Solving the puzzle of the performance-gap
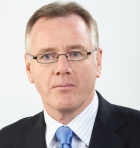
Clients are becoming increasingly frustrated by the building performance gap, but what can the commercial heating and hot water industry do about it, asks David Pepper of Lochinvar.
At the recent CIBSE ‘Leadership in Building Performance Conference’, clients’ frustration with the performance gap was clear to see. Louise Ellison, head of sustainability at the retail developer Hammerson, said it was puzzling that even some of the newest buildings were among the worst performers in terms of energy efficiency.
‘We need better data from the industry. You have the information; please share it with us so we know what we can expect and so that we don’t simply design just to comply with legislation,’ she told the conference.
She added that clients were becoming more energy aware and were now far more likely to ‘look under the bonnet’ to identify the long-term management risks posed by the buildings they buy.
The performance gap is also an expectation gap. Clients are not always clear about what they can expect from our industry, but they know that rising energy costs and buildings that perform poorly can have a direct impact on their profitability. In the absence of better information from us, they are bound to base procurement decisions on lowest common denominator legislative requirements or just to meet corporate social responsibility goals.
They, and we, can do better.
Delivering heating and hot water in an appropriate, reliable and cost-effective way is a key building-performance issue. The ability to closely match boilers and water heaters to predicted demand is an essential part of any modern energy-saving strategy. It is no longer acceptable to design for peak demand plus a generous margin for error because of the legacy of energy waste this builds into the system. However, we also have to cope with the vagaries of occupant behaviour.
Too many buildings continue to disappoint — and puzzle — their owners because they fail to meet the energy efficiency and comfort targets set when they were first designed. Much of this is down to poor design choices and the failings of the procurement process, but equally how systems are used and often allowed to ‘drift’ off course during a building’s lifetime can upset even the best laid plans.
Commercial heating designers and specifiers can play their part in narrowing the 'performance gap' that emerges over time by paying attention to the following points.
• Ensuring boilers and emitters are properly sized and commissioned;
• Ensuring that they can be closely controlled to adapt to changes in occupancy patterns and outside weather conditions
• Integrating them properly with the rest of the building systems.
Crucially, they must be easy to maintain and control and as flexible as possible to limit any long-term undermining of the design intent.
Manufacturers of boilers and water heaters are innovating to build as much flexibility as possible into their systems to more closely match the aspirations of clients. We are rarely afforded the luxury of a direct conversation with the client, so it can be hard to analyse exactly how the building is to be used, However, we should have enough flexibility built into our products to cope.
For example, the concept of modulating pre-mix burners has been used in gas-fired condensing boilers for several years. It is a tried-and-tested philosophy, and most, if not all, modern boilers have a turndown ratio of at least 4:1. The real user benefit is gained from multiple boiler installations with cascade controls which can greatly enhance operating efficiency.
A 3-boiler cascade installation, for example, provides 12:1 turndown. This modulation ensures that boilers will not repeatedly ‘cycle’, but that they will react smoothly and gradually to demand. This is good for operating efficiency and longevity, and is largely immune to changes in occupant behaviour, providing the installation and commissioning team are given the opportunity to set up the system properly.
There is much talk about ‘soft landings’ and enabling the project team to remain engaged with the client post-occupancy so we can return to tweak and fine tune, but experience shows that this is rarely possible. Many buildings ‘drift’ away from their original design intent because users reset controls — or even turn them off completely.
Maintenance programmes are usually reactive rather than strategic. However, despite that, on-board controls that constantly measure and monitor operating conditions will keep the equipment as close to optimal operating settings as possible.
In other words, we must deliver our own version of soft landings on a more targeted and pragmatic basis — and, therefore, more financially realistic, because, at the end of the day someone has to pay. By focusing on product specific flexibility managed by on-board controls, we can smooth out some of the occupant behaviour issues that can lead to buildings drifting off course.
Although the recession is (largely) behind us, cost cutting — dressed up as ‘value engineering’ — is still the norm and continues to be driven by end users. The industry is still failing to get the message across that decisions based purely on securing the lowest possible capital cost will lead to higher energy bills and inflated maintenance costs, which the building owner will have to bear throughout a building’s lifetime.
Heating and hot-water suppliers have to work within these constraints, but we also have a responsibility to do our bit to narrow the performance gap to the best of our ability. By designing solutions that are flexible enough to adapt to changing demand patterns and operating conditions, at least we can solve our part of the performance puzzle.
David Pepper is managing director of Lochinvar.