Rising energy prices spur maintenance activity
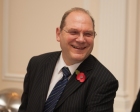
In the last 10 years, energy prices have has risen by 140% and gas by 240%*. With prices still soaring, energy reduction in building operations is on the agenda of many. Alan Juggins of Cavendish Maintenance, explains how the rise in energy prices is changing the landscape of building maintenance.
Whilst the industry has somewhat changed since I started as an electrical technician in 1972, the maintenance industry is still big business in the UK. According to the Association of Electrical & Mechanical Trades, there are over 200 known maintenance companies in over 330 international locations. The development of the industry has come from the change in maintenance contracts in general.
Our experience has been that maintenance contracts are now split into various areas. For example, you have the base build, which incorporates the plant machinery, and then the demise contracts. The contracts are very different in their approaches, and my experience is that the success of both contracts lies with a good soft landing.
The journey could be bumpy!
According to BSRIA, Soft Landings is a process for designers and constructors to improve the operational performance of buildings and provide valuable feedback to project teams. It is a Government initiative for all new buildings to adopt the Soft Landings approach by 2016. Unfortunately Cavendish’s experience has been that, whilst it is great in principle, it only considers buildings that are at conceptual stage. This means that many of the buildings that are about to be completed haven’t considered Soft Landings, making it a somewhat bumpy, if not firm, landing for all parties.
Even when you are taking on a new maintenance contract with an incumbent, this same principle should apply. Upfront planning and handover will ensure that you have reliable plant.
The aviation approach
Good maintenance should be good value for money and cost effective. Being from a client background, I understand that budgets are always a constraint, so there needs to be a smarter way of providing a level of maintenance which creates savings via energy usage, thus giving a more efficient building.
I, and managing director Steve Allen, have used the same principles as the aviation industry, where, just like pilots, one creates a check list before take off. This check list is used as the core base of maintenance, ensuring that you have no malfunctions or, as we like to call it, ‘no mid-flight problems’. By carrying out vital checks, you can ensure that all plant equipment is running as it should be before occupation. This process is also used on a daily basis, and it is here that we can start to see patterns on where energy can be reduced, creating a more efficient building.
I think that maintenance should be like visiting a 5 star hotel — everything seamless and like a home away from home. You only get to see the front-of-house staff, never the back-of-house staff. This ultimately means incorporating non-intrusive maintenance. Today’s occupier isn’t interested in how the building works, just that it is going to be comfortable when he/she arrives at his/her desk in the morning.
Switching on to switching off!
According to an article by energy-comparison site ‘U Switch’, energy prices have risen by 151% since 2004, making it an average rise of £800 in most households. Large corporates are seeing this problem 10-fold, where they are battling to reduce their energy consumption whilst the price per unit rises. Older buildings have even more of a challenge because they lack thermal insulation, meaning that a large proportion of their energy bill is used on heating the building. Even 1950s buildings only had 50 mm of insulation, because energy was so cheap.
The building-services and maintenance provider can help to reduce the energy output by investing time and capital in lower-energy products and upgrading plant machinery.
For example, there have been some fantastic developments in lighting during the last five years. Lighting can be equate to as much as 40% of a building’s energy budget. Swapping the current lighting system for one that uses less energy can make a big difference on the bottom line.
![]() |
With budgets always being a constraint, there needs to be a smarter way of providing a level of maintenance that creates savings via energy usage, thus giving a more efficient building. |
When I was working as a client for a large aerospace manufacturer, we found that swapping sodium mercury vapour and fluorescents in clean rooms to the new LED lights gave the biggest savings. We aimed for 1000 lx and we saved two-thirds of the previous year’s energy spent on lighting.
The LED lighting gave 2-fold saving. The first was a 50 000 h lamp life instead of the standard 10 000 h. Secondly, due to the ceiling height, we didn’t need to stop production and arrange access, meaning less downtime and less maintenance required.
Large plant machinery such as chillers and CHP units are also being improved all the time. It is important that maintenance teams evaluate plant machinery and produce a predicted failure schedule for the buildings’ machinery. Cavendish installed two 800 kW Turbocor chillers at British Land’s Euston Road premises, which achieved major energy savings. The modified control system allowed the smart use of the new chillers — with the older chillers being retained as back-up — and N+1 is automatically controlled. Modern chillers are estimated to be at least three times more efficient than older models, as they adjust outputs to match the load required.
Newer technologies have come with problems. The lack of knowledge stems to both clients and technicians. There isn’t the number of technicians coming through that can maintain the new equipment, meaning that older technicians are having to re-train and learn new techniques to keep up with the changing technology.
My feeling is that the key to maintenance is non-intrusive maintenance. New pumps today, for example, can share data to the BMS, meaning that the standard technician’s role will change.
I am sure that as technology changes, we will see more savings from non-intrusive and smart monitoring, helping the ever-increasing challenge of rising energy prices.
Alan Juggins is operational manager for Cavendish Maintenance