Controls and services in sync.
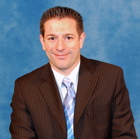
Making alterations to a building and its services without making corresponding changes to the controls will quickly lead to poor performance and increased energy consumption. controls are not fit-and-forget technology — as Matt Peasnall of Trend Control Systems, explains.
When a BEMS (building and energy-management system) is first commissioned it is configured around a specific building layout. While this might be perfect initially, buildings naturally evolve. Alterations such as repartitioning, different occupancy patterns, the addition or relocation of equipment and wear and tear to plant infrastructure can quickly lead to inefficiencies that result in higher energy bills, lower employee productivity, poor comfort conditions and increased building maintenance costs.
A simple but extremely common example is electrical equipment such as a photocopier being placed near a temperature sensor. This increases the temperature around the sensor, which will then call for cool air to reduce it. The cool airflow will affect adjacent controlled zones and people will feel colder and use fan heaters to warm up. This ‘heating-fighting-cooling’ scenario is all too-typical in buildings and will negatively affect energy consumption.
A BEMS itself is also not immune to performance deterioration, and incorrectly configured time clocks and setpoints can have negative repercussions on overall performance. The quality of the control offered can gradually deteriorate due to factors such as loss of sensor accuracy and unnecessary system over-rides. As a result, a BEMS needs to be kept up to speed with the building usage and should always be considered a fundamental part of the building’s infrastructure, not simply a ‘fit and forget’ element.
It is incredibly frustrating that some organisations fail to maximise the potential of a resource that they’ve already paid for and have right under their noses. All too often recommissioning becomes one of those ‘we’ll-do-it-tomorrow’ type jobs. This must not be the case, and breaking down the service regime into bite-sized chunks will make the task less onerous.
One of the obvious elements is to enable the BEMS to automatically adapt to the different ways the building is used throughout the year with seasonal fluctuations. It is also vital to consider changes in occupancy patterns. For example, schools and other educational establishments will be unoccupied for extended periods of time, so there’s no point heating being on 24/7 when they are only occupied between 8 am and 5 pm during term time and not at all during holidays.
Again, schools have a tendency to undertake moves and changes during the summer holidays, so a building layout used in the spring could be replaced by something quite different when the academic year starts again in September. Not adjusting setpoints to compensate for these changes could easily lead to a BEMS that doesn’t do its job properly.
Very often a continuous commissioning regime will highlight adjustments which should be made that will deliver immediate savings, i.e. the replacement, calibration and relocation of space temperature sensors and the verification of energy-efficiency control strategies such as optimum start, resets and load control. The introduction of BEMS-based software tools can ‘learn’ how a building operates and automatically adjust control parameters by running algorithms that optimise efficiency.
Through the correct implementation of control strategies and tools, the BEMS can be directed to highlight areas of concern for further investigation, allowing building owners to react quickly and effectively to potential issues.
Depending on what’s involved, the implementation of a continuous commissioning regime can be carried out by in-house staff, the BEMS manufacturer, or approved third-party integrators. Scheduled changes and setpoint adjustments are pretty straightforward. However, when it comes to more advanced work, a service-level agreement is always recommended to ensure a continual loop of feedback and prevent gaps in provision, thereby maximising energy savings and occupancy comfort.
All building owners, facilities managers and occupants require greater visibility and transparency of their energy consumption and need access to relevant data. The benefits of ensuring the BEMS is commissioned correctly and optimised to match current operating requirements are obvious — enabling building services to operate in strict accordance with demand, thereby avoiding unnecessary energy use and making it truly fit for purpose.
Just as importantly, a BEMS operating at its optimum will significantly decrease wear and tear on HVAC plant and prolong the life of these expensive assets.
Matt Peasnall is projects and service director at Trend Control Systems.