Delivering the benefits of variable-flow systems
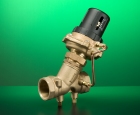
In delivering the energy-saving and operational benefits of variable-flow heating and chilled-water systems, differential-pressure control valves have a key role to play. Andy Lucas of Crane Building Services & Utilities takes up the story.
To get the highest efficiency from a design, a new car for instance, manufacturers consider the individual components and, more importantly, how those individual components work as an assembly — for it is the efficiency of the finished assembly that really matters.
The same is, of course, true of heating and chilled-water installations.
No matter how good the individual components (boilers, pumps, valves etc.) may be, if they are not selected, installed or commissioned correctly all the ‘claimed’ efficiencies are lost. Each individual component is dependent on the others to allow it to function correctly.
The change in the design of water-distribution systems from constant volume to variable volume allows the possibility of reducing the amount of energy input into the system.
Variable-volume systems are designed to match heat output to the actual demand of the building in real time. As room thermostats indicate a requirement in a particular zone, the BMS drives the actuators on control valves to open or close accordingly. As the control valves open or close, the flow rate will vary, allowing the pump to change speed to satisfy the new demand. As well as the variation of pump speed, the total heat requirement also changes, which affects the quantity of water produced by the boilers/chillers.
If we solely consider the pumps, which typically use about 6% of the energy input into the heating system, the energy saving can be easily understood. A flow reduction to 50% of design flow rate gives a corresponding heat output of about 80%, with a pump power requirement of about 12.5% of the energy requirement at design flow rate.
Perfectly alright in theory, but in practice as pump speed changes the pump efficiency may also change, negating some of the savings; but in practice we know reduced pump speeds save energy.
The role of the differential-pressure control valve (DPCV) is now fairly well understood.
1. To re-create stable differential pressures for the control valve to operate.
2. To make each circuit ‘protected’ by a DPCV independent.
Variable-volume system design creates the problem of pressure variations in the distribution pipework. The use of DPCVs re-creates stable zones (branches/sub-branches) that are characteristic of constant-volume systems and therefore allows balanced, accurate control over the flow rate by the 2-port control valves. Without this stability, the capability of the BMS, via the control valve, to control the heat output of the terminal units is compromised.
As we know, modulating 2-port control valves are designed to establish a direct relationship between heat output and the control-valve open position.
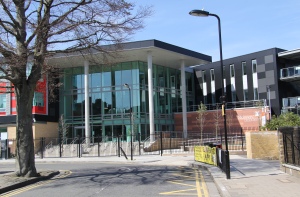
Modulating 2-port control valves are designed to operate with a characteristic known as equal percentage modified (EQM); the shape of the control valve disk is designed to establish a relationship between the required heat output and how far the valve is open.
To maintain this relationship, the differential pressure across the control valve must be constant. Variations in differential pressure will cause uncontrolled changes in flow rate — hence the introduction of the DPCV to eliminate these variations.
Having understood the requirement for controlling the differential pressure and the consequence of not controlling it, we must of course ensure that the selected DPCV is correctly sized. As with all control valves the pressure drop across the DPCV is relative to its ability to control the flow rate. Too large a DPCV will have a low differential pressure across it whereas too small a DPCV will have a high differential pressure across it. Although a high pressure drop across the DPCV gives a high level of control over the flow rate, it also requires a higher input of energy into the pump.
By sizing the DPCV correctly, a system designed to be variable volume can achieve high levels of pump energy saving. A recent example is Skinners’ Academy in Hackney, London, a co-educational comprehensive school using 25 Crane DPCVs.
Having looked at the possible energy savings for the building occupant, we should also consider the advantages for the commissioning process.
Without DPCVs fitted, the entire system installation needs to be completed before the balancing process can start. This can delay project completion, as problems can only be identified at the point where the contractor wants to achieve handover.
In addition, any future changes to the system will also result in the need for the whole system to be re-balanced. The advent of ‘seasonal/continuous’ commissioning (see the BSRIA publication BG 44/2013) may also result in changes to the system balance.
The installation of DPCVs at strategic positions around the system divides the complete system into smaller manageable stable zones, which are independent of other zones.
Each zone can now be balanced to ensure correct flow rates to its terminal units. Once the DPCV is set, changes made in other zones have no effect on the balanced zones; they are ‘protected’ by the DPCV from pressure changes in the distribution pipework. This allows the commissioning engineer to balance the protected zones in any order, as once balanced they stay balanced. Project programmes can be accelerated as each zone is commissioned separately.
Talking early to manufacturers in the product-selection process (whether for pumps, boilers or valves) helps ensure high levels of installed system efficiency and reduces installation problems. Talk to the experts.
Andy Lucas is technical development with Crane Building Services & Utilities.