Delivering the benefits of variable-speed pumps
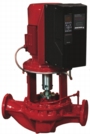
Enjoying the energy-saving benefits of adding variable-speed pumps to existing systems requires modifications to the system. Wayne Rose shares some ideas.
Many carbon-reduction strategies, particularly those qualifying under the CRC Energy Efficiency Scheme, will harness the energy-saving potential of moving from constant-speed to variable-speed pumping. The replacement of aging fixed-speed pumps with variable-speed alternatives is one of the ‘low-hanging fruits’ of carbon reduction — with a typical payback of just one year. As the pump is not forced to operate at full speed at all times, it can be expected to have a longer life. The lower water velocity reduces waterborne noise, and there is no check-valve chatter as the variable speed pumps work on soft start and soft stop.
When planning the migration to variable speed, however, it is important to avoid certain misunderstandings. For example it is commonly assumed by building owners and operators that a system can be converted to variable speed, with all the implied energy and cost savings, merely by installing an adjustable-frequency drive onto the pump motor.
In reality, the system piping inside and/or outside the plant room may require modifications to achieve the true energy-saving potential. This article aims to highlight the most important considerations and suggest effective upgrade strategies.
The most commonly missed opportunity is to leave the system unchanged when the pumps are upgraded to variable speed. With 3-way valves installed, for example, there is no opportunity to reduce the pump flow, as the valve will divert flow as demand is reduced. This results in constant pump flow through the installation, even though the pump is equipped to deliver more efficient part-load pumping.
If the system is adapted however, by closing the bypass valve, the 3-way valves effectively become 2-way valves. With the bypass closed, when the 3-way valve modulates to attempt to divert the flow through the bypass, it will restrict the flow rate instead (Fig. 1).
An Armstrong IVS Sensorless pump (with an on-board variable-speed drive) will sense this deviation from its control curve and reduce speed until the pre-set control curve, the system resistance curve, and the pump performance curve at the new speed converge for the new operating point. In this way power is saved and operating costs are reduced. Water velocity and noise are reduced, repair intervals are extended.
Variable-flow HVAC systems converted from 3-way control to 2-way valve control can experience certain challenges when the 2-way valves are shut off. For example, the pump may overheat when it continues to run against a closed valve at its minimum speed, with the risk of premature seal failure or thermal-shock cracking issues if cold water is suddenly allowed into a hot cast-iron casing. The temperature of conditioned water in the headers and remote risers, now stationary, will decay to ambient. When heating or cooling is next needed, there could be a delay in delivering freshly heated or cooled water from the plant room, up the riser, and along the floor to the terminal.
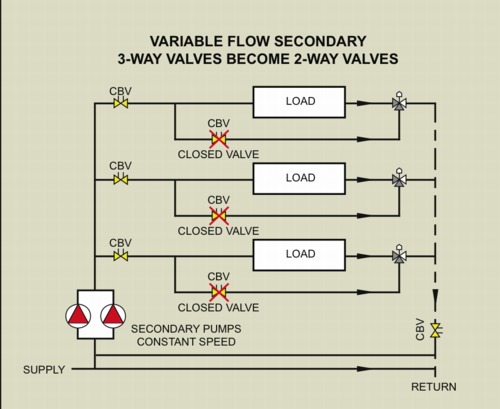
A simple solution is to simply leave the most remote 3-way valve bypass line open on each riser. If there are few loads in the zone, close the most remote 3-way valve by 50% so that energy is not wasted by too much conditioned water being returned unused to the chiller or boiler. In this way, water will only be bypassed when the remote load (typically the least served in the system) is satisfied.
Another good (although more complicated) bypass control option is to mount both the bypass and the differential pressure sensor remote to the pump on the index line. To operate effectively the minimum frequency on the drive control must be set high enough at low load to ensure the pump will operate at its minimum set speed and move left up the performance curve (Fig. 2), increasing the pressure at the index and causing the bypass valve to open. The closed-valve pressure of the pump at its minimum frequency must be 25% higher (12% higher frequency) than the control pressure setting of the pressure transducer at the index.
One of the most problematic elements in many variable-speed upgrades is the location of differential-pressure sensors remotely in the system. The exact position for the sensor is often difficult to determine, and sensors are prone to failure. Armstrong, for a number of years, has recommended IVS Sensorless pumps with on-board variable-speed drives, as these make the differential-pressure sensor unnecessary. These pumps are now available with variable-speed drives up to 55 kW, and the IVS102 range of standalone variable-speed drives is suitable for use with pumps rated up to 450 kW.
Our technical white paper ‘Conversion from constant flow system to variable flow’ provides further guidance, covering the best ways of upgrading for air-conditioning systems (including those incorporating fan-coil units), radiators and primary pumping. It also includes additional ideas for bypass control. It is available by emailing LSullivan@armlink.com.
Wayne Rose is marketing director of Armstrong.
www.armstrongintegrated.com
