An installation is not complete without commissioning
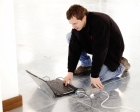
The difference between a newly installed air-conditioning system working perfectly or not at all can be down to a methodical commissioning process, says Martyn Ives of Fujitsu.
All too often, commissioning is thought of as something you only need to consider at the end of an installation when it should be something that is as much part of a project as correctly positioning the units.
At the end of a project, when the customer sees all the equipment is in place but not yet working, there is always a lot of pressure to get the units going as soon as possible. However, not carrying out a thorough, methodical commission process may be the difference between a system working perfectly or not working at all.
The irony is that, with a bit of planning, commissioning does not have to be left entirely to the end. It can be done throughout the installation.
For example the addressing of the indoor unit can be done when wiring the system as its covers are already off. This is a perfect time to label the indoor unit with the port and the system address.
There are five main steps to ensuring an air-conditioning system works to the optimum.
• design
• installation
• commissioning
• operation
• maintenance.
Each step is as important as the other, and the correct amount of time should be allocated to each.
Even something as basic as calculating the additional refrigerant charge correctly is very important. Overcharging and undercharging will cause the system to run inefficiently and, in some cases, to malfunction.
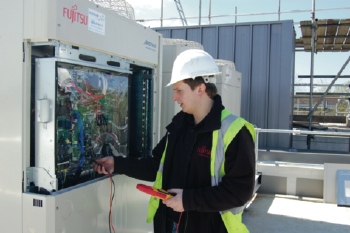
Addressing the system so the indoor units will talk to the outdoor units properly can be one of the areas that gives the most problems; the larger the system, the more involved the process.
While VRF systems are simpler to commission than they used to be, it is still worth double checking all the units have the right address. Incorrect addressing of units can result in the end users thinking they are changing the settings for a wall-mount in an office when they are really adjusting the ducted unit in the showroom. The result is a dissatisfied customer and an unnecessary, unbillable callout.
Many systems offer auto-addressing as well as manual. However, auto-addressing does not address in a logical way so adjacent rooms can be wide apart in the numbering system, adding an extra complication for the service engineer.
To help with commissioning, Fujitsu offers a powerful piece of software called Service Tool, which allows the commissioning or service engineer to check that all address settings are correct, and view all temperature and pressure readings from condensers. It also monitors running currents, valve controls, compressor frequencies, amps, and fan speeds. On the indoor units it can monitor temperatures, fan speeds, valve control and operation mode.
Installers who are worried about the commissioning process or simply do not want to tackle it can often turn to the manufacturer to provide a commissioning service and commissioning training courses.
Not all aspects of commissioning are quite so technical. For example, it is imperative to ensure the installation is correct to the design schematics supplied by the manufacturer. Visual checks need to be made on all pipework and fittings before the builder makes them inaccessible. These checks should ensure that the pipework is supported correctly and well insulated. The checks should also ensure that separation tubes and refrigerant branch boxes are installed at the correct angle, as shown in the installation manual.
Even more low-tech is checking that the system is achieving the right temperatures and there are no undesirable noises.
As well as the mechanics and electronics of the system, it is just as important to show anyone who is likely to be able to adjust the controls how to do it properly without causing problems. Contractors should also assure themselves that the end users know who to contact if things go wrong and how to contact them.
This procedure is more than just running the office manager through the basics in five minutes flat and ignoring the blank expression. It requires producing clear and concise written instructions that stay with the system and can be used by whoever takes over when that office manager goes on holiday or leaves. When the operation of the system is disrupted by an end user, it is the system or the installer that gets the blame, not the end user. Carrying out a proper handover is simple self-preservation.
A good commissioning process is the seed of tomorrow’s market growth as it ensures end user satisfaction and repeat business. The time to think about it is at the design and planning stage, not just before the handover.
Martyn Ives is technical manager with Fujitsu.