St Paul’s Cathedral gets Hamworthy makeover
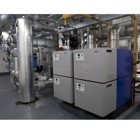
Following 50 years of service, the three steel shell boilers serving St Paul’s Cathedral in London could not be repaired any more and have been replaced with Hamworthy Wessex Modumax mk3 condensing boilers with a total output of 1016 kW. At the same time, new plant to provide domestic hot water was installed.
The cathedral is Grade I listed which posed a series of problems, in addition to the technical issues.
Robin Bunton of Bunton M&E Services advised that replacement boilers were necessary and worked with Mike Crouch, Hamworthy’s agent for the area, and Nick Coates from Blue Print Building Services Design on the specification for the heating and hot-water refurbishment project with clerk of works Martin Fletcher.
The installation comprises two stacks with two boilers in each that can deliver any output from 50 to 1016 kW. These boilers fit through a standard doorway, providing the installation flexibility needed.
Six months before the boilers were installed, two MagnaClean filters were installed to clear sludge and debris from the heating system, followed by a system flush. The boilers and the heating system were separated by a plate heat exchanger. The completed plant room was fabricated and built off-site at Bunton M&E Services’ workshop, dismantled and delivered to site — reducing the total installation time on site to just four weeks.
Flueing requirements were met by running a FuranFlex flue liner down the length of the 30 m rain water chute into the plant room.
Commenting on the success of the project, Robin Bunton says, ‘The speed of heat up has greatly improved. Previously it would have taken a week to heat the cathedral up from cold, but now it only takes one day. The heating runs 24/7 on weather compensation.’
The cathedral is a popular tourist venue, with coach parties using facilities such as toilets and catering in a relatively short period, causing an extremely high peak demand. Two Hamworthy Powerstock glass-lined calorifiers, each with a capacity of 500 l and a recovery time of 18 minutes, were chosen. It was not possible to get a 1000 l calorifier into the plant room, hence two 500 l units.