Abolish Part L and design buildings that work
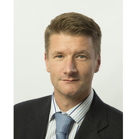
Part L of the Building Regulations stifles innovation and embeds poor long-term performance into buildings, says Tim Rook of the Building Engineering Services Association.
If we can’t achieve total abolition of Part L of the Building Regulations, the industry should at least lobby for a root-and-branch revision of it. Without a dramatic change in direction, we will never be able to answer the increasingly anguished calls from clients for buildings that are fit for purpose.
Part L encourages a ‘tick-box’ mentality and a wholly unimaginative approach to building design that is condemned to fail before it even starts. This applies just as much to refurbishment of existing buildings as new projects.
We design too much for compliance and not enough for performance. Clients are rarely expert or well enough informed to specify for performance in their design brief. Instead, the team starts working towards a BREEAM and/or EPC rating that is purely theoretical.
A system that promotes SBEM (Simplified Building Energy Model) for non-domestic buildings, SAP (Standard Assessment Procedure) for homes and BREEAM ‘scoring’ of buildings is entirely unsuited to driving performance design as it gives developers carte blanch to simply select the lowest-cost option for compliance, irrespective of the building context or actual usefulness of the technology selected. It simply delivers to an arbitrary set of rules established from poor quality data sets.
Leeway
As a result, design decisions are made by non-experts for the wrong reasons, and there is no leeway for new ideas and technologies that are outside of ‘the box’. Engineers are, therefore, unable to properly ‘engineer’ the project in hand.
Part L calculations are not energy-performance metrics because they use arbitrary or standardised data in a bid to come up with a simple equation. Variables like dynamic weather conditions and unregulated energy usage, which in many cases accounts for over 60% of total energy consumption, are simply ignored. There is also very little possibility of reflecting how the building is to be used and operated in the simplistic terms of Part L.
Standardised design data is completely hopeless for calculating how complex building-services systems are likely to operate under real conditions. It is difficult (impossible even) to determine what is the ‘performance gap’ because you are not designing for performance, but simply aiming for the lowest common denominator that gets you over the line for compliance and planning consent.
The Government is currently consulting on the future of SAP, which creates a rare opportunity to make a change that will benefit everyone. How can you improve and measure performance in the real world if design is based on current SAP methods? This is the industry’s chance to influence the future direction of SAP, and BESA will certainly be making a strong representation for robust changes on behalf of its members.
As well as being restrained by the demands of compliance, engineers become very focused on the exact geometries needed to create BIM (Building Information Modelling) models at an early stage of the design process. This means they don’t spend enough time thinking about the overall physics of the building. The fact that computing technology now enables us to create thousands of versions of a model very quickly does not mean that we should.
The Latham Report of 1994 kicked off an important change in our industry by exhorting consultants to design less and contractors to design more in order to get buildings that perform better in practice. BIM is turning back the clock and reversing this process by encouraging too much early detail and technology-focused design — often for buildings clients can’t afford and which end up being ‘value engineered’ out so eating into crucial design time before the project starts on site.
A far better solution would be to impose a simple performance metric measured in kg of CO2/kWh or kWh/m2. This would allow the engineering team to come up with the most appropriate way of achieving the target without locking themselves into a particular set of technologies — and with the complete building in mind.
The measurement would be checked and verified on completion, but also reported against annually to make sure the building remains on track. This would give the client a way of measuring the inherent value of their building — rather like the principle of miles per gallon (MPG) used to measure actual performance of a car.
The rapid emergence of the Internet of Things (IoT) gives us an opportunity to measure and monitor more values and to do so more effectively. The availability of thousands of low cost nano-sensors that can be linked into a Wi-Fi network allows us to capture performance data much more effectively.
Inspiration
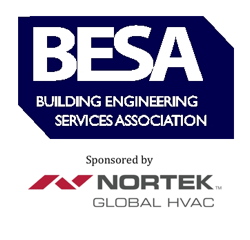
The time is right to revisit the compliance model. Things are changing, and more engineering firms are advising clients to insist on operational targets in their project briefs. Some UK firms are now taking inspiration from NABERS (the National Australian Built Environment Rating Scheme). This is now compulsory on all public-sector buildings in Australia and is closing the loop between building performance, occupant satisfaction and commercial value.
Private-sector clients who adopt the scheme gain competitive advantage in the property market for having a higher NABERS rating because it scores their building in terms of actual environmental impact in use. It demonstrates a significant value return on investment and makes the link between energy efficiency; occupant comfort, health and well-being, quality and sale or rental value.
The WELL Building Standard that factors human health, well-being and productivity values into its assessments is also gaining traction with employers concerned about the impact of poor internal spaces on their workforces. Developed in California, it is now being used in 21 countries around the world and some of its values are being added to the BREEAM rating scheme for the UK.
Whatever methods the industry uses, clients are determined to see change. Sarah Ratcliffe, programme director at the client group Better Buildings Partnership, told the recent CIBSE Building Performance Conference that her members were desperate for more accurate performance data and now expected their supply chains to design for long-term operation.
She said, ‘Engineers’ simulations ignore process imperfections and how buildings are operated. It is not clear who is responsible or who is incentivised to make buildings perform well. This is not a technical issue, but a cultural and process problem.-
This ‘really matters, according to Ms Ratcliffe, because ‘property owners are now being asked for performance data from their investors. They also have to comply with a range of mandatory and voluntary reporting and disclosure requirements. And … it gives them a competitive edge and helps drive cost savings.’
She said that building-services engineers had ‘fallen into the trap of focusing on design … when they should give equal weight to commissioning; delivery; operation and refurbishment’. As an industry, we need to ‘get the basics right and focus on outcomes for people’.
Adapt
Her comments were echoed by one of the UK’s largest estate management companies. Debbie Hobbs, sustainability manager at Legal & General Property, believes the building engineering supply chain does not understand how buildings are operated and so fails to adapt its designs and systems to the end user.
She also points to the flaws in the project process right up to the point where facilities management is procured at the lowest cost. As a result, built assets are undermined because of the ‘very low skills base’ involved in their operation.
A radical review of the process would make it possible for asset managers to procure FM based on their operational requirements — clearly set out in the performance metric against which the FM would be measured annually. This would also give the building-management team a chance of getting to grips with unregulated energy use and finally challenging the inexorable rise of energy costs and carbon emissions in line with their corporate reporting obligations.
Abolishing Part L would give building owners a chance to measure the real commercial value of their built assets and allow engineers to actually engineer.
Tim Rook is technical director of the Building Engineering Services Association (BESA).