Controls — the ultimate quick fix
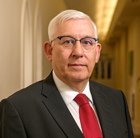
Malcolm Anson of the Building Controls Industry Association offers a quick method for getting to grips with controls and using them more effectively for better energy efficiency.
The combination of legislation and energy prices continues to drive building owners and facilities managers to search for energy savings. Installing more energy efficient equipment and altering the building fabric are effective disruptive and time-consuming measures to take, requiring significant capital spend.
But there are smarter, faster and more cost-effective methods to reduce energy use in a timely way. What’s more, there is a strong possibility that most building managers already have the tools to do the job.
If you manage any kind of building, it's a safe bet that you have the controls currently installed that, with a better grasp on their basic use, will allow you to start saving money very quickly. A well-run building energy management system (BEMS) can reduce building operating costs while providing invaluable information on other potential energy-savings.
Through proper operation of a BEMS, energy waste can be reduced to a minimum because building plant only operates when it is required. Furthermore, a correctly operated BEMS ensures that services are only provided when they are needed, so competing services (such as heating and cooling) do not fight against each other. These benefits not only reduce energy waste but they also keep down maintenance costs because machinery is not operating unnecessarily.
The first step to securing these benefits is to perform a simple survey of all your building’s controls. It is surprising how many building managers or FMs do not really know what controls they have within their building. This can happen because of poor handover of a new building, or simply because facilities staff leave and a new team is not fully trained.
Basic control systems check — low cost with massive savings • Make sure control panel switches are in auto, not manual. • Check time switches /optimisers (soft and digital) are set to correct time and day. • Are extension timers and frost thermostats working correctly? • Are frost settings correct? • Are all motorised valves working electrically and mechanically? • Adjust the flow temperature in variable-temperature heating systems to ensure boilers condense. • Link boiler flow temperature to follow variable-temperature valve slope. • Review all time settings — building usage may have changed. • Install extension timers — don’t just run plant on time clocks in case it is needed! Low-cost additions to a BMS Check that control algorithms include the following. • Sensor in boiler flow, to notify FM if flow temperature is high for a number of minutes after plant shut down • A hold off of heating if external temp is above, say, 18°C. • Interlocks to ensure heating/natural ventilation/mechanical cooling do not overlap. • Use averaging space temperature sensors. If there’s no signal for heat from them there will be no heating plant running. • If there is not a variable-temperature valve, modulate boilers directly — don’t run at 82°C. Medium cost additions to a BMS • Outside lighting control using time control and lux sensor. • Add in additional zone controls. • Use inverter-controlled pumps. • Use a web-browser-capable controller to monitor adjust settings remotely for reactive control — saving time and money on site visits. |
Many buildings will already have a BEMS in place, so facilities managers need to evaluate the existing system to decide if it meets present and potential future needs.
The answers to these questions will hinge on factors such as type and age of the system, and the current state of its operability. It is important to consider if upgrading is possible, or if replacement is a more sensible route for the long-term.
The critical questions to ask are the following.
• What are the energy-management requirements of the building? Does the existing system meet address them?
• Will the site’s energy-management requirements change over the next few years, and is the current system equipped to cater to those changes?
• Is the BEMS being appropriately and fully utilised? Is everyone who uses the system properly trained to do so?
Involving the right people and following the correct processes in an assessment of the status quo are two key elements. The Building Controls Industry Association (recommends the following steps.
1.Involve the people who are monitoring and using the BEMS every day. They will be able to tell you how the system operates as they see it, and should have an understanding on what is missing that would be beneficial to add.
2.Involve the contractor who is maintaining your building controls because a second opinion is also useful if you’re considering an upgrade.
3.Perform a technical assessment of the BEMS — including the design requirements, control strategies and the physical equipment in your building that require control.
4.This evaluation also provides an opportunity to review the operation of mechanical and electrical plant.
5.Document changes and observations from the evaluation process. The main outcomes you should be looking for are: an assessment of how well the BEMS currently operates; any training requirements for users; potential cost savings from re-commissioning existing plant; assessment of cost-benefits of upgrading, including the financial benefits of improved energy efficient control and operation.
The outcome from this process will give the facilities manager a far greater understanding of the system and a clear idea of what is needed to improve it.
When this process has been completed, the result is a far more accurate understanding of what controls technology is available in the building, and also how people are using it.
It seems surprising, but so often BCIA members find that controls have been set to ‘manual override’ for months, leaving equipment operating 24 hours a day. This sort of issue can be picked up very quickly once a systematic survey is undertaken — and the savings can be very significant for very little effort.
Malcolm Anson is president of the Building Controls Industry Association and managing director of Clarkson Controls.