Showing the way to energy-efficient refurbishment

The move to an existing building gave Chalmor the opportunity to upgrade it and massively improve its energy efficiency, including some novel ideas — as Ken Sharpe found out.
Even if all new buildings were to be zero-carbon, whatever that might mean, Government targets for reducing carbon emissions in the UK will not be met. Existing buildings have an equally, if not more important, role to play — simply because there are so many of them, their slow rate of demolition and the small number of new buildings completed each year.
A fine example of what can be achieved is the newly refurbished building of Chalmor in Luton. The company specialises in energy-saving controls and lighting and therefore fully understands the benefits of these technologies and how to apply them. The building is on a small industrial estate near the centre of Luton and immediately adjacent to Chalmor’s previous building. It provides offices, warehouse space and testing facilities.
The previous building provided Chalmor with 120 m2. The ground floor alone of the new building is 200 m2, and the addition of a mezzanine floor increases the area to 350 m2.
The headline figure, says commercial director Barrie Morris, is an 80% reduction in energy consumption compared with the existing systems in this 27-year old building. The payback on the investment is expected to be within five years. The project enjoyed the support of a £25 000 interest-free loan from the Carbon Trust toward the £175 000 total cost of the project.
The building doubles up as a showcase for energy-efficient technology, as managing director Steven Henry explains. ‘Because this new facility serves as both a working office and a showcase for our energy-saving products, it incorporates a much wider range of lighting products and controllers than might be the norm. It also illustrates the significant return on investment that can be achieved through selection of such products.’
Included in the services mix are reverse cycle heat pumps to provide heating and cooling, energy-efficient light sources and a high level of control — as befits a company with expertise in controls.
There are also some other novel ideas for reducing energy consumption. One is a dedicated electrical circuit for equipment that can be switched off at night, such as computer monitors. The electrical supply to this circuit is interrupted when the building is not occupied. The computers themselves are served by another circuit so that they can be left on if necessary.
Security is a major issue, and it has been addressed using CCTV with night vision rather than 400 W of external floodlights to reduce energy consumption. There is external lighting, but it is only turned on in response to suspicious activity.
Much of the existing building fabric has been retained, avoiding the carbon emissions that would have been associated with demolishing it and putting up a totally new building on the site.
Externally, little has changed. There is a new entrance, and windows have been added on the northerly aspect; there were no windows before, just translucent panels in the roof.
A mezzanine floor has been added inside to provide space for offices.
Such a major refurbishment first requires attention to the building fabric to improve its U-value. There was previously 100 mm of insulation in the walls, and this has been increased to 200 mm. Where windows have been installed, the original insulation below them has been removed and replaced with just 50 mm of Celotex foil-backed insulation to achieve the same U-value as 200 mm of fibre. The roof insulation was also increased to 200 mm.
At one stage, insulating below the warehouse roof lights was considered, but it was decided that the energy-saving potential of daylight was greater than could be gained simply by the reduction in heat loss.
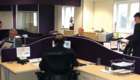
Ideally, Steven Henry and Barrie Morris would have preferred their new building to be naturally ventilated. However, the side of the building with windows faces a pub kitchen and its associated cooking smells. Opening windows to cool the building in summer would not have been a good approach.
To find efficient heat-pump technology, the Energy Technology List was consulted — enabling the project to qualify for Enhanced Capital Allowances.
Although the equipment selected was capable of delivering efficient heating and cooling, what the Energy Technology List did not indicate, however, was that it had only 24-hour programmers — not 7-day programmers to avoid it operating over weekends.
That shortcoming presented no problems to Chalmor, which simply adapted its own controllers to deliver even more effective control than a 7-day programmer by integrating the operation of the heat-pump heating and cooling systems with control of the lighting.
While the building occupants can use the 24-hour programmers, a higher level of control is provided by Chalmor universal controllers for preheating the building and using information from the same presence detectors that are used to control lighting to disable heating/cooling units if offices are not occupied.
Interior lighting is controlled in more zones than would be normal in a building of this type and usage to demonstrate the capabilities of such control products — but it is also proving to be functional.
All lighting is controlled by occupancy sensors, with daylight sensors to dim lights down to 10%. Dimming lamps has a much less deleterious effect on their life than switching them on and off.
The main staircase off the entrance hall with its full-height glazing and glass doors receives a lot of daylight, and Barrie Morris remarks how often sensors turn off lights when nobody is using the stairs. The stairwell is also used to demonstrate Chalmor’s high-powered Endurance fitting, showing how quickly it strikes and comes up to full brightness.
This being a building with a realistic budget, areas that are not generally occupied like corridors and the entrance hall are heated by direct-acting electric panel heaters with sophisticated control. Likewise water for the toilets is heated electrical, with one 2.5 kW water heater serving all three toilet areas (male, female and disabled).
The warehouse area is not heated at all. It is not normally occupied, and staff working there are provided with extra warm clothing if required. Lighting for the racking area in the warehouse is normally off and activated by PIR sensors.
Finally, to reduce the carbon footprint of the building’s services to zero, Chalmor has negotiated a green electricity contract with EdF.
If all empty buildings could be refurbished to this level of energy efficiency before being re-occupied, Government targets for reducing carbon emissions could soon be met. Will the adjacent building left unoccupied by Chalmor receive an equally energy-efficient refurbishment?