What if we bought everything in reverse order
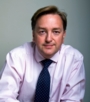
John Nicholls wonders if we would get better buildings more cheaply if the construction process were reversed — right down to the facilities-management contract. Would there be more emphasis on reducing unnecessary work and improving efficiency — rather than removing everybody’s margin?
During a recent meeting of eminent minds at the Building Controls & Industry Association (BCIA), discussions turned towards ensuring customers were handed the building they wished for. Surely end users would be overjoyed with an energy-efficient building that has a miniscule carbon footprint and a facilities-management budget smaller than a tank of petrol. Prompted by these discussions, I sketched out the following thoughts, written in the interest of debate, simply to promote debate and lateral thinking.
One of the main complaints of the building management systems (BMS) industry, over the last 20 years at least, is that BMS manufacturers and systems specialists are not involved early enough in the project to help maximise the technology design to be installed. Making sure the end user gets value for money, rather than a cheap and cheerful solution that is neither man enough for the job or tailored for the building. In previous times, this was the case. However, much of the influencing has now been reduced to just getting named in a specification that is a copy of a tome created 10 years ago. Shame on us.
Many years ago, influencing technology design was normal industry practice. I perceive there was more importance given to the endgame when it came to creating a building and the technologies that would be installed within. Perhaps investors had more money to spend then and were able to afford what they wanted. The BMS would work in perfect harmony with the mechanical plant it was asked to control. The fact remains, however, that the BMS can yell as much as it likes at the plant room, but the air and the water systems can only deliver what they have been designed to produce.
Then capitalist forces took over and in many cases during the construction process tomorrow’s problem is left to tomorrow’s people. On budget and on time takes precedent over ‘cheap to run’.
So bear with me on this one, shake off the fact that you were once an engineer, shake off those old notes from the blue-sky seminar you went to and here goes. What if the whole construction cycle was procured backwards or the order in which packages were let was reversed? I know this is not your average MBS article, but it makes a change from more updates on CRC legislation.
Firstly, the facilities-management package would be let, with a specification written around the building performance and life-cycle costs. Next would come the decision regarding technology and what control systems — such as the BMS, lighting, variable-speed drives and security — would be used.
Selection of the specialist installers would follow those who have been informed of the previously selected technology, and they would have to find the best installation solution for the building. The mechanical and electrical contractors would come next. This would be far removed from the practice of design and build. Effectively contractors would be pricing on how efficiently they can manage the construction process rather than how brutal or economical their purchasing department can be.
Finally, the builder. How bizarre would it be if a selection of main contractors were asked to price for a building that had practically been fully designed and all the players in place? By this time, there would be a tremendous amount of schedules and rates available. Perhaps, if nothing else, the risk is further reduced for those currently at the top of the tree.
The exception to the above process would be the architect and the design consultant. During the good old days they would be employed at the start of the contract and would have full design responsibility.
Winners and losers
The specialist and the technical teams in the construction cycle would be happy. At last they can influence the design to install the right solutions — all before it is too late. This is a situation much sought after and which often only occurs when all the construction players have left site, leaving the specialists and the end user holding the baby — albeit a baby that arrived late, came extremely cheaply, but shouted and swore for the entire duration of the delivery process.
On the flip side of the coin, the higher up the food chain you are, the more you dislike this situation. I have been told by a number of M&E contractors that part of their job is to protect the investor from specialists like me, who want to gild the lily with unnecessary gadgets and technologies that the building does not need. The M&E and main contractors would have little room to manoeuvre in the traditional manner. They are being given a done deal. Their ability to redesign, barter and ‘value engineer’ becomes non-existent.
In short, and trying to speak as a neutral individual, the building would cost more to build but possibly less to run. Putting my optimistic hat on, I could submit that this need not be the case. I suggest that less time would be spent organising Dutch auctions from the top to the bottom of the chain, because no-one is currently immune. More priority would be placed against focusing on the process of reducing unnecessary work and improving efficiency, rather than removing everybody’s margin.
With a recession currently biting into profits like a northerly wind, I think short-term capitalism will be the front runner for the foreseeable future. Meanwhile, I’ll put my blue-sky seminar notes back in the attic and return to quoting against the points schedule I’ve been given. Food for thought.
John Nicholls is a director with BG Controls