Going the extra mile
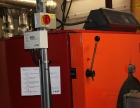
Following the Mayor of London’s announcement of further investment in retrofit energy-saving measures, Geoff Newman discusses what comes next in the boiler room when the obvious measures have been taken.
As the next heating season approaches many minds will be turning to the boiler plant: how much energy will it use through the colder months and what contribution will it make to the organisation’s carbon emissions?
Such concerns about energy consumption and environmental impact have led many organisations to implement relatively quick and inexpensive ‘fixes’ to improve the efficiency of the boilers. Typically these initiatives might include optimising or upgrading the building management system (BMS), adjusting temperature settings and encouraging behavioural changes.
In parallel, though, there is sustained pressure to ‘go the extra mile’ and achieve further savings once these obvious ‘tweaks’ have been applied. The challenge for the building services engineer, therefore, is to identify additional opportunities for achieving significant savings within budgetary constraints.
In this respect, those projects that will deliver a fast payback for a relatively small investment of capital have particular appeal, as the savings achieved help to fund more ambitious, longer-term energy-saving projects such as those being delivered via Energy Performance Contracts. In many cases such projects will involve retrofitting additional technologies to enhance any energy-savings that are already being achieved.
Indeed, the benefit of such retrofit projects has recently been recognised by Mayor of London Boris Johnson, who has announced a further investment of £12 million to expand the current programme of retrofitting buildings across the capital. Retrofit initiatives are also being used widely by service providers with responsibility for reducing their clients’ energy consumption.
With respect to boiler plant the next obvious area to address is that of boiler dry cycling, something with which many MBS readers will already be familiar. What may not be quite so obvious is the fact that the energy-saving measures mentioned above will not typically identify or prevent boiler dry cycling. Yet tackling this phenomenon using patented M2G retrofit boiler load optimisation has the potential to reduce energy consumption by 12% to 15% across an estate – over and above those savings that have already been achieved.
Crucially, it is possible to prevent boiler dry cycling with a relatively low investment and a typical payback within two years, without conflicting with existing boiler control strategies or compromising comfort conditions within the building.
This is because M2G boiler load optimisation control works in a very different way to other methods. By monitoring each boiler every second the M2G is able to establish a profile of the load being placed on each boiler; it can identify immediately if the boiler is dry cycling to compensate for standing heat losses or if there is a genuine heating demand.
This continual adaptation to BMS/optimiser variable set points ensures the M2G complements existing controls without altering the boilers’ designed set points or the system temperature and therefore enables additional cost savings to be delivered.
Another important point, in terms of life cycle costs, is that M2G units are self-learning and require no maintenance or seasonal calibration and can be easily transferred to new boilers if existing plant is replaced.
The underlying reasons for boiler dry cycling and an explanation of how M2G prevents it are included in a new animation that can be viewed at the link below.