Going with the flow
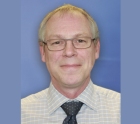
Increased use of variable-flow systems is creating new challenges in control valve design and specification. Bjorn Sejr Nielsen of Danfoss, explains the importance of provable product performance and the role of pressure-independent control valves (PICVs) in achieving the desired flow control.
In the 10 years since Danfoss developed the concept, the PICV has become a mainstay of the UK control valve market, with millions installed in thousands of projects. That’s not to say that PICVs are universally used on all new projects. Traditional control-valve designs are still being created, and there are geographical variations in use across the UK.
However, with the trend towards variable-flow systems new concerns are emerging for specifiers, designers and end users — primarily about the performance of products in the following key areas.
• Achieving desired flow rate.
• Performance in partial load when under the influence of the control system.
• Operation at ultra-low flow conditions.
These three areas represent the main differences between a PICV system, which works in near-perfect performance conditions, and a system which is slightly or no better than a traditional control-valve design. With a few simple checks, specifiers can ensure they get the ‘best-of-the-best’ system design, rather than a ‘better-than-the-old method’ system. So let’s look in more detail at potential PICV performance in relation to these three areas.
First, achieving the desired flow. A PICV is a flow-control valve which uses a differential-pressure-control cartridge to control the pressure across the control valve, to ensure the design flow regardless of the pressure put onto the valve. This means it is designed to deliver a set flow. Achieving the exact design flow, ±0%, using current methods is impossible. Even if the valve always delivered this flow, the measurement equipment used in systems wouldn’t be able to measure the flow with such accuracy.
So the question is, what tolerance can be allowed in good system design? Well, this depends on specific system design and requirements. For example, a valve which delivers low flow may not be able to deliver the required heating or cooling duty of the system in conditions where maximum capacity is required. Alternatively, a valve which delivers flow above the requirements of the system will ‘overflow’ the coils and deliver poor control and energy efficiency.
So it is extremely important that the PICV delivers the required flow within a reasonable range. This range will depend on the specific needs of the project, but the good news is that your PICV supplier should be able to prove performance at time of specification. BSRIA test standard ‘BTS 1/2012 Test method for pressure independent control valves’ is a standard which sets parameters for PICV manufacturers to test their products to a variety of performance measures, including delivering the required flow. This will assist specification by demonstrating how different valve sizes and different flow settings perform in delivering the required flow. The more accurate, the better performance.
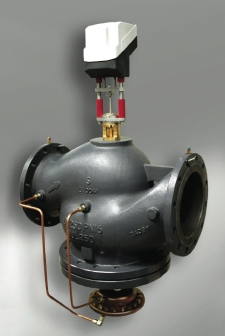
The second key performance area when selecting PICVs is how they perform when under the influence of the control system. This is primarily a question of control-valve authority. In theory, a PICV should be full authority and fully modulating. This is impossible in traditional control-valve systems and is one of the key reasons for the increased use of PICVs over the past 10 years. However, the ‘full-stroke’ design of some PICVs means that authority will be reduced at some flow settings and when delivering low flows. So valve design is important to achieving better control.
The outcome of a full authority is achieving the desired room temperature and reducing the instances of ‘hunting’ in the system. Hunting is where the control valve is incapable of achieving the desired room temperature due to poor control. The valve operates with low authority ‘on/off’ and over delivers flow when opened. The result is that the room temperature is constantly fluctuating.
Proving PICV performance when under the influence of the control system is another component of the BSRIA test standard. Manufacturers should, therefore, be able to provide information to prove the performance of their products prior to specification and purchase.
Finally, operation at ultra-low flow conditions. 10 years ago the key application that prompted a move to PICVs was fan-coil and terminal units, and this remains the majority application for the product. The specific challenge created by this application is that low duties and high differential temperatures, especially on heating, have created a need for PICVs to work at extremely low flows.
Dealing with ultra-low flows is about ensuring the valve works to the required standard. First, the valve should be able to handle the flow within its published flow range. Secondly, proving this performance should become part of the technical submission made at specification stage. At Danfoss, we believe proving performance at these ultra-low flows is something specifiers should demand from manufacturers, as whilst control of 1 kW of heating duty may not seem important on a single fan coil, control of 100 kW of heating across 100 fan coils is important for energy efficiency and system performance.
Looking ahead, Danfoss believes the next phase of PICV specification should focus on optimisation of design and a demand for system performance. Although PICVs are widely recognised as the best solution to provide this performance, product and manufacturer selection is still critical to ensuring the system delivers what the designer has promised.
Bjorn Sejr Nielsen is marketing director with Danfoss.