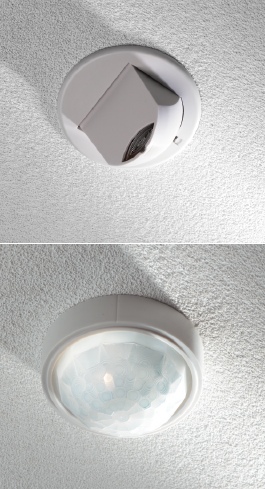
The second most crucial consideration is the type of environment. Care needs to be taken when siting control devices as the ambient temperature may affect their operation and range. Also, the number and positioning of devices is crucial to ensure there are no blind spots and that moving objects such as fork-lift trucks and lifting devices activate the control device as and when required.
The next step is to understand how and when the warehouse is in operation. For example, a 24-hour warehouse which is constantly occupied would benefit from some form of daylight control, which either switches the lights off or dims them down as ambient light becomes available.
A warehouse that has occasional picking of items from aisles would achieve maximum energy savings by utilising some form of occupancy control on the lighting.
Where a warehouse has a number of different shift patterns with different lighting requirements, a networked solution, available in wired and wireless options, could be advantageous.
A major advantage of a wireless network (like the CP Electronics An-10 system) is the ease of installation and flexibility as it can be moved and scaled as required. However, a wired system (such as the CP Electronics RAPID system) may be preferable in very large installations or where the environment is hostile to wireless communication.
There are, of course, numerous additional considerations which must be taken into account, such as the need for minimum levels of light for safety reasons. Perhaps the most important consideration, however, is ease of use, almost negating any need for end-user intervention.
The ability of lighting controls to achieve energy savings is widely publicised but generally speaking the examples only refer to office environments. Historically, little attention has been paid to lighting in warehouses despite this type of environment quite often having the highest energy bills.
This is undoubtedly an area which we are now addressing because there are considerable energy and cost savings to be achieved by installing energy-efficient luminaires in warehouses and then controlling them correctly.
If we use the same approach as we do in office buildings to understand the usage of the space and introduce the appropriate control regime, then not only will the installation costs be minimised but savings will be effective immediately — a fact which is difficult to overlook for any company.
Rob Crookes is product manager with CP Electronics.