How Monodraught utilised 3D printing to develop Cool-Phase
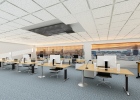
James McGowan of Monodraught discusses the development of Cool-Phase, the company’s latest innovative application of phase-change material as a thermal energy store to actively ventilate and cool buildings.
Winning the prestigious 2013 Impax Ashden Award for Energy Innovation for our Cool-Phase natural-cooling system was a real boost for everyone at Monodraught because the whole company has been involved in its development over the past few years. Designing and manufacturing sustainable products that reduce energy consumption is a worthwhile objective for any company, and staff at Monodraught relish it as a long-term mission. Nowhere is the challenge greater than in the R&D department.
The application of phase-change material (PCM) reflects the ethos of the Monodraught team to apply the most advanced concepts of modern science and technology to create ground-breaking and innovative products.
When the redesign of our Cool-Phase system was first discussed we wanted to involve the entire company. We had separate meetings with each department in the business to get every perspective possible. We began by exploring new design techniques that would enable us to speed up the design process. As we focus heavily on R&D within Monodraught and already use a lot of 3D modelling within the R&D department, we decided to complement it with the very latest 3D printing technology. 3D printing gave us the ability to bypass the traditional ‘prototype’ lead times from our suppliers.
Rather than waiting several weeks for component samples or fabrications, we were able to 3D print the designs ourselves within hours — either to scale or full size. This allowed us to use a physical component rather than the usual computer renders to review designs. Design issues were identified quickly and iterations of designs evolved through the speed of the 3D printing process.
Another benefit of the 3D printing technology was a rotating mechanism in the Cool-Phase air-handling unit being redesigned and operational in our test centre just days after the drawings left the design office, simply because we didn’t have to fabricate the parts.
Early in the development process we printed a modular design for a thermal battery component for Cool-Phase. The battery component was separated into three modules, each comprising six components, using just three reversible symmetrical parts. Using 3D printing, we were able to prove the design concept.
These experiences with 3D modelling and printing and the modular approach to component design and production have helped to reduce our component count by around 70%, which also reduces the assembly time. The modular design concept streamlined our installation process, enabling us to now install a Cool-Phase system in a third of the time.
Monodraught also uses computational fluid dynamics (CFD) for the in-house testing of products, because part of the challenge of working with new technologies is justifying them and ensuring that we can answer any questions our customers may ask.
As a result we have worked very hard on the airflow of the system, where one of the challenges we face with Cool-Phase is meeting stringent Building Regulations. One of the weaknesses specifiers have identified in many of today’s air-handling units is a general inefficiency in airflow components, which are often fabricated from sheet metal with 90° angles that are not efficient in terms of air movement and system energy use. The combination of 3D modelling, CFD and the injection moulding processes we are using to manufacture Cool-Phase has enabled us to very accurately design the geometry of our airflow components.
We could therefore design complex sweeps that optimise the flow of air, creating a far more capable system that is as effective and efficient as possible. As a result of our work, the Cool-Phase fan uses far less power, which means it is also operates much more quietly and is a more energy-efficient system. Both are benefits we could not have achieved without the technologies we are now employing.
Even more impressive, and something that has surpassed the expectations of everyone involved in the development, is the fan’s power usage during typical daytime operation ranging between 7 and 20 W — so low that customers we initially spoke to just didn’t believe it! However, we do have the data to prove it. We are, of course, delighted that it is so low and represents such high energy efficiency compared to alternative ventilation and cooling strategies.
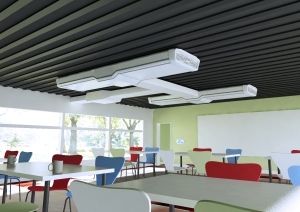
Aesthetics was a noticeable development item, mainly due to the batch-manufactured sheet metal used previously not lending itself to aesthetically pleasing design. We set ourselves a target to improve the looks; during discussions the evolution in design of the WALL-E and the Robot Eve characters in the Disney movie ‘WALL-E’ became a talking point.
The evolution of the design of Cool-Phase can be compared to the contrast between the very heavily manufactured, mechanical design that is Wall-E and the seamless Apple look that is very Eve. Whilst the sleek, smooth and contemporary ‘Eve’ look has been partly achieved by reducing the depth of the unit, this had implications for the size of system’s ductwork, the airflow going through it and the air paths. However, by adopting new manufacturing techniques we achieved all these objectives and created a very slimline design. This slimline look was discussed as a possible ‘optional’ system in the Cool-Phase development programme but is now no longer required as the model is just 350 mm deep, which reduces the building void space required to install it to just 400 mm.
Almost every component in the Cool-Phase system has been 3D modelled at some stage. At one end of the scale we downloaded 3D files from fastener manufacturers to assess how their products would integrate with ours, and at the other end we 3D printed the entire Cool-Phase unit as a 20:1 scale model part way through development, to preview the design.
Predictably, this means that our sales and technical staff want scale models to help them present Cool-Phase to potential customers, architects and consultants.
Monodraught has always been dedicated to creating new technologies and innovative products that enable the HVAC and building services sectors to provide more sustainable buildings for the future and replace the traditional, inefficient technologies currently available. And whilst initially, components created with 3D print technology were used to speed up development, it is rewarding to discover that many of those same components have also improved efficiency and reduced energy consumption to a point where our new Cool-Phase system can maintain temperatures within the comfort zone while reducing energy consumption by up to 90% compared to conventional cooling systems.
In our drive to develop new and innovative products, we are also applying new and innovative technologies that have been developed, often for applications far removed from our own industry. The decision to apply 3D modelling and printing in the development of our new Cool-Phase system has put us in the fortunate position that we are well ahead of our manufacturers and are now examining ways to maintain acceptable lead times.
To quote the Ashden awards judging panel: ‘This [Monodraught] is a business that has built up a reputation for its long-term commitment to sustainable buildings in the UK. It is no exaggeration to say this [Cool-Phase] could potentially change the whole ventilation and cooling market.’
As John Curley, business manager for Cool-Phase, believes that the business support Monodraught receives from winning this prestigious award will enable the company to access a global platform on which to build its profile for low-energy cooling and ventilation solutions.
James McGowan is R&D product designer for Monodraught.