Planned comfort

The worst time to find someone to repair a boiler is when something goes wrong — unless you have a maintenance plan, in which case breakdowns are far less likely. Peter Gammon takes a look at why maintenance and service contracts can be a saving grace.
Insurance plans are bolted onto numerous purchases these days, from mobile phones to vacuum cleaners. However, if after five years you haven’t had a problem, the question arises of why you paid for the plan in the first place. Or further down the line something goes wrong and you delve into your files and pray that the extended warranty is still valid. Either way, having the peace of mind that problems are covered makes life far easier, especially if it’s in the depths of Winter and your boiler plant isn’t firing up.
Although the quality of boiler construction is incredibly high these days, there are some occasions when even the newest units can break down. Everyday, thousands of commercial buildings rely on boilers to maintain their hot water and central heating, meaning, potentially, problems could be costly and substantial. What might be an inconvenience for the average household is an operational disaster for a hospital, nursing home, hotel or school. With potentially hundreds of people affected, it is vital safeguards are in place — as well as the ability to fix the problem fast.
Boiler service plans are perfect for spotting early signs that a problem might be looming; it could be discolouration of the heat exchanger indicating a possible leak or a build-up of scale reducing heat transfer. Discovering such problems in good time will reduce the potential cost and added inconvenience of a breakdown. Keeping a boiler running efficiently can significantly reduce its running costs and ensure value for money over its lifetime — a very sound reason for boiler maintenance.
Of course, saving money should always be secondary to safety. Not even the most Scrooge-like wants to compromise the lives of others. Although modern boilers are far safer now than ever before, a planned service by a trained engineer can catch most problems early.
So how much can a breakdown cost? In commercial buildings the bill can be large, not only in remedial repairs but the potential ramifications for the building’s occupants. A hotel is a good example where a boiler failure on a Sunday morning can cause thousands of pounds in lost revenue as waves of disgruntled guests expecting a relaxing hot bath seek compensation. But the cost to a business is not always financial. In a hospital or nursing home, lack of heating or hot water for patients or residents can cause serious health and operational issues. And the Office of National Statistics estimating that 25 400 extra deaths are caused as a direct result of cold conditions in Winter highlights the need to maintain a continuity of heating supply for vulnerable people.
The outlay for remedial repairs of commercial boiler systems can also be incredibly high. According to my colleague Richard Layzell, our service office manager, replacing a heat exchanger in a commercial boiler can be as much as £3500 and to replace the brains of the boiler, the controller, could be £400. And this doesn’t factor in labour costs or call-out charges, which can ramp up the overall bill. Planned boiler maintenance gives the building or facilities manager the assurance that when a spare part is required, the plan can provide it and cover the cost. Plus it will allow breakdowns to be repaired quickly and downtime minimised. At MHS, for example, all our trained engineers have access to an online database of spares, enabling them to complete any maintenance safe in the knowledge they have everything close at hand or at worst, available for overnight delivery.
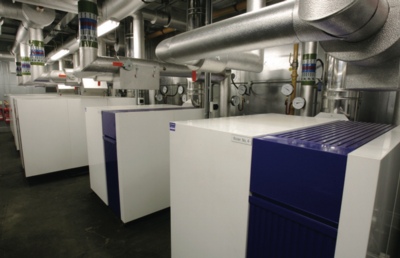
As any financial controller will tell you, running a successful business relies on effective forward planning, and an unexpected expense can ruin a profit-and-loss statement. So where commercial boiler plant is concerned, budgeting for an annual maintenance contract allows the costs to be spread over a 12 month period — making outgoings more predictable. And with more commercial properties moving towards multi-boiler cascade systems, service down-time due to maintenance can be less of a consideration. If one boiler is being worked on, the others in the cascade are able to continue to operate providing at least partial service.
But what options are available? Some companies offer ‘off-the-peg’ plans that may not suit the individual requirements of the business. However, all customers’ needs are different and it is much better to create specific plans tailored to suit individual requirements. Whether it is a plan covering two, five or 10 years, there is flexibility in how a business approaches its maintenance.
As energy prices show little sign of falling, it makes good economic sense to ensure that your commercial plant is running efficiently. After all, small changes in the way commercial boilers are run can make significant savings in fuel bills. And for most facility managers, businesses and accountants, having the reassurance that the boiler is running efficiently and can be fixed quickly provides a welcome peace of mind.
Peter Gammon is technical manager with MHS Boilers.
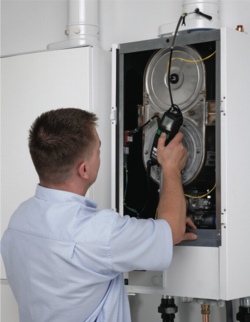