Delivering indoor air quality
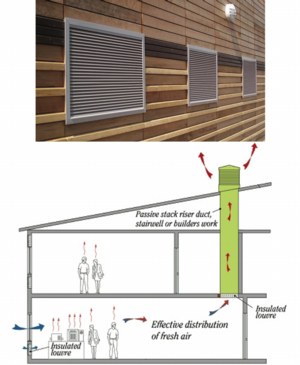
• Stack effect: Rising warm air causes pressure differentials across the building envelope, which are generally positive at high level and negative at low levels.
• Mechanical systems: Heating and ventilation systems create positive or negative pressures within the building. Any one of these driving forces, or a combination of all three, will lead to air leakage through any cracks or gaps in the building envelope. This leads to cold external air moving into the building, and warm internal air moving out of the building. It is now widely accepted in the UK that there is little merit in improving the effective U values required for envelope assemblies unless the levels of uncontrolled air leakage through them are significantly reduced. The significant energy penalty which uncontrolled air leakage causes has been recognised within the amendments to Part L (Conservation of Fuel & Power) of the 2006 Building Regulations. These amendments introduce maximum envelope air-leakage standards for domestic and non-domestic buildings. Air leakage does not solely waste energy in heat being lost from the building and air handling systems having to work harder to compensate. It also creates draughts, noise transfer and poor indoor air quality, which inevitably affects occupants’ performance. Ventilation strategy The ventilation of a building should therefore rely on a designed strategy based on the assumption that the envelope will be relatively airtight and meet the requirements for fresh air recommended in CIBSE Guide A. Government pressure to reduce carbon emissions and energy consumption is leading more companies to adopt as sustainable an approach as possible. Low-energy systems should be designed from the outset to provide as near to the required air change rate as possible, to prevent energy-wasting over-ventilation. Designers and specifiers have an abundance of ventilation strategies from which to choose — ranging from systems that are totally natural or totally mechanical, or a combination of the two (mixed mode). Natural ventilation requires little or no energy at all; Passivent Aircool units, for example, use only 1 W of electricity to operate, but other elements use no electricity at all. Natural ventilation depends on the pressure differential of the external and internal environment to provide the natural air change. Naturally ventilated buildings typically consume less than half the energy of air-conditioned buildings, their capital costs are typically 15% lower, and less space is required for plan rooms and services distribution. Research also shows occupants perform better in naturally ventilated buildings. Mechanical ventilation can be provided by a fan system at varying air-change rate, depending on requirements. The fan can be chosen according to the air-change requirements calculated for the specified area, occupancy level and occupancy activity. In addition to the ventilation fan, it is possible to have a heat-recovery system that can reduce the cost of cooling or heating the incoming air by recovering some energy from warm or cool exhaust air. This system will cost more, but heat recovery reduces heat losses and the heating demand. Mixed-mode ventilation delivers accurate environmental control while minimising energy consumption. The system uses natural ventilation as far as possible and only uses air conditioning to heat or cool when required by rising internal demands or changing climatic conditions — and then operating it at part load. Natural, mechanical and mixed-mode ventilation can achieve further energy savings by matching the flow rates delivered to demand and introducing control to the operating times through system controls. Ventilation rates may not need to be constant throughout the day, especially if building occupation varies during operating hours. Variable damper opening controlled by levels of carbon dioxide or process pollutants can be used. As the need for ventilation increases, the damper opening increase and more air is brought in. Advances in software enable the efficiency of a system to be tested prior to installation, using thermal modelling to predict the thermal efficiency and ventilation performance — so there is ample scope for specifying a ventilation system that works properly, keeping occupants in a pleasant environment that is suitably cool in summer and warm in winter, without draughts or dampness, instead of relying on gaps within the building fabric. David Stolton is product manager with Passivent Commercial.