Usable controls for BMS
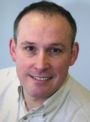
How can you control a building if you cannot work out what the controls are meant to do? Roderic Bunn has lots of experience of controls being the weak link in the chain of controlling building systems.
Why provide controls that people cannot use? It seems obvious that building-control systems should be straightforward to operate. Why, then, do we persist in providing controls that challenge and confuse? What possible benefit can there be in providing a controller that people struggle to understand? Are controls providers wilfully mystifying what should be simple, and creating a dependency culture to force long-term maintenance and support contracts onto defenceless building owners?
Such conclusions may be the product of an overactive conspiracy thyroid, but one cannot help but wonder whether poorly designed controls are, indeed, all part of a grand plan to divide and rule.
As a building evaluator for the Technology Trust’s £8 million Building Performance Evaluation programme, and also having been involved with the Carbon Trust's Low Carbon Building Performance (LCBP) programme, I have many opportunities to see the latest low-energy technologies in action — and the controls systems that operate them.
One is forced to say that, by and large, controls are still a weak link — both in the chain of procurement and also in the chain of building system control.
Taking procurement first, it is still unusual that control specialists are appointed early enough to enter into a meaningful dialogue with the client about their specific requirements. Specifications are low on detail about end-user expectations, and the closest many clients get to understanding controls is setting aside a massive proportion of the budget for a magic wand called a building energy management system (BEMS). They do not get involved in the detail. In fact, many consultants do not get involved in the detail either, leaving controls schedules to the contractor, who, in turn, outsources the responsibility to the controls supplier.
Second, many sub-systems come with proprietary controls. Ground-source heat pumps, wind-assisted ventilation devices, and motorised window systems come shrink-wrapped with their own controls. These packages are often procured separately by the M&E contractor a long time after the client has signed off the briefing documentation and agreed the specification. No-one ever questions the controls interfaces.
These systems usually come with their one-size-fits-all, vanilla-flavoured, end-user controls. Doubtless the specialists know how their controls work, but that does not mean they are intuitively obvious to ordinary building occupants. Such controls — particularly user controls — lack clear annotation, use symbols that are confusing, are located away from the devices they are supposed to control and rarely give any indication of their status. People become alienated rather than informed. They have the feature all right — but not the functionality.
Some controls, particularly those imported from abroad, such as ground-source heat pumps or solar thermal packages, come with instructions poorly translated from German and Swedish. This just adds to the confusion. Faced with labels or notation in a foreign language, facilities managers will tend to leave the systems alone.
Third, the commissioning, training and familiarisation of all building services occurs late in the contract. As a consequence it is often seen as something to be traded-off against more urgent work. Time scales are often compressed when sub-contracts over-run.
The same is true of commissioning — still the Cinderella of building services. Commissioning is compressed, hurried and often done very poorly. Rarely is an independent commissioning engineer appointed to oversee the commissioning on behalf of the client, despite evidence that this offers the best chance of the client getting a fully commissioned building at handover. Amazingly, given greater technical complexity being piled into the latest breed of low-carbon buildings, The management of commissioning management is still seen as an avoidable cost rather than a necessary investment. Commissioning plans are not considered early enough (if at all) and usually left to late in the project. Training for end-users on systems and their dedicated controls is often an afterthought.
Finally, customer support after handover, while planned with good intentions, often never occurs. The client is in a hurry to take occupation, and the build team is in a hurry to get paid and leave site. This does not bode well for systems to be set up properly. Occupants are left untrained and unfamiliar with the controls they have inherited. In any case, once practical completion has been achieved the project team begins to disband, and the focus shifts to defect resolution rather than system fine-tuning.
BSRIA's post-occupancy evaluations of buildings regularly find controls settings at the commissioned values set two years earlier, with no subsequent optimisation or fine-tuning to match patterns of use. This seems to be a particular problem with systems that come packaged with dedicated controls. BSRIA finds controls systems that are not only opaque to the premises manager and end-users, but also to the consulting engineer, who may have had no authority over their purchase.
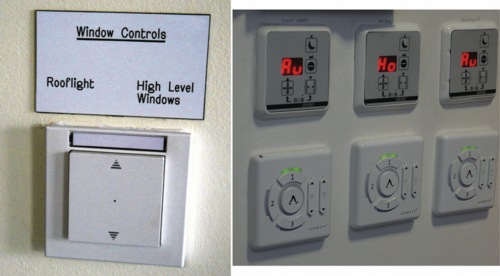
Small wonder then, that buildings are failing to meet their expected levels of performance. BSRIA regularly finds energy consumption three times higher than the design target and in some extreme cases five times the design estimation. Much of this excess is due to plant running wastefully, and the wasteful running itself is often down to poor control and poorly set up controls systems.
So what is to be done?
First, controls systems need to be brought much further forward into the briefing and design stage, and specifications need to be much clearer about the level and type of controls required for separate systems. Generic controls that come packaged with sub-systems deserve just as much attention as the bespoke BEMS — sometimes more. One cannot assume that a manufacturer’s grasp of what constitutes an intuitive, useable and programmable controller will match the understanding of the building’s occupants.
Second, where the occupiers are known, their facilities managers and user representatives should be involved in reviewing the proposals and commenting not just on the design intent, but also on the details of the management and user interfaces, including the equipment and its location.
Third, adequately trained operation and maintenance staff must be in place well before handover, and the training must include familiarisation with the controls. This must be done in good time — not at the last minute. Occupants will be happier to take ownership of systems when they are comfortable with the design concepts, understand their role in the control of the systems, and have commented on interface development. The latter rarely happens, but it absolutely crucial for people to understand what the controls do.
Despite training and familiarisation, it will still be important for a building-user guide to be written to help people understand the design intention so as to be able to use the building and its controls effectively. This guidance should complement the operating and maintenance manuals.
Finally, in the Soft Landings view of the world, project teams should follow through after handover to present key information on how the building’s controls are supposed to operate, introduce the guide for occupants, and be available in the critical weeks following occupation to answer queries from the building occupants.
And don’t forget, that the performance of a £50 000 building-services system can often be a function of a £1 wall-mounted controller. Controls may be tiny, but they are not trivial. Building designers need to spend far more attention on product choice, installation and fine-tuning. You cannot afford to treat them as fit-and-forget.
Roderic Bunn is a principal consultant in building performance analysis at BSRIA. He manages the Soft Landings initiative at BSRIA and is a Building Performance Evaluator for the Technology Strategy Board. He was co-author of ‘Controls for end users: a guide for good design and implementation’.
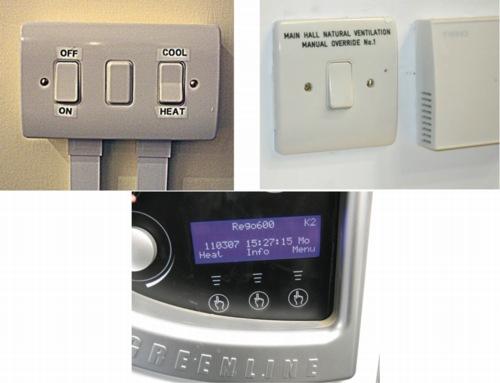