Removing heat at source
Traditionally the way to deal with heat generated by server racks in an IT suite or data centre has been to allow the fans in the blade servers to draw room air through the racks to remove the heat and reject it into the space. The task for the building-services engineer is then to remove that heat from the air to maintain the required conditions. Humidification may also be required.
The task becomes more challenging as heat densities within the racks increase. One technique successfully deployed is for hot aisles to contain hot air rejected from the server racks rather than allowing it to dissipate throughout the space. This approach then reduces the amount of air that AHUs have to handle, albeit at a higher temperature.
Another more energy-efficient approach, which has numerous benefits, is to absorb the heat from the air at source at the rack and then cool via a chilled-water circuit so that the air is returned to the space at the same temperature, giving the space a room-neutral effect.
It’s an approach that Eaton-Williams has considerable expertise in, as Dimitri Rocchiccioli, the company’s export manager explains: ‘Heat is removed from the rack and is passed through a rear-door heat exchanger (RDHx) that contains a chilled-water cooling coil. An RDHx can be active (with fans to help draw air through the rack) or passive.’
An active RDHx can remove up to 55 kW of heat, and a passive rear door heat exchanger can remove up to 30 kW of heat — but Dimitri Rocchiccioli points out that a standard application is typically 15 to 25 kW per rack.
It is important to avoid moisture condensing from the air being cooled, so the flow/return temperature is around 16/22°C. The cooling provided is therefore entirely sensible cooling.
The Eaton-Williams approach uses its ServerCool range of data-centre cooling solutions, and the chilled water for the RDHxs is supplied by ServerCool’s cooling distribution units (CDUs) serving the rear-door heat exchangers. One CDU delivers a total of 305 kW of cooling and can supply up to 18 racks. The CDUs themselves receive chilled water either from a dedicated chiller or within the building’s chilled-water system, with the primary flow/return temperatures typically being 7/12°C.
The CDUs are connected to the RDHxs by flexible hoses with quick-release couplings, which makes changes to the layout fast, simple and flexible.
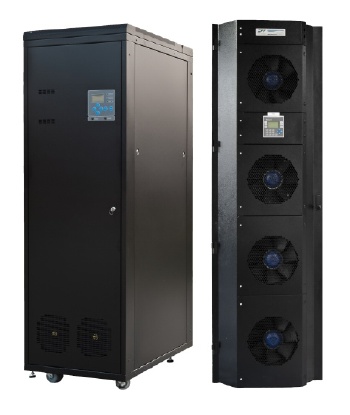
For smaller installations, a CDU module can supply up to 20 kW of cooling to three RDHxs.
Eaton-Williams also supplies CRAC (computer-room air-conditioning) units, which can complement the rear-door cooling approach.
Dimitri Rocchiccioli refers to independent tests carried out on Eaton-Williams passive rear doors by the Silicon Valley Leadership Group (SVLG) at Lawrence Berkley Labs in California for racks with heat loads of up to 10 kW.
The CDU with 305 kW of cooling absorbs only 4.1 kW of power, which makes this solution very energy efficient, offering lower PUE (power usage effectiveness) compared to other more traditional cooling solutions.
Rear-door heat exchangers are well suited to large data centres, but can also be used in small server rooms with just one rack. The approach is to install CDU modules in servers contained within a small number of racks. Eaton-Williams can offer various models including the CDU 20 which can be installed into 6U of rack space. Eaton-Williams can also provide CDUs for chip cooling
‘But why,’ asks Dimitri Rocchiccioli, ‘remove the heat from air after it has been drawn through a server rack? Cooling technology is moving at a very fast pace, and chilled-water circuits are now being used to remove heat from the actual source of the heat — the high-powered chips themselves.’