The role of big data in unlocking BMS efficiency

Without an effective building management system (BMS) monitoring strategy, seemingly small inefficiencies can result in rapidly mounting costs if left undetected, says Wago’s Steve Emberton. By harnessing big data, a building’s systems can avoid downtime and deliver more energy savings in the future through ongoing optimisation and elimination of wasteful practices.
Big data is not exactly a new concept, but it still has yet to be embraced by all in the buildings industry. And yet the benefits can be substantial. Storing a week’s worth of building data allows building-service managers to refer to the previous week for a side-by-side comparison of data trends. However storing a month, a year, or several years of data allows true data analysis to take place
That said, there is little value in storing data unless it is actually utilised, and the power of big data is only unlocked when that data is analysed and turned into meaningful information that can be used to make efficiency improvements.
Powerful analytics programs can be used to search the data and locate trends, relationships, correlations, hidden patterns, or maxed-out values. The information gleaned can be used to make informed adjustments to a building’s operation, from minor schedule and set-point changes to reprogramming of the control system, or physical changes to the building’s plant equipment. A small change may not make much impact on energy usage on its own, but many small changes can quickly add up to substantial overall savings.
Take scheduling for instance. Traditionally the world used to work five days a week from nine to five; however this is increasingly no longer the case. As such, the way buildings are operated needs to reflect the changes in our modern working practices.
The strict regime of fixed on/off times is long gone in favour of optimum start and stopping of main building plant to ensure buildings are at an ideal working environment as workers walk through the door and that equipment powers down at the end of the day so as not to waste energy when everyone has gone home. Analytics can look at the occupancy trends and determine what these times are likely to be on any given day; and the more data we have, the more we can fine-tune to ensure optimal climate and maximum efficiency.
Modern building-management systems are capable of highly complex scheduling, allowing individual parameters to be configured for very small areas. This means that unusual events or seasonal changes in occupancy can be accommodated, and new temporary or recurring schedules can be created to ensure that equipment is only running when it needs to be at any given time.
Dropping a fixed set point for an environment by 1 K can lead to as much as a 3% energy saving. However, simply reducing the temperature is clearly not a viable solution once it starts adversely affecting comfort. Indeed, temperature is not the only factor to consider, as comfort and productivity are affected by a number of other elements such as air quality, light levels, occupant behaviour, location, equipment and more.
Set points should therefore be dynamic in operation, algorithmically monitoring atmospheric variables and using them to provide a complete picture of building performance. The goal is to understand not just where set points can be changed, but why segments are performing differently, and what the knock on effects will therefore be for other building segments and systems. This helps to determine where improvements can be made, and what impact any changes will have on energy levels.
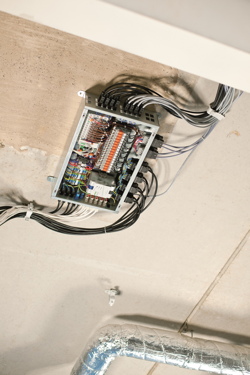
A common strategy for optimising space temperature set points is to have separate heating and cooling set-points, or one set point with a wide dead-band. This prevents heating and cooling systems from fighting with each other and ultimately cancelling out while wasting large amounts of energy unnecessarily.
If alarms are poorly defined and easily set off, an operator may be tempted to acknowledge them without review simply to stop them from being a nuisance. However, this is an incredibly bad habit to get into, as one day a significant alarm will come along that could cause real damage. That said, it is unfair to blame this solely on human behaviour, as poorly configured and displayed alarms will inevitably lead to confusion and apathy.
Instead, it is far better to ‘drill down’ via a graphical representation of the building, using traffic-light-style alarming to view the item of plant at fault. Maintenance personnel will be happy to see their building with a healthy green glow around it, and this also enables quick identification and remedying of faults. Such a system is also ideal for conveying energy usage, which can identify inefficiencies that fall short of triggering fault alarms.
Energy usage of individual components is rarely monitored by a BMS, but it has the potential to make a huge difference. For example, if a filter flow alarm on an air-handling unit is ignored, the supply fan speed will be increased by the BMS to maintain the correct airflow, and as such the power used will increase and generate an energy alarm that can be investigated. This sort of usage of data is typical of using analytics rather than a hard-wired alarm.
Storing data for no specific purpose is a form of inefficiency in itself, as data storage has a cost implication. It is therefore crucial to leverage as much of the accumulated data as possible. Monitoring and trending of data increasingly exists in a virtual world where data analytics is now taking over from human judgement and studying printed graphs. Building-management systems such as Wago’s flexROOM system have a high degree of adaptability in order to utilise data to make proactive parameter changes based on the requirements for individual floors, rooms and segments. Efficiency alarms like the example described above will increasingly come from analysis of big data, and enable operators to extract those incremental improvements that come together to deliver significantly reduced overall costs.
Steve Emberton is building automation manager with Wago.