Managing the change to new boiler technology
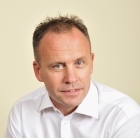
Managing the shift from old-style atmospheric boilers to modern condensing boilers presents opportunities and challenges. Stuart Turner of Hamworthy Heating shares his experience.
With the refurbishment of heating and hot-water plant we are seeing a shift from traditional atmospheric boilers and water heaters to modern condensing models. When embarking on this type of project it is vital to assess the current system along with the proposed new scheme to gain the maximum benefit from these products and make the best possible use of the existing system — including pipework and flue runs. This will ensure an ease of transition from old to new plant with minimal downtime — a crucial factor in commercial buildings that cannot afford to be without heating or hot water for a long period of time.
Taking an holistic approach from the outset of a project gives you the ability to obtain an objective view — whether it be for space heating, hot-water supply or heating and hot-water services. It is important to understand the client’s philosophy and justification for their approach to identify early on any aspirations for building excellence such as BREEAM ratings or particular performance criteria.
In existing buildings it is beneficial to undertake a thorough plant-room survey to identify factors that, if ignored, will be to the detriment of the project outcome. This survey can ultimately save substantial time and cost later in the project.
However, this must not be explored in isolation, but extended to review the building and entire system. Has the building had a change of use or occupancy that may affect the demand, or is the system old and dirty so that it will require specific water treatment prior to any equipment being installed. Are there measures that have been, or could be, put in place for increased efficiency and reduced wastage such as splitting the system into zones, installing external temperature sensors for weather compensation and thermostatic valves on some of the radiators?
There are many factors to consider, which will vary on each project, so there is no one solution that will suit all applications.
It’s crucial to recognise early on the type and condition of the existing flue system and its route, as many boiler refurbishment projects today will require the flue system to be upgraded or replaced — particularly if you are not replacing like for like.
Updates to the Building Regulations Part L and European directives such as the Energy Related Products Directive are driving the change from atmospheric or pressure-jet boilers and water heaters to condensing or high-efficiency models to comply with the outlined efficiencies.
However, the existing flues on this type of system are not able to deal with a modern pressurised and wet system where condensate will form.
Flues for atmospheric appliances will be larger to create a low resistance system, allowing the natural draught to pull flue gases through the system.
Modern boilers use a fan to push flue gases through the appliance, creating a positive pressure at the flue outlet, allowing smaller flue diameters, but also typically run at lower flue-gas temperatures, with the likelihood of condensate forming within the flue.
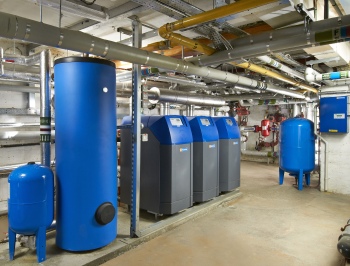
The flue system must be water tight and pressure tight, and designed to drain the condensate from the flue and prevent flow back into the boiler. You may be able to make use of the existing chimney with a liner to enable it to cope with condensing operation and also to keep installation costs down.
Provision must also be made to remove condensate safely from the boiler itself. A 100 kW boiler will generate around 13 l/h of condensate. The condensate is typically 3.5 pH, which is slightly acidic but can be disposed of normally through the drainage system. If the boiler or water heater is not next to a suitable outlet, the condensate trap/drain must be connected to a drainage system using corrosion-resistant material. It may be beneficial to install a condensate pump to assist with effective removal, particularly important in basement plant rooms.
Modern boilers with low water content are less tolerant to fluctuating flow conditions in the heating circuit, so a low loss header is recommended to safeguard the condensing boilers from low-flow conditions on the secondary circuit, which may be caused by a pump being shut off or a motorised mixing valve changing position. A low-loss header ensures that a steady flow of water is maintained through the boilers, protecting them from potential damage as a result of firing when there is insufficient or no water flow.
Only part of the benefit of a boiler or water-heater upgrade can be realised unless a review and improvement to the control system is implemented.
It is vital to identify the existing control regime, control features and functionality. Also, find out if and where temperature sensors are fitted. For multiple-boiler installations a good boiler sequencer, such as Hamworthy's Merley controller, will help maximise the benefits of the new boiler plant. Older atmospheric boilers only operated on/off or high/low, compared to the fully modulating operation of condensing boilers, so it is unlikely the previous controls will be sophisticated enough to implement effective sequencing strategies.
The accompanying photographs show the result of a best-practice plant-room refurbishment. With a thorough site survey and objective review of the existing heating and hot-water system the number of boilers was reduced from eight atmospheric to three condensing boilers, creating more space in the plant room for servicing and maintenance. An air and dirt separator and dosing pot was installed to clean and protect the system. Two condensing water heaters with top-to-bottom recirculation kits achieve highly efficient hot-water generation.
Ultimately a project to refurbish heating and hot-water plant should always be viewed in the wider context — not just the boilers and water heaters in isolation. This approach will ensure that a best-practice solution is achieved and the customer gets best value for money, and high-efficiency compliant products with full system integration.
Stuart Turner is southern regional sales manager with Hamworthy Heating.
