The need for RH in IAQ

Optimising indoor air quality requires attention to very detail, not just filtering out airborne particles. Dean Ward considers the role of humidification.
When considering indoor air quality (IAQ) there is often a focus on the particles that may be found in the air, such as dust, pollen and microbes — and quite rightly so because of the health problems they can cause. However, one thing that many building operators, and some building-services specifiers, overlook, is the humidity of indoor air. Yet failing to maintain an appropriate relative humidity (RH) in a building can be as much of a risk to health as airborne particles.
For example, when the RH is above 60% people feel uncomfortably hot and listless — beyond what would be expected from the actual temperature. If, on the other hand, the RH is below 40% our mucous membranes start to dry out, causing a feeling of constant thirst and leaving us more vulnerable to infection by airborne pathogens. Other symptoms include dry and itchy eyes.
Further, low RH can make the air unhealthy for the machines that modern working practices can rely on, causing problems such as a build up of static electricity. And while it may not be an IAQ issue, low RH makes people feel colder so they turn the heating up —reducing the RH even further, as well as wasting energy.
For all of these reasons, many organisations recommend maintaining an RH of 40 to 60% in commercial workplaces. These include the Humidity Group of the Hevac Association, the World Health Organisation and the National Association of Optometrists. This is also the range recommended by BS EN 29241 as the optimum for visual display terminals.
This situation tends to be worse in the winter, as many systems rely on the introduction of tempered fresh air to the building to maintain an appropriate RH. In cold weather, though, the moisture content of outdoor air (absolute humidity) will already be low, and this will be exacerbated by the heating system. Thus, in many workplaces, the indoor RH in many such spaces consistently falls below 25%, giving rise to complaints of dry eyes, sore throats, coughs and lethargy and resulting in increased absenteeism.
Clearly, then, there is a strong case for maintaining the RH at 40 to 60% as part of an IAQ control strategy, but how best to go about it? There are many options for humidification but it is important to select the most appropriate in terms of energy performance and cost of ownership.
Ironically, the most cost-effective solution (adiabatic humidification) is often rejected because of concerns about IAQ. Historically, adiabatic systems have caused concerns about the spread of micro-organisms, dust and allergens — deterring many people from taking advantage of the energy-saving benefits. However, this perception is outdated and does not take account of the technological advances that have been made in this respect.
As a strong reason for opting to use adiabatic humidification is that energy is not used to heat the water, an alternative to pasteurisation has to be found to control waterborne micro-organisms; there are several alternatives, with variable effectiveness. Adding biocides to the water is one option, but a costly one. Irradiating the water with ultra-violet light can be effective, but only in the areas that are fully exposed to the radiation. Every system has edges, corners and other areas the radiation will not reach, and UV radiation will not prevent bacterial growth in non-irradiated areas.
In providing a cost-effective solution that addresses both IAQ and humidity control, it is necessary to take an holistic approach and look at every aspect of the system, starting with the water itself. Using fully demineralised water will ensure a high standard of hygiene right from the start, and this can be combined with other mechanisms to provide enhanced protection.
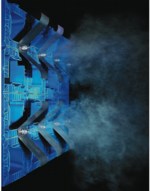
Water vaporisation also needs to be highly efficient so that no water aerosol droplets are allowed to accumulate in the system and create potentially hazardous pools of water. Some modern adiabatic humidifiers address this requirement by using molecular, low-pressure (4 to 6 bar) nozzles with ceramic orifices to create an homogenous spray mist that immediately starts to evaporate in the air flow. With the right design, the absorption distance is very short, minimising water consumption and reducing cost of ownership.
To further increase evaporation efficiency, the airflow then passes over highly porous, adjacently-arranged 50 mm-thick ceramic plates so that any mist deposited on the plates evaporates into the passing air, raising efficiency levels to over 90% while enabling rapid drying when spraying stops.
As an extra precaution, the system should automatically drain humidifying water out of the lines every 12 hours, during a system shutdown — with additional system purging every time the system is reactivated.
As noted earlier, any such system also requires supplementary measures. Adding silver ions to the humidification water by electrolysis, in proportion to the flow rate, has proved very effective in killing micro-organisms. In addition, the silver in aerosols subsequently accumulates on the ceramic plates, creating an additional layer of protection within the system. In parallel, of course, any such system should be regularly maintained by engineers who are experienced in ensuring optimum performance from humidification plant.
In these ways it is perfectly possible to create an environment where all aspects of IAQ are addressed, without a major impact on lifecycle costs.
The increased productivity from a healthy and comfortable workforce will more than compensate for the relatively small investment required.
Dean Ward is applied product manager with Walter Meier (Climate UK).